Have you ever thought about how earthquakes can affect storage racks in your warehouse? Aside from causing a complete collapse in extreme cases, there are many other less obvious ways that earth tremors can jeopardize the safe operation of your racking systems. Whether you are the owner of an existing facility or building a new distribution center, there are several factors to consider.
No matter what region your warehouse is located in, seismic forces need to be taken into account when designing the warehouse rack systems. Not only must they be designed adequately, but they must also be installed with respect to specific seismic requirements. In this blog, we will cover general topics to consider for seismic forces.
What is Seismic Activity?
Seismicity, or seismic activity, is the frequency, type, and size of earthquakes experienced in a specific region. Higher levels of seismic activity can lead to a higher probability of earthquakes. But an area with a low seismic activity does not necessarily mean that there is zero chance of an earthquake. A seismographic network records earthquakes. Each seismic station in the network measures the movement of the ground at that site. Magnitude is the most common measure of an earthquake’s size. It is a measure of the size of the earthquake source and is the same number no matter where you are. Resources such as www.seismicmaps.org help clarify if you are in a low or high seismic activity region.
![]() |
Figure 1. A Seismic hazard map of North America. |
How Pallet Racks React to Seismic Activity
An earthquake can generate stress and cause damage to your pallet racking systems. Typical damage includes pulled anchors, out-of-plumb upright columns, deformed bracing components, and beam-to-column connectors. To learn more about the aftereffects of an earthquake on racking, read our blog on 5 Signs Your Racks May Have Been Damaged During An Earthquake.
As mentioned earlier, pallet rack systems must be designed and installed to resist seismic forces. The original equipment manufacturer (OEM) will usually have established the minimum requirements that must be followed. Rack loads must always respect the LARCs (Load Application and Rack Configuration drawings) that the design engineer issued. If rack components are replaced, modified, or reconfigured, load capacities can be compromised.
Choosing the Right Racks
There are specific aspects of a rack that should be evaluated to ensure that it conforms to codes. Only professional engineers and the OEM can determine rack load capacity. These rack experts can check and validate the following details:
- Anchors and baseplate
- Height-to-depth ratio
- Upright and beam configuration
- Clearance with building or other racks
Anchors & Baseplate
When a rack system is adequately designed, the size, quantity, and placement of anchors are specified in the LARCs. The same goes for the size, thickness, and position of holes for the baseplates.
![]() |
Figure 2. A standard baseplate (left) vs. a reinforced baseplate typically used to take on seismic forces. |
Height-to-depth Ratio
ANSI (American National Standards Institute) & CSA (Canadian Standards Association) state that pallet racks with a height-to-depth ratio higher than 6:1 need special provisions to prevent overturning. For example, attaching the top of the upright with adjacent racks using cross-aisle ties or row spacers for back-to-back uprights to prevent overturning or using special anchoring methods to prevent the uplift of a column.
![]() |
Figure 3. Height-to-depth ratio of back-back systems attached by row spacers. |
Upright and Beam Configuration
Different combinations of uprights, beam sizes, and beam elevations confer different dynamic behavior to the racks and alter their seismic load capacity. Warehouse racks should, of course, always be rigorously inspected for damages, and it's important to make sure the upright and beam configurations match existing LARCs. The rack loads must always respect the maximum allowable load capacity indicated in the LARCs (Load Application and Rack Configuration drawings). When damage is spotted, the rack owner should either replace or repair the damaged rack components swiftly.
Clearance with Buildings and Other Racks
To minimize the risk of injury to any warehouse workers in proximity to the rack, as well as to reduce the chance of the building and the rack colliding during a significant seismic event, RMI’s ANSI MH16.1: Specification for the Design, Testing, and Utilization of Industrial Steel Storage Racks calls for a certain amount of horizontal clearance (also called seismic separation) between the two. A clearance distance equal to 5% of the overall racking height (topmost beam level) in the down-aisle direction and 2% in the cross-aisle direction is required. When in doubt, it is best to refer to a rack safety engineer.
