Pallet racks are a crucial part of any warehouse or storage facility. However, with the benefits of warehouse racks come safety concerns that you must address to maintain a safe and efficient workplace.
Pallet racks in a warehouse can be risky if not installed or maintained correctly, as they may collapse and cause injuries. But even well-maintained warehouse racks can be damaged by workers or equipment.
This blog post will answer the top 5 questions about pallet rack safety.
- Do I need load capacities displayed on my racks?
- Can I use plywood instead of wire mesh decking?
- Is it safe to repair a damaged rack?
- Who can inspect racks for safety, and how often should they be inspected?
- Do racks need to be anchored to the ground?
Whether you’re a warehouse manager, a safety professional, or someone interested in pallet rack safety, this article is for you. So, let’s dive in and explore the five common racking questions.
1 - Do I need load capacities displayed on my racks?
Yes, rack load capacities are critical to the safe operation of your warehouse.
Due to safety regulations for pallet racks in North America and increasing demand for enhanced warehouse safety, it’s mandatory to have and display the rack capacity on the rack or in its vicinity.
Did you know that WorkSafe B.C. fined a construction company
more than $330,000 due to damaged racks, including their failure to
provide information regarding the rated capacity of their racks?
What are load capacities?
When it comes to warehouse safety, load capacities are a critical consideration.
A pallet rack load capacity determines the maximum weight limit a particular rack can support. Exceeding that limit can cause rack columns to become unstable, increasing the risk of collapse and employee injuries. For example, a rack designed to hold lightweight items should not be used to store heavy, bulky items, as this can lead to overloading and instability.
In addition to preventing overloading, load capacity displays can be helpful tools for conducting regular safety inspections. By checking them during inspections, you can identify any racks that may be at risk and take corrective action before a disaster occurs.
What is the responsibility of the rack owner?
The ANSI/RMI Standard mandates the display of load plaques in rack installations. It’s worth mentioning that building and safety inspectors may require the installation of such plaques. The plaques must include specific information such as:
- Maximum permissible unit load (i.e., the total weight of the product and its storage container or pallet), as well as the maximum uniformly distributed load per level.
- Average unit load, if applicable (typically calculated by dividing the maximum total product weight by the number of beam levels in the row).
- Maximum total load per bay.
It’s important to note that any changes to the rack’s configuration must be evaluated, like adjusting the beam’s height or removing/replacing a beam with different specifications. A qualified rack design engineer must recalculate the system’s capacity, create new load plaques, and attach them to the rack system to ensure that the load capacity is accurately reflected.
Were you aware that in Canada, only a professional engineer
is authorized and insured to determine the load capacity
of a pallet rack system?
Where should load capacities be displayed?
The load capacities should be marked and visible to all workers using the warehouse racks.
There are several ways of communicating the load capacity of a racking system. One can use adhesive labels placed on the first beam (at eye level) since it allows for a varying load capacity throughout a rack system. Load capacity labels placed on each bay are the most common ways of displaying this information.
If your racks have the same load capacity throughout, you may use rated load plaques at the end of the aisles to remind the forklift operators of the rack load capacity before entering that aisle. It ensures that the maximum load capacity is communicated to forklift operators so they do not overload the racks.
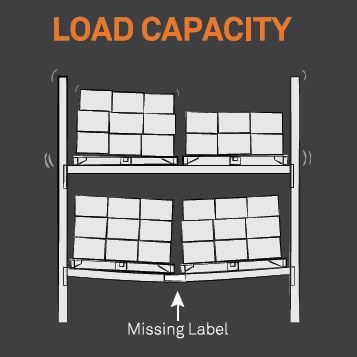
Importance of displaying load capacities on racks
So, do you need load capacities displayed on your racks? The answer is a resounding yes.
By clearly displaying load capacities on racks, you can help to prevent overloading, ensure even loading, promote proper rack usage, and facilitate regular safety inspections. If you haven’t already done so, display certified load capacities on your racks today.
We can assist if you need clarification on your system’s load capacity. Our qualified engineers have commercial pallet racking expertise and can determine the maximum beam capacity through sophisticated modeling and calculations. Our non-disruptive process includes producing all required labels or plaques to correctly display weight capacities for your racking systems.
SPEAK TO AN EXPERT CONCERNING
WEIGHT CAPACITY CALCULATIONS FOR YOUR PALLET RACKS.
2 - Can I use plywood instead of wire mesh decking?
A few options for pallet rack decking are available, but the most common ones are wood and wire mesh decking. Wire decking is still popular for pallet rack systems. Plywood or timber can sometimes provide an interesting alternative.
To answer the main question, we need to consider various factors:
- The purpose of the decking.
- The load capacity.
- The fire safety.
- The cost-effectiveness of the materials.
Purpose of the decking
Wire mesh decking provides better airflow, visibility, and drainage, which is especially important for storing products that require good ventilation or have fire safety concerns.
Plywood decking, on the other hand, may not provide the same level of ventilation or drainage. Therefore, it may only be suitable for some products.
