While warehouses are essential for the supply chain, warehouse work often involves heavy equipment, high shelves, and fast-paced operations, posing safety risks to employees.
Whether you’re a seasoned warehouse worker or new to the industry, these safety tips are essential for a secure and productive work environment. In this blog, we’ll explore essential workplace safety tips every warehouse employee should know.
1. Adopt Safe Lifting Techniques
Lifting heavy objects is a regular task for many workers, and it places a significant strain on the body, particularly on the back.
According to the Bureau of Labor Statistics (BLS), over 1 million employees experience back injuries annually, accounting for one in five incidents. Moreover, a substantial 25% of compensation claims are related to back injuries, resulting in significant financial costs to the industry, in addition to the physical and emotional toll on affected employees.
Lifting heavy objects is unavoidable for many employees, but there is a right way to do this potentially dangerous task.
However, other body parts can also sustain harm, whether from lifting a single heavy object or repeatedly lifting lighter ones. Some of the most common types of injuries associated with handling heavy objects in the workplace are fractures in the vertebrae, disc injuries, as well as wrist and elbow injuries.
Maintain proper posture
Use proper lifting techniques to prevent strains and injuries. Bend at your knees instead of your waist, minimizing pressure on the spine. Keep the load close to your body.
Avoid lifting heavy objects without help
When dealing with heavy lifts or awkward items, workers should use a forklift or seek the assistance of a colleague.
Minimize frequent and prolonged lifts
The risk of injury increases the longer someone holds an object aloft. Use stands, jigs, or other devices that eliminate the need to maintain an object at a considerable height.
2. Wear Appropriate Personal Protective Equipment (PPE)
According to OSHA, the correct usage of PPE can avert close to 40% of occupational injuries and illnesses. PPE acts as a barrier against workplace hazards. Always wear appropriate safety gear, including helmets, gloves, steel-toed boots, safety glasses, and high-visibility vests, as required.
Did you know that failure to wear appropriate PPE is responsible for
approximately 15% of injuries that lead to complete disability?
Every year, thousands of individuals suffer vision loss due to work-related eye injuries that could have been averted by appropriately choosing and using eye and face protection. In noisy workplaces, employees may experience hearing impairment unless they wear earplugs or earmuffs. Without protective gloves, they are at risk of lacerations to their hands and fingers. Head injuries may happen in the absence of hard hat protection.
3. Keep Aisles and Emergency Exits Clear
Cluttered and obstructed walkways can lead to accidents. The second most frequent cause of workplace injuries is related to trip or slip hazards that result in falls. 20 to 30% of workplace falls lead to moderate to severe injuries, such as deep bruising, fractures, or concussions.
In fact, per OSHA, slips, trips, and falls result in nearly 700 fatalities per year, constituting 15% of all workplace deaths!
Always maintain clear pathways by removing obstructions, spills, and debris. Use assigned storage locations and ensure materials are stored securely to prevent the risk of falling objects. Consistently perform cleaning and promptly identify and mark slip or trip hazards for safety in the workplace.
Additionally, avoid ever blocking an emergency exit door with any object, even if it’s just briefly. Emergency exits often become obstructed by items like ladders, carts, and even forklifts.
4. Follow Machine Safety Practices
Moving machine parts have the potential to cause serious workplace injuries, including crushed fingers or hands, amputations, burns, or blindness. Research suggests that approximately 30% of annual workplace injuries involve cuts and lacerations, such as scratches, abrasions, puncture wounds, needle sticks, and amputations.
If your job involves operating machinery such as forklifts, conveyor belts, or pallet jacks, it is crucial to undergo comprehensive training and obtain the required licensing.
Follow all safety procedures, including seatbelts, and don’t operate equipment recklessly. Always be aware of your surroundings and the presence of any pedestrian traffic. Thoroughly understand the operation and safety procedures associated with the machinery and equipment you handle.
Additionally, ensure that equipment emergency shutoff controls remain available, allowing for swift and unimpeded access to power down machinery if necessary.
5. Be Aware of Fire and Chemical Safety Procedures
Warehouses can contain flammable materials, making workplace fires and explosions a source of severe injuries and fatalities. According to the U.S. Bureau of Labor Statistics, each year, over 200 workers lose their lives, and more than 5,000 suffer injuries in work-related fires and explosions. While these occurrences are rare, they have the highest casualty rate among all possible workplace accidents.
The most frequent injuries resulting from work-related fires and explosions are skin burns, ranging from third-degree burns to first-degree burn injuries. Other common injuries linked to explosions and fires encompass:
- Broken bones
- Lung damage due to smoke inhalation
- Cuts or lacerations, particularly in explosion cases
- Concussions and other traumatic brain injuries (TBIs)
- Nerve damage
Familiarize yourself with the locations of fire extinguishers and emergency exits. Participate in regular fire drills and comprehensive safety training sessions to be informed about the appropriate steps to take in the event of a fire.
If you need to handle chemicals or hazardous materials, ensure you understand the proper storage and handling procedures. Always wear the recommended PPE and be aware of chemical labels and safety data sheets (SDS).
