Across North America, many warehouses are used for the storage of hazardous materials. From gas cylinders to liquid paint, warehouse facilities are the most common sites where hazmat incidents occur. According to The United States Agency for Toxic Substances and Disease Registry (ATSDR), 75% of hazmat emergencies occur in storage facilities. Of these incidents, 36% involve the storage of incompatible chemicals, and 22% occur while using the wrong storage equipment. Accidents within a storage facility that contains hazardous materials can be dangerous for all warehouse occupants. Hazards can cause short to long-term effects. There are two different types of hazards: physical and health-related (Figure 1). Safety precautions and procedures exist to limit the occurrence of such accidents, such as the installation of labels, frequent inspections of goods, effective storage, and other useful safety measures. In this article, we will cover the different methods of safeguarding warehouse personnel from potential hazards and the preventative measures that can be implemented throughout the warehouse to encourage a safer workplace.
PHYSICAL Materials that present effects like: |
HEALTH Some of the health hazard classifications are: |
Fire Corrosion Reaction with other materials |
Acute toxicity Skin irritation Respiratory distress Eye Damage Long-term carcinogen effects |
Figure 1. Different types of hazards. |
Why Labelling Unsafe Substances Is Important
Labels are the easiest way to spot what kind of hazards you could be facing. Having the correct labels will not only help identify different substances that come into the warehouse but will also help when separating and organizing them. The table below shows the main labels and signs used to identify hazardous materials across North America:
CATEGORY | USA | CANADA |
Explosives | ![]() |
![]() |
Gases | ![]() |
![]() |
Flammable & Combustible Liquids | ![]() |
![]() |
Flammable Solids | ![]() |
![]() |
Oxidizing Substances & Organic Peroxides | ![]() |
![]() |
Toxic Infectious Substances | ![]() |
![]() |
Radioactive Materials | ![]() |
![]() |
Corrosives | ![]() |
![]() |
Miscellaneous Dangerous Goods | ![]() |
![]() |
Biohazardous Infectious Materials | ![]() |
![]() |
Health Hazard | ![]() |
![]() |
Environment (May cause damage to the aquatic environment) | ![]() |
![]() |
Exclamation Mark (May have less serious health effects or damage the ozone) | ![]() |
![]() |
There are a lot of similarities between the Canadian and American labels. One key difference is the color coding. As shown in the table above, the labels for the U.S. have different colors. This helps differentiate between the types of hazards that certain materials can have. The “Hazard Diamond” from the National Fire Protection Association (NFPA 704) shown in Figure 2 conveys health warning information for emergency response teams.
![]() |
Figure 2. Hazard Diamond (Uline) |
With the help of labels, it is a lot easier to separate these hazardous substances. It is also important to keep incompatible materials at a distance from each other such as:
- Acid + Bases
- Flammables + Oxidizers
- Water Reactive + Aqueous Solutions
Special Storage of Hazardous Materials in a Warehouse
Having an organized warehouse with labeled products and sectioned-off areas helps facilitate the storage of hazardous substances in a warehouse. In addition, there are key procedures that can help improve warehouse safety when it comes to hazardous materials. They are as follows:
- Have an organized receiving area with information and paperwork for every substance that is received to properly identify what comes in and goes out.
- Every individual material that is received should be accompanied by a Material Safety Data Sheet (MSDS) which provides:
- Product information
- Hazardous ingredients
- Physical data
- Fire and explosion hazard data
- Reactivity data
- Toxicological properties
- Preventive measures
- First-aid measures
- Preparation information
- Check for damages when goods are received (holes, leaks, or any other damages that can increase the risks of spills).
- During the storage of hazardous materials in a warehouse, it is important to keep areas properly ventilated and keep them far away from heat sources and direct sunlight.
- Use chemical-resistant structure materials within the facility.
- Use chemically approved containers, cabinets, and refrigerating units.
- Store the incoming materials based on chemical compatibility and not alphabetically.
