Used racks are often an attractive choice for warehouse owners: compared to new racking, their costs can be much lower, which plays a vital role in the decision-making process. However, purchasing second-hand racking does not come without risks. You should be aware of a few concerns to avoid mistakes that could jeopardize safety in your warehouse.
Proper research and asking the right questions before purchasing can reduce investment risk. The five tips below will help you make the right decision for your facility when buying used racks.
5 Safety tips when buying used racks
Buying used rack tip #1: Watch for look-alike parts that aren’t truly identical
On industrial racking, upright columns have holes at regular, repeated increments, and beams have connectors that fit with those holes. Not all racking brands have the same hole patterns, and there are many variations in shape: sometimes, holes are round, square, rectangular, teardrop-shaped, etc.
Additionally, the spacing between the holes and the thickness of the metal can vary. This means that beam connectors of a given type may not precisely fit into existing uprights. Even if the beam manages to fit, there are additional concerns, and load capacities may change.
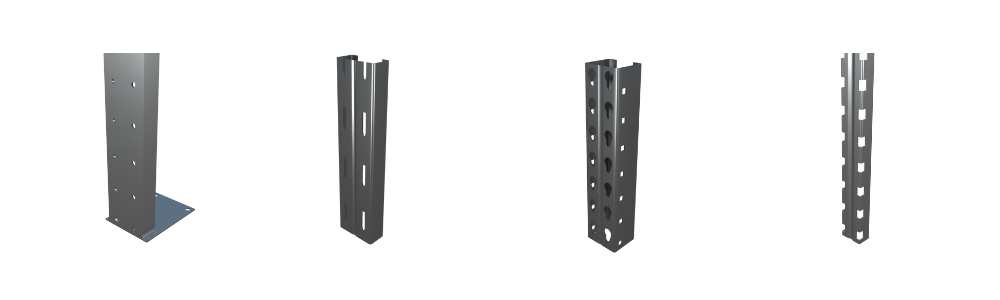
Depending on the beam used, the holes for safety pins, screws, or built-in safety devices might not necessarily align with those of a different upright from the same manufacturer, or a different one. This would make those beams easily susceptible to being detached from the racks. If the fit is not right, the rack could become out-of-plumb, unstable to the point of collapse, or simply inadequate for horizontal loads produced during a seismic event.
Damaged rack parts must always be replaced 'like-for-like', otherwise, load capacity may change, and LARCs will not apply.
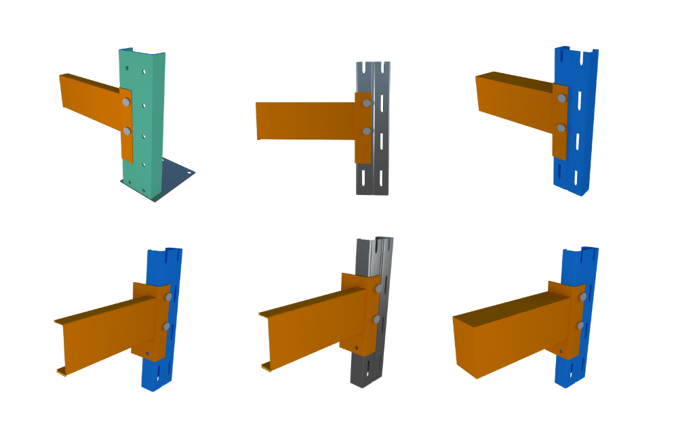
Buying used rack tip #2: Consider the hidden limitations and manufacturer support
Have you checked if the original rack manufacturer of the used racks you plan on purchasing is still in business? Where will you go if specific replacement parts are needed and not available on the used market? Who will confirm that the replacement rack components are compatible? And how can you order parts if the original rack manufacturer (OEM) is unknown?
As you can see, the processes for ordering OEM parts may become difficult, and the warehouse’s storage may not be compliant. Racking manufacturers also occasionally recall products, and purchasers must verify the status of the rack type they intend to purchase before doing so.
2.1 Ongoing rack maintenance becomes more complex
If a warehouse’s racking system becomes damaged, replacement parts may need to be ordered. This task can be complicated if there are many racking types from different manufacturers on the same racking system. Given that used beams and uprights are not always labeled with the manufacturer’s information, warehouse staff may need additional research to identify types before ordering suitable replacements.
Some product lines may have been discontinued over time, or some manufacturers may have left the business. In such cases, ordering the exact replacement parts may be impossible.
2.2 Warehouse space optimization is restricted
The manufacturer customizes racking solutions to optimize for a client's storage needs. Dimensions and load capacities designed for one particular situation may not be ideal in another. So, while the specifications for a rack may look similar to your needs, they may still differ and not meet your specific requirements.