6. Report Hazardous Conditions
Maintain clear communication with your coworkers and supervisors. If you see a potentially unsafe situation or behavior, report it.
Notify supervisors of any near-miss incidents, accidents, or unsafe working conditions. It is instrumental in detecting and addressing potential hazards. Supervisors are legally mandated to provide a secure workplace for all staff, but this can only be achieved if employees communicate such concerns.
7. Get Familiar with First Aid and Emergency Response
Familiarize yourself with the locations of first aid kits and emergency response plans within your workplace. Make sure you know the fundamental first aid procedures and the correct steps to take in case of an injury or emergency.
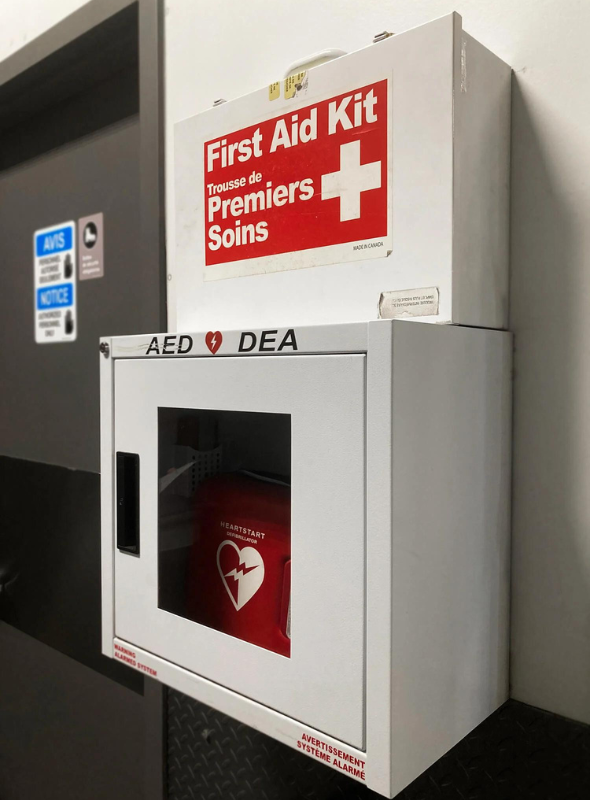
8. Stay Current Through Continuous Training and Education
Safety protocols and technology in warehouse settings are continuously advancing. Stay informed through regular training and keep up with the latest workplace safety practices and equipment to prevent accidents and injuries. If you’re unsure when to begin, consult your supervisor.
Recognizing potential hazards within your workplace and maintaining awareness of your surroundings are crucial. The more familiar you are with your job responsibilities and workplace environment, the better prepared you are to identify potential risks.
9. Stay Hydrated and Take Breaks
Physical exertion in a warehouse can lead to dehydration and fatigue. The greater your exhaustion, the more your awareness of your environment diminishes, making you more susceptible to potential injuries.
Drink plenty of water and listen to your body. Staying well-hydrated keeps you alert and attentive, allowing you to operate machinery safely.
Did you know that even a 3% decrease in hydration can have the same effect on a person’s reflexes as a 0.08 blood alcohol content, resulting in a higher likelihood of judgment errors and slower reaction times?
Take your designated breaks at the specified times to keep yourself alert and refreshed. OSHA has established these intervals for a specific purpose: fatigued employees are most susceptible to accidents. Additionally, consider organizing your more challenging tasks for the beginning of your shift when your alertness is at its peak.
Recognizing the signs and effects of dehydration is crucial for your well-being. Common indicators of dehydration include:
- Thirst
- Dizziness or light-headedness
- Muscle cramps or aches
- Dry mouth
And in more severe cases:
- Confusion
- Rapid breathing and heart rate
- Fever
- Fatigue
- Headaches
- Nausea
10. Pay Close Attention to Rack Weight Limits
Be mindful of the manufacturer’s load capacity assigned to each rack, which can be found on the rack’s load capacity label or plaque. If you notice that a label or plaque is missing, promptly inform your supervisor, as this information is mandatory.
Overloading racks is a common hazard that can result in structural damage and, in the worst cases, potential collapses. If you observe any signs of bending or deflection in the beams, take it as a clear indication that the rack carries more weight than it should. It’s crucial to maintain these weight limits to ensure everyone’s safety in the workplace and the integrity of the storage system.
Prioritizing Workplace Safety: A Shared Responsibility for All Warehouse Workers
In conclusion, safety in the workplace is a paramount concern for every warehouse worker.
By following these 10 workplace safety tips, you contribute to a safer and more productive workplace, protecting yourself and your coworkers from unnecessary accidents and injuries. Safety in the workplace should always be a top priority, and with ongoing vigilance, we can work together to create a secure and thriving warehouse environment.
If you ever need assistance or guidance on rack safety, feel free to contact a Damotech expert for expert support.
References:
- https://blr.com/resources/4-of-the-most-common-causes-of-workplace-injuries/
- https://essr.umd.edu/about/occupational-safety-health/ergonomics/back-injuries-fact-sheet
- https://petrocohen.com/blog/common-lifting-injuries-at-work-petro-cohen/