- Make sure the ventilation (supply and exhaust systems) follows the ASHRAE Standards 62.1 and 62.2 for hazardous materials.
- Make sure the sprinkler system (whether it is foam or water) complies with the NFPA Chapters 16 and 17 for hazardous materials.
- When storing products in pallet racks, make sure you have updated LARCs (Load Application and Rack Configuration drawings). To learn more about why LARCs are so important, read this article. Regularly inspect the racks for damages, non-conforming issues to the rack design code, or discrepancies with LARCs (the original engineer-approved drawings).
![]() |
Figure 3. Chemical storage cabinets (Barrier Holden, 2014) |
![]() |
Figure 4. Receipt of goods area (Health and Safety Executive, 2009) |
Moving and Stacking Hazardous Materials on Pallets
When handling hazardous materials in a warehouse and storing them on pallet racks, there are several factors to consider. Some of the treated wood pallets are very toxic and are unsafe to store hazardous materials. Always look for the pallet stamp to ensure that you are using the right pallet with a safety pallet treatment. For additional information on the different types of pallets available in the industry, read this article.
![]() |
Figure 5. Sample Pallet Stamp (Lovely Greens, 2013) |
![]() |
Figure 6. Types of treatment codes on pallet stamps (Eric Brennan, 2014) |
Not only do the pallets you use matter when storing hazardous material, but also the way you stack the material. There are two main configurations to properly stack and secure the substances on the pallets:
- Interlinked stacking
- Strapping
Interlinked Stacking
The stacking method can significantly by the stacking method. Intermediate layers, e.g. made of laminated paper or corrugated cardboard, represent a layer bond with the drums. With the interlinked stacking of boxes, the unburdened upper layer often must be held together. If the individual pieces (e.g. boxes) are very light, the layers should also be secured with shrink wrap.
![]() |
Figure 7. Interlinked stacking for boxes and cylinders (Berufsgenossenschaft Rohstoffe und chemische Industrie, 2013) |
Strapping
Packaging on a pallet can be made more stable with vertical and/or horizontal strapping using textile, plastic, or steel lashing straps. With boxes made of corrugated cardboard, conical packaging, or soft packaging, attention must be paid to the tightness of the strap, as this can damage the packaging. To help avoid this, edge protectors are used to spread the clamping force of the straps.
![]() |
Figure 8. Strapping for Boxes and Cylinders (Berufgenossenschaft Rohstoffe und chmische Industrie, 2013) |
![]() |
Figure 9. Examples of strapping and interlinked stacking (Health and Safety Executive, 2009) |
Hazardous Material Spill Prevention and Response
According to the Workplace Hazardous Materials Information System (WHMIS), there is always a chance that a spill or leak can happen when storing and handling hazardous materials in a warehouse. The key is to be prepared with an efficient clean-up plan. Having the necessary tools and equipment can go a long way to avoid spills from affecting the health and lives of workers.
Below are three proactive steps you can take to be better prepared for a potential spill:
- Purchase proper employee attire for safe handling of hazardous materials: Personal protective equipment (PPE) is vital for keeping your employees safe when handling hazardous materials. At the minimum, workers must have eye protection, gloves, and boots. Most warehouse situations rarely require full hazmat suits, but proper coveralls are strongly recommended. Face shields are also recommended when handling corrosive materials.
- Post signs and visual aids: Carry a full assortment of visual aids like preventative floor signs, floor safety tape, tool shadow tape, and aisle markings.
- Install spill pallets: Installing spill pallets (Figure 10) beneath the liquid storage containers to prevent the danger of leaks and spills. The size of the container will determine the size of the pallet. Drums containing 55 gallons or more must have a full coverage spill pallet to to catch spills on all sides. The spill pallet must be designed to hold at least 35% of the drum's content.