![]() |
Figure 4. Minimum down-aisle and cross-aisle clearances. |
Handling & Storage of Goods
OSHA (Occupational Safety and Health Administration) states that “all goods, materials, and equipment at work sites must be stacked, stored, and secured in such a way that it does not flow, move, roll or collapse.” It is the worker’s responsibility to ensure that stacking, storing, or securing goods, materials, and equipment are done safely. Racks, shelving, fixtures, etc., should be regularly inspected for damage and other defects that might cause loss of strength or result in injury or damage.
![]() |
Figure 5. Goods are stored within pallet racks so that they cannot easily roll or slide off the pallets. |
Building Codes
Building codes are rules and regulations that determine the construction, design, and maintenance of your buildings. Your warehouse must comply with the building codes of your region. In the United States, most states and local jurisdictions adopt the building codes from the IBC (International Building Code). In Canada, the building codes are outlined by the NBC (National Building Code). It is vital to comply with the appropriate building codes to ensure your warehouse is built and designed to sustain seismic loads.
![]() ![]() |
Figure 6. IBC (International Building Code) and NBC (National Building Code) |
Soil Classification
The type of soil a warehouse is built on needs to be considered. The NEHRP (National Earthquake Hazards Reductions Program) defines six different site classifications, based on the soil, rock, and various other characteristics:
B: Rock
C: Very dense soil and soft rock
D: Still soil
E: Soft soil
F: Soils requiring more evaluations
![]() |
Figure 7. Types of soil. |
Each letter will classify the characteristics of your soil and how it impacts your warehouse during a seismic event. Soil type is a significant factor in determining how severe an earthquake will be. The softer the soil, the more severe the earthquake will be since seismic waves tend to amplify much more in soft soils. This would result in greater vibrations being transferred through the foundation of the warehouse.
Practicing “Earthquake Emergency Procedures”
![]() |
Figure 8. "Drop, Cover, and Hold on" earthquake preparedness protocol recommended by OSHA. |
OSHA recommends practicing earthquake emergency procedures at least two times per year to promote and strengthen safety behavior. Earthquakes are unpredictable; hence, you will be prepared for whenever one occurs. You can start by determining safe places in your warehouse; the shorter the distance to move to safety, the quicker you can get there. Note that being under a rack system is not considered a “safe place.” When you reach your safe place, DROP, COVER, and HOLD ON. Practice these actions regularly so that they become automated responses. For more details, visit OSHA’s preparedness and response to earthquakes website.
Key Takeaways
As you can see, there are many key factors to be considered when dealing with seismic activity. Some of the factors are assessed during the design and construction process of the warehouse and racks, while others need to be evaluated periodically. It is the responsibility of the owner of the warehouse to ensure everyone’s safety. For rack owners, this means that improper use, selection, installation, or maintenance of racking may put workers at risk of injury and expose employers to serious liability in case of an accident. Therefore, it is crucial to be on top of your racking systems’ health, especially if you are in a region with higher seismic activity. If you have any specific concerns about your pallet racks or would like to get a racking inspection done in your facility, consider using Damotech’s engineering services.
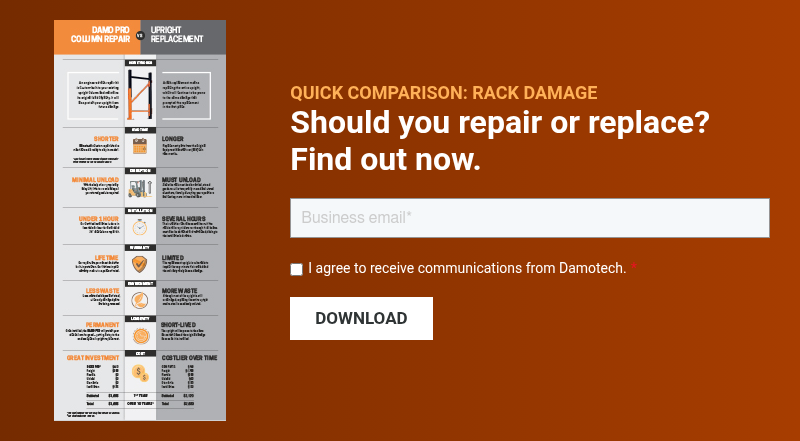