Although field welding or welding on existing racks may seem like a quick and inexpensive way of repairing a damaged racking system, there are risk factors to consider before going forward with this option.
- Why can’t we simply weld a stiffener channel to the damaged rack column?
- Racks already have welds when I buy them, why can’t we do the same?
- Do you have anything in writing from OSHA about onsite welding on existing racks?
These are all legitimate questions for someone looking to fix their racks but getting a clear answer on what is acceptable and what is not, isn’t easy. OSHA is not specific about rack damage or repairs; they ask that rack damage be addressed so that no one gets hurt and remain unclear about how this should be done.
The Rack Design Code (ANSI MH16.1), states that “welds on the test specimen shall satisfy and be performed in strict conformance with the requirements of Welding Procedure Specifications (WPS) as required by the American Welding Society (AWS)”. But this is aimed towards rack manufacturers, not the rack’s owner or maintenance manager.
The Rack Repair Guidelines issued by RMI are more explicit about welding. They outline that field repairs (in the warehouse) are risky and must be overseen by a qualified Professional Engineer so that the work is performed in accordance with applicable American Welding Society (AWS) codes.
They also talk at length about field welding risks such as fire hazard, weld contamination, operation temperature, engineer supervision and welder certification. I’ll summarize these for you:
Fire hazard: even when carefully following recommended fire safety procedures, welding causes sparks that may fall in the worst possible places, on products, flammable product or pallets, and become a fire hazard. Consult OSHA standard 29 CFR 1910.252(a) for more details.
Weld contamination: this happens when the welded surfaces are not well prepared, which can result in a weakened weld or hydrogen embrittlement, possibly leading to failure.
An excerpt from AWS: “…The portions of such surfaces which will be welded shall be thoroughly cleaned of all foreign matter including paint for at least 2 in [50 mm] from the root of the weld.” (1)
Operation temperature: great care must be taken to control the temperature during the welding process to respect AWS standards. Welding in a freezer environment is therefore generally discouraged.
Supervision and certification: for field welding, an engineer must provide a qualified procedure and the welder must be certified by AWS.
“If field welding is necessary, the Supervising Engineer must provide a qualified or prequalified procedure for the weld joint that meets appropriate AWS standards.” (2)
Welder Certification: A welder must show proof of certification and have the required skills to execute the repair exactly as specified by the engineer supervising the work.
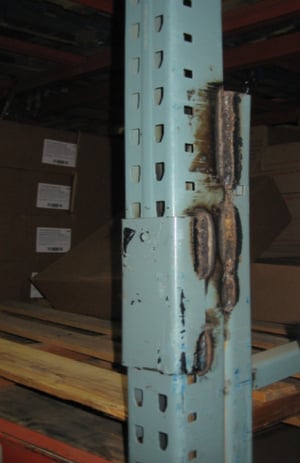
The image on the right is an example of a repair that is to be avoided. Since it's difficult to test the result of the weld and guarantee a resistance at least equal to that offered by the original component, there are strong recommendations against field welding in a warehouse on existing pallet racking. If you absolutely must use this method, first consult an engineer familiar with racking systems and make sure that all aspects of the code and regulations are followed carefully before proceeding with the welded repair.
To avoid the use of field welding, there are certified bolt-on repair solutions that do not require on-site welding or the dismantling of the racking system. To find out more about these rack repair solutions and see how it is done, watch this video.
(1) American Welding Society Specification- D1.1/D1.1M [3]; Section 8.5.1 Base-Metal Condition
(2) RMI Guideline for the Assessment and Repair or Replacement of Damaged Rack V.1 Section 5.4