Load capacity of the decking
Pallet rack wire decking is designed to support heavy loads and has a higher capacity than plywood decking. It would be better if the racking system is intended to hold heavy loads. Additionally, wire mesh decking is more resistant to damage from heavy items.
Plywood may be acceptable when storing lighter-weight products or when items packaged in boxes are not likely to damage the plywood, such as in a picking area without pallets. Additionally, it can help prevent smaller items from falling through the decking
ARE YOU UNSURE OF YOUR RACKS’ CONFORMITY?
CONTACT AN EXPERT TODAY!
Fire safety
Wire decking for commercial pallet racking is more fire-resistant. It allows smoke and heat to rise, and sprinkler water can reach the lower levels through the storage rack, reducing the risk of fire damage to the stored products.
In contrast, plywood is combustible and may pose a fire hazard in certain situations. With a ceiling-only sprinkler system, water cannot reach the fire if it is blocked by wood decking.
Cost-effectiveness
Wire mesh decking tends to be more expensive than plywood, but it is more durable and has a longer lifespan.
Plywood decking may be a cheaper alternative but requires frequent replacement and maintenance.
Here are other things to consider surrounding the use of wood as decking:
- Dirt may accumulate on the plywood over time. Not as much when using wire mesh.
- Plywood decking can fall from the rack and become a hazard. They should be fixed to the beams.
- Plywood may block overhead lighting and reduce visibility into the racking system.
Key takeaways for choosing between wood and wire mesh decking
Ultimately, the decision of whether to use plywood or wire mesh decking will depend on the specific needs of your warehouse and the products you are storing. When deciding, it is essential to consider the weight and nature of the products, the level of protection required, and the budget for the decking.
While the Rack Design Code MH16.1 (RMI) does not provide specific guidelines regarding decking use, we recommend wire mesh decking based on the benefits mentioned below.
Wire Mesh
Pros
• Protects from falling objects.
• Durable material with a longer lifespan.
• Openings let sprinkler water reach lower levels (to prevent fire damage better).
• Better airflow and visibility.
• A variety of wire mesh decking to fit different beams.
Cons
• More expensive than wood decking.
• Ensure decking is not deformed/detached from beams.
Wood
Pros
• Affordable solution.
• For storing smaller hand-picked items.
Cons
• Properties can degrade over time (rotting or cracking).
• Flammable material.
• Can obstruct water trickling down from fire sprinkler systems.
• Blocks overhead lighting.
• Prone to accumulate dirt and debris.
3 - Is it safe to repair a damaged rack?
Warehouse racks are designed to support heavy loads, and any damage to the racking system can compromise the safety of the entire structure.
If you notice any damage, it’s crucial to remove the affected rack from service immediately and have it inspected by a qualified professional. This expert can determine the extent of the damage and whether the rack can be safely repaired.
It is important to note that repairs should only be attempted by properly trained and qualified professionals. Trying to repair a damaged racking system yourself can be hazardous. Improper repairs can lead to further damage or even the collapse of the rack, putting workers and products at risk.
Therefore, it’s essential to seek professional assistance when repairing a damaged racking system. Rack experts have the expertise and experience to identify and address any damage to the racking system safely and effectively. They can also provide recommendations for any necessary repairs or replacements to ensure the safety and longevity of the racking system.
While replacing entire uprights can be lengthy and costly, cost-effective repair services and products are available. These options can reduce downtime and maintenance costs and save valuable time.
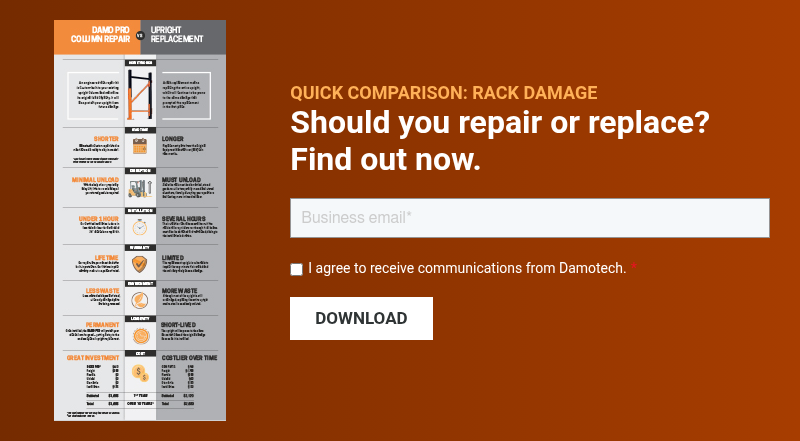
Key takeaways for repairing damaged pallet racking systems
In conclusion, always prioritize safety when dealing with commercial pallet racking. Don’t attempt to repair damaged pallet racks yourself; seek professional assistance to ensure the safety and stability of the racking system.
Repairing damaged racks can save you money in the long run. A professional can identify and repair minor damages before they become more significant problems that require costly replacements. By repairing damaged racks promptly, you can extend the life of your racking system and avoid unnecessary costs associated with replacing an entire rack.