Buying used rack tip #3: Ensure compliance with local building codes
Rack owners/operators are responsible for ensuring that their racking systems comply with building and fire codes. To do so, they should have documentation proving such adherence on hand, should officials request to view it [1]. While the system intended for resale was approved initially, the concern is that building codes change over time, and racks that met them when they were first installed may no longer meet them today. Building codes also change between regions, states, and provinces, so ensuring used racks meet your local code requirements may be challenging.
It is critical to ensure that the racking systems you intend to purchase meet current building code requirements in your area. Employers must provide a safe work environment for their employees, and using racking systems that are certified per local building codes falls under that responsibility.
Buying used rack tip #4: Evaluate the level of damage on the used racks you're buying
One of the most intuitive concerns in purchasing used warehouse equipment is the damage to the racks themselves. Damages on a racking system incur “a reduction in actual capacity and structural performance” [1], meaning that they may no longer meet their advertised load capacities or may even be unfit. Even if the buyer inspects a used rack before purchasing, it is essential to note that disassembly, packaging, and transport may also damage the components before they arrive at their new warehouse.
4.1. Refurbished pallet racking parts
Sellers may be advertising their racks as refurbished. While this may sound appealing at first glance, it may cause concern. According to the Rack Manufacturer’s Institute (RMI), “without proper engineering oversight, there is no proof or assurance that the replacement part is sound and will yield a safe operating system” [2]. Any racking system changes, modifications, repairs, or reconfigurations require a new structural certification by a rack design professional [1,3].
In other words, if replacements are not certified by an engineer, there is no guarantee that the previous load capacity will be maintained, and a liability will be created.
Buying used rack tip #5: Be wary of hidden costs and the absence of a warranty
The asking price for used racking may be less than that of an OEM rack provider, yet transportation, unloading/reloading, and uninstall/install costs must be considered. While these two are pretty evident, other factors may not be.
5.1 Used rack lead time concern
An important consideration is shipping time. Used racking may need to be unloaded, dismantled, and packaged before shipping to the buyer. Because of these steps, it may take longer to arrive at the new warehouse than it would with new racks, which could negatively affect operations in the facility. Old labeling on the racks may need to be removed, which would take time. Inquire about the time frame in both cases (new and used) and factor that into your decision.
5.2 Used rack (re) certification
All industrial racking systems must have technical drawings created by engineers that detail the configuration and load capacity of the system. Relocating or making changes to the configuration requires new documentation and certification from a racking engineer [1,3,4]. Creating such documentation would incur additional costs. Documentation supplied by the manufacturer at the initial purchase may no longer be available at resale (lost or misplaced), or not match your exact configuration. This could complicate the certification process.
5.3 Used rack warranty
Another critical concern is that the manufacturer’s warranty may not be upheld after the teardown and transfer. Additionally, “mixing new and used pallet rack components from different manufacturers can affect the manufacturers’ warranties” [5] even if they are still functional post-resale.
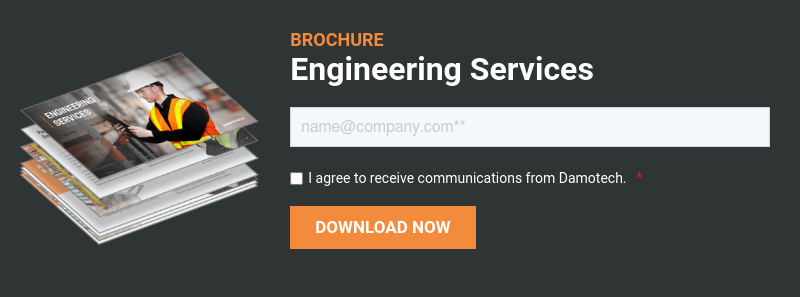
Comparison of new vs. used pallet racks
Category | New Pallet Racking | Used Pallet Racking |
---|---|---|
Condition | Delivered in flawless condition with no prior wear, ensuring consistent performance from day one. | May show signs of wear, rust, or damage, potentially affecting appearance and performance. |
Cost | Higher upfront investment, but often balanced by longer lifespan and fewer immediate repairs. | Lower initial price, making it attractive for tight budgets, though long-term costs may be higher if repairs are frequent. |
Durability | Built to last under regular use, with predictable performance and lifespan. | Durability varies depending on age, prior usage, and storage conditions before purchase. |
Availability | May require longer manufacturing lead time, especially for custom orders. | Often available immediately, allowing for quick setup or project turnaround. |
Warranty | Typically includes manufacturer warranty covering defects and ensuring peace of mind. | Rarely includes warranty; buyer assumes more risk if issues arise after purchase. |
Sustainability | Requires new materials and manufacturing, which has a higher environmental footprint. Probably requires shipping from further away. | Extends the life of existing equipment, reducing waste and manufacturing demand. Most probably sourced locally. |
Compatibility / Built to Specs | Custom-built to match warehouse layout, load capacity, and operational needs. | May not match your exact requirements; similar-looking parts may be incompatible. |
Standard Compliance | Meets the latest MHI and industry safety standards out of the box. | May not comply with current standards, especially if manufactured many years ago. |
Tech | Can integrate with modern warehouse tech such as automation, RFID, and tracking systems. | Unlikely to include modern tech features; upgrades may be difficult or costly. |
Consistency / Aesthetics | All components arrive in matching colors and finishes, giving your warehouse a clean, uniform appearance that reflects professionalism. | Colors, styles, and finishes often vary between used components, creating a mismatched look over time — your warehouse can look like a mix of random parts. |
Expert solutions to make used racks safer for your warehouse
While these concerns are pertinent, used racking may still be the solution envisioned for your warehouse. This section offers some general advice that may be useful in offsetting risk.
