Racks are highly efficient structures, but they require components to be free from damage to bear the loads placed on them. Indeed, in their simplest form, racks are meant to support stored goods or loads. When they are first designed and installed, their load capacity is established to perform this duty very well, provided they remain intact. But accidents happen and over the years, several factors can lead to an unsafe racking situation.
What causes racks to become unsafe?
A multitude of factors contribute to an unsafe racking system. Here are just a few:
Impacts from forklifts | Inadequate aisle widths for equipment used |
Beam elevation changes or removal | Harsh operating environment |
Overloading racking systems | Lack of rack safety training and awareness |
Priority on speed instead of safety | Complacency |
1. Impacts from forklifts
This is perhaps the most apparent cause of rack damage and failures. Pallet racks are not built to withstand impacts; they are intended to bear loads. While there are many types of rack damage, the frame doesn't need to be severely impacted to pose a safety risk. Accumulated damage leads to a weakened structure that may no longer be able to support loads. Once a rack component has been dented or deformed, particularly near the base of the system or the junctions, it will no longer carry its rated load capacity.
2. Beam changes or removal
Changing the configuration of a racking system (without consulting an engineer or the rack supplier) is another factor that can cause the system to become unsafe. Moving a beam's height up or down or removing one level of beams in your rack is considered a change in configuration. After such changes, the rack can still support loads, but it won't support the maximum design load (watch our explainer video).
3. Overloading racking systems
Overloading a rack can cause permanent deformation of the beams or beam connectors. Loads should be evenly distributed in the rack. To know the maximum load capacity of a rack, refer to the original Load Application and Rack Configuration (LARC) drawings.
4. Priority on speed instead of safety
What is your warehouse safety culture like? Are you paying for speed or promoting safety above all? To the extent we are picking at a certain pace because we're in a peak period, rack safety will inevitably take a back seat to that speed. So, to the extent we have that culture within the warehouse, we will see a potential drop in rack safety.
5. Inadequate aisle widths for equipment used
Upon their planning, rack systems are designed to be integrated with specified lifting equipment. When lift trucks have limited space to maneuver, they can inadvertently hit the racking systems and damage them. We recently share a formula to determine how much aisle space is needed in your aisles. Read the article about aisle widths.
6. Harsh operating environment
Does cold storage make things unsafe? Of course not. However, harsh conditions add a layer of complexity and challenge to operations in such environments, which can lead to hazardous situations or unsafe practices and ultimately impact rack safety. For instance, moisture on a pallet racking system made from steel can cause the rack to rust. Rust can undermine the structural integrity of the racking system and lead to the system's failure or collapse.
7. Lack of rack safety training and awareness
Lift drivers are trained to drive a forklift and taught proper loading and unloading techniques, but they may lack awareness about rack safety. Since forklift impacts are among the leading causes of rack damage, we should pay attention to their training. It is the rack owner's responsibility to inform drivers of the effects of forklift impacts on pallet racks. When they are adequately trained to prevent and recognize rack issues, everyone's safety is improved. If employee turnover is high, implement regular training sessions to keep everyone informed and keep safety procedures top of mind.
8. Complacency
Ultimately, if we don't address the damage in our warehouse, we become complacent, and complacency could be safety's worst enemy! A lack of regular rack inspections and maintenance program, or if rack damage is mostly being ignored and not addressed, lead to an unsafe racking situation.
Although racks appear to be pretty straightforward, many things can go wrong. They can pose a threat to those working in and around them if they are misused or become weakened by cumulative damage. As part of your warehouse's maintenance and safety program, make sure to schedule regular inspections, so no racking issues go unnoticed.
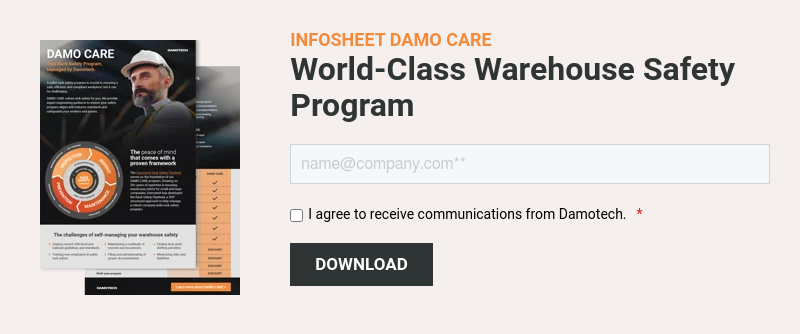