![]() |
Figure 10. Spill pallets (ENPAC Spill Pallets) |
Beyond these preventative measures, there are also best practices that should be followed in response to a spill. These include not touching the spilled material, containing it with an absorbent material, assessing how the spill occurred in the first place, and finally, planning how to prevent it from happening again. More comprehensive lists of how to properly respond to a spill can be found on the United States Department of Labor and the Government of Canada websites.
Traffic Routes: The Safe Handling of Hazardous Materials in a Warehouse
Although there is no official guideline for traffic routes when warehousing hazardous material in North America, having ample space to maneuver pallets with lifts can reduce the impact of accidental damages resulting in leaks and spills. Within the Health and Safety Executive (HSE) in the United Kingdom, traffic routes in warehouses for hazardous substances must have a specific width. In the case of traffic routes for workers, these must be at least 2.5ft (0.75m) wide, and for forklift traffic, the routes must have the width of the forklift plus at least 1.64ft (0.5m) on each side of the fork-lift truck.
![]() |
Figure 11. Traffic routes for lifts and workers (Berufgenossenschaft Rohstoffe und chmische Industrie, 2013) |
Takeaway on Hazardous Materials Safety
Looking at each point presented, they all play a key role in protecting not only the materials being stored but also the employees from potential physical and health hazards. It is important to take these into consideration when operating a warehouse that stores hazardous material and take the necessary precautions such as:
- Correctly reading the MSDS documentation when goods arrive
- Organizing the material and properly storing it
- Frequently inspecting the hazardous material for damages or any observable issues
- Supply warehouse workers with proper PPE and training to handle the material in case of a spill
For more information regarding these topics, you can refer to the most recent versions of the Codes and Standards below:
- NFPA Chapters 16 and 17
- ASHRAE Standard 62.1 and 62.2
- WHIMS 2015 and 1988
- OSHA CFR 1910, 1915, 1917, 1918, and 1926
It is equally important to integrate good rack safety procedures that will help protect hazardous materials from being damaged. Respecting North American rack design codes and conducting regular rack inspections considerably reduces the risk of rack collapse. Find a reliable and experienced rack safety partner who can guide you in finding the most suitable and efficient rack safety solutions to not only safely store your hazardous materials, but also to help you improve the overall safety of your warehouse.
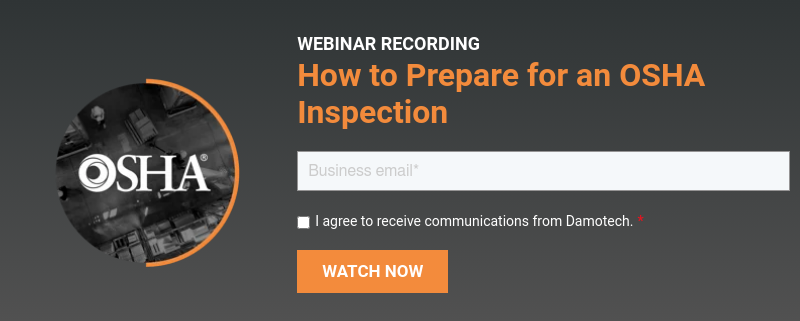
References:
Berufgenossenschaft Rohstoffe und chmische Industrie. (2013, November ). Storage of Hazardous Substances. Retrieved from ASECOS: https://www.asecos.com/dokumente/M062_Code-of-Practice_Storage-of-Hazardous-Substances.pdf
Dull, J. (2019, June 18). OSHA Floor Markings. Retrieved from ifloortape.com: https://ifloortape.com/osha-floor-marking-safety-5s-nsc/
ENPAC Spill Pallets. (n.d.). Retrieved from enpac.com: https://enpac.com/?fbclid=IwAR3FsescfJab6yyoCWhDu6cuCaghyMkbUDGJlbeA9VCfDe6FBHprtjtsnjc
Health and Safety Executive. (2009). Chemical Warehousing: The storage of packaged dangerous substances. Retrieved from Safety Resources Blog: https://safetyresourcesblog.files.wordpress.com/2014/10/chemical-warehousing.pdf