- If possible, try to see the racking components before buying them. Photos can be taken selectively, and angles or lighting can affect the appearance of damage. While checking the racking, identify critical (non-aesthetic) damages such as large deformations or pitted/flaking rust. If you do not know how to inspect a rack for damage, online tools like this Rack Damage Assessment Guide can guide you. Occasionally, in-house repairs are made on the racking, which is a cause for concern, especially if they are not certified. New paint may also hide underlying rust.
- Please inquire about the load capacities and dimensions of the systems and ensure they adequately meet your warehouse’s storage needs.
- Note the manufacturer’s name and racking type/style. This will facilitate future repairs, as you know where to order parts. Additionally, it allows you to verify if it is compatible with the racks already in your warehouse.
- Review your area's building codes and ensure the purchased racking meets those specifications.
- Ask for any documentation provided by the manufacturer of the racking.
- Consult the rack manufacturer to verify if any warranty is maintained after the secondary purchase.
- Finally, and most importantly, it is necessary to work with a racking engineer as the relocation of racking systems “should be subjected to the same certification processes as a new installation” [1]. The load plaques and their associated capacities cannot simply be transferred and posted in a new facility without verification [3]. Racking engineers will provide the technical documentation required to certify a racking setup. They can assess damages to see if load capacities can be maintained as advertised, or certify repairs for refurbished products. They can also create compulsory load capacity displays in prominent locations [1,3,4].
Buying used racks: why safety must come first
Cost savings can be appealing when purchasing used pallet racking, but safety should never be compromised. Older systems may have hidden structural damage, missing labels, or incompatible parts with your existing setup. Without proper inspection, you risk installing equipment that doesn’t meet current safety standards, putting employees and inventory at risk. Always verify the manufacturer, check for visible and hidden damage, and ensure the system complies with industry regulations before purchasing. A careful evaluation today can prevent costly accidents and downtime tomorrow.
A smarter alternative: engineered repair kits instead of used racks
Instead of replacing damaged rack columns or braces with used — or even new — racking, you can extend the life of your existing system with engineered repair solutions like the DAMO PRO and DAMO BRACE. The DAMO PRO column repair kit not only restores load capacity but also includes a lifetime warranty, giving you lasting peace of mind. Its robust design helps protect against future impacts, reducing repair frequency over time. The DAMO BRACE replaces damaged or missing horizontal and diagonal braces, ensuring structural integrity without full frame replacement. Both solutions are installed with minimal disruption to warehouse operations, keeping your storage safe, compliant, and cost-effective.
Always be vigilant when buying used racks
Buying used warehouse racks can be a good idea for your warehouse, especially if you know the safety concerns to consider when planning your purchase. The lower costs of used racks must be compared to the risks to warehouse safety and potential operational complications. In that case, the answer to the equation is easy to find, and the choice becomes easier.
References
[1] CSA Group. (2017). User Guide for Steel Storage Racks A344-17. Toronto, Ontario: Canadian Standards Association.
[2] Rack Manufacturer’s Institute. (2014). Guideline for the Assessment and Repair or Replacement of Damaged Rack - Version 1.00. Charlotte, North Carolina: Rack Manufacturer’s Institute.
[3] Rack Manufacturer’s Institute. (2021). Design, Testing, and Utilization of Industrial Steel Storage Racks ANSI MH16.1-2021. Charlotte, NC: Rack Manufacturer’s Institute, an Industry Group of MHI.
[4] ANSI. (2012). Specification for the Design, Testing and Utilization of Industrial Steel Storage Racks MH16.1:2012. Charlotte, North Carolina: Rack Manufacturers Institute (RMI).
[5] CSA. (2005). User Guide for Steel Storage Racks/Standard for the Design and Construction of Steel Storage Racks A344.1/A344.2-05. Mississauga, Ontario: Canadian Standards Association.