4 - Who can inspect racks for safety, and how often should they be inspected?
Pallet racks are subject to wear and tear, damage, and other issues that can compromise their safety and integrity, such as collisions and overloading. Have your warehouse racks regularly inspected to ensure they are safe and in good condition.
Who can inspect a rack?
Trained and qualified professionals should perform inspections of warehouse pallet racks.
Professional rack safety experts have the necessary training, knowledge, and expertise to identify safety hazards, assess the condition of the racking system, and recommend appropriate corrective actions. They are also well-versed in safety regulations and can ensure that the racking system follows safety standards.
Conducting a comprehensive third-party inspection before undergoing an OSHA audit is highly advisable. This inspection should evaluate the condition of your warehouse’s pallet racking systems to identify any issues hindering compliance with OSHA regulations. They may include improper pallet rack installation, hazardous damage, unposted capacity, or unsafe modification. Addressing these concerns before an OSHA visit can help you avoid potential fines and temporary suspension of operations.
How often should racks be inspected?
Rack inspections should be conducted regularly to identify any damage before it becomes dangerous and poses a risk of accidents. The frequency of inspections depends on several factors, including the type of rack, the load capacity, the level of use, and the environmental conditions in which the rack is located.
As a general guideline, a professional rack inspector should inspect racking systems at least once a year. However, more frequent inspections may be required in high-traffic facilities or those with heavy usage or frequent loading and unloading.
Additionally, it is recommended that warehouse racks be inspected after any damage or significant change to the rack system occurs, such as:
- Collisions.
- Overloading.
- Seismic activity.
- Other incidents possibly compromising the safety of the racking system.
As well as annual inspections, conducting thorough monthly checks of your industrial pallet racks is crucial. Warehouse personnel should be trained to identify any visible damage or signs of wear and tear, such as bent or broken beams, loose connections, or missing bolts. Any damages found should be reported to the rack safety expert for further inspection and repair.
Ensuring safety and longevity with routine pallet rack inspections
Regular pallet rack inspections by qualified professionals are fundamental for maintaining a safe and efficient warehouse environment. Promptly addressing any damage or issues found during inspections can ensure the longevity of your pallet racking system.
Regular inspections by professionals and warehouse personnel can help prevent accidents and optimize business operations.
5 - Do racks need to be bolted to the ground?
Yes, pallet racks should be anchored to a concrete slab to ensure stability, provide resistance to small impacts, and prevent them from tipping over.
OSHA has taken measures to ensure that businesses that do not correctly anchor their commercial pallet racking are cited for violations. Although avoiding a fine from OSHA is a significant motivator to fasten your racks securely, the potential risks of employee injury or structural damage to the building associated with an unstable rack are more compelling reasons.
Furthermore, if a forklift collides with an unanchored pallet rack, it could trigger a catastrophic chain reaction, like a domino effect, if the surrounding racks are not adequately strengthened. It would result in significant losses ranging from thousands to millions of dollars in damaged inventory.
The anchoring method used for warehouse racks can vary depending on the specific installation site and type of rack. Some common anchoring methods include wedge anchors, screw anchors, or sleeve anchors.
To ensure the appropriate anchoring technique is used for a specific application, seek the advice of a professional engineer or installer. Following the manufacturer’s recommendations and applicable regulations or standards is crucial when selecting and installing anchors. The Rack Manufacturers Institute’s guidelines provide suggestions on the suitable anchor bolts to use for pallet racks. Additionally, please note that seismic anchors are necessary for racks in areas with a high risk of earthquakes.
In addition, regular inspections of rack anchors are also essential for maintaining the racking system’s safety. Over time, anchors may loosen or become damaged, compromising the stability of the racks. Qualified rack safety experts should perform inspections at least once a year to ensure proper safety. If any damage, such as cracks or splits in the concrete or bolts, is detected, they should be addressed immediately.
Key Takeaways for anchoring pallet racks
Properly anchoring warehouse racks to the floor or foundation is necessary to prevent accidents and injuries. The appropriate anchoring method should be determined based on the floor type and load capacity, and regular inspections should be carried out to ensure that the anchoring remains secure.
Regular inspections are also important to ensure that the anchors are still effective. By taking these measures, you can ensure the stability of your racking system.
CONCLUSION: Prioritizing Pallet Rack Safety for a Safer and More Productive Warehouse.
Pallet rack safety is a crucial aspect of warehouse safety that cannot be overlooked. As we have discussed, several factors are needed, from load capacity and inspection to rack repair. Given the complexity and potential risks involved, it is understandable that rack safety can be daunting for many warehouse operators.
Partnering with a rack safety expert can make it easier to ensure your commercial pallet racking are safe and compliant with relevant regulations and standards. These experts have the knowledge and experience to help you navigate the complexities of rack safety and implement effective measures to prevent accidents and injuries in your warehouse.
Taking a proactive approach to rack safety can create a safer and more productive work environment for everyone involved.