The concept of addressing rack damage seems simple: You spot a dented column or brace and you decide whether you would like to replace or repair it. Well, not quite! There are many different degrees of rack damage and knowing when it is severe enough to address can be hard to determine. In this blog article, we will break down the most common types of damages per racking component and give you rules of thumb that can be used to educate warehouse workers on pallet rack safety. We will also offer a visual tool that can serve as a daily reminder that pallet racks should be examined on a regular basis.
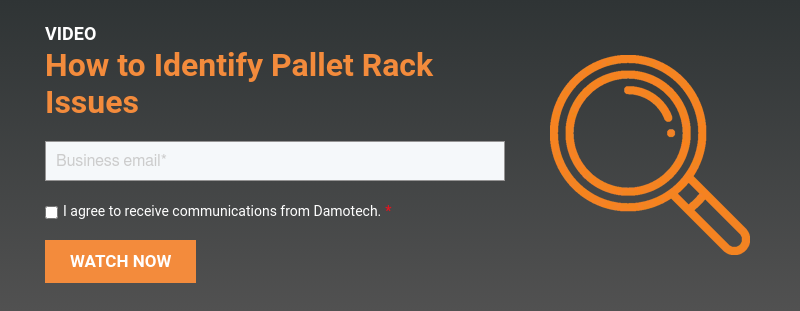
First Things First
Most experts and governing bodies agree to recommend monthly pallet rack inspections done by trained warehouse personnel, and yearly inspections performed by third party rack experts or engineers. Read our blog on When to Inspect Pallet Racks? for more information on specific situations when a rack inspection is strongly suggested. The frequency of inspections also depends on how often rack-related issues occur in your warehouse. To help you conduct your own rack inspections, you can download our Pallet Racking Inspection Checklist. Using this checklist, you can easily record the location of damage, define a priority level, and consolidate a list of repairs needed.
1-2-3 Rule: Racking Uprights & Braces
To determine whether a deflection on an upright or brace should be addressed, follow this simple 1-2-3 rule. It is based on the degrees of deflection that need addressing:
- 1/8” of an inch for a frontal column deformation
- 2/8” for a lateral column deflection
- 3/8” deformation on a brace
Frontal Upright Deflection
Start with what is easiest to see: a frontal damage to your upright. Examine them carefully and check if there is a deflection of over 1/8” within a span of 40 inches. Take it a step further and look for other types of damage like cracks, bulges, pinched columns, and any sign of corrosion. Any of these are worth being investigated by a 3rd party rack safety expert via a more thorough rack inspection. Engineers specializing in rack safety will look beyond the damage to certify that the rack systems comply with governing rack design and safety standards.
Lateral Upright Deflection
When looking at lateral damage to your upright, any deflection over 2/8” within a span of 40 inches should be addressed. Pay particular attention to damage that is sometimes hidden behind the beam connectors.
Horizontal or Diagonal Brace Deflection
A rack frame bracing consists of horizontal and/or diagonal members that join the front column to the rear column. These members are very carefully designed by the rack manufacturer to stabilize the rack frame in the cross-aisle direction and to support each of the individual columns. Any damage to these components can jeopardize the stability of the racking frames and could degrade the structural integrity of the entire racking system. Therefore, if you spot a deflection of over 3/8” within a span of 40 inches, this should be addressed as soon as possible.
Damage Assessment of Individual Rack Components
Twisted Columns
Twisted columns may affect the load capacity of the rack. Load capacity refers to the maximum load that may be placed on a given racking system. Once this is compromised, your racking may be at risk for a collapse. For this reason, considerably twisted columns should be addressed immediately.
Anchoring
ANSI/RMI standards require pallet rack anchors for all column bases in every storage rack system. Why are such small components essential to the whole structure? Because these mechanical fasteners are what connects a rack system to a building. Their purpose is to resist forces such as: overturning forces caused by earthquakes or wind, accidental impact forces on the bottom end of columns (i.e., from a forklift), and shear forces (horizontal reactions). When assessing anchoring, you should also check if shims are well seated, secured and of equal size to the footplate. Shims should also be made of material that meets or exceeds the bearing capacity of the concrete floor; wood or plastic shims won’t cut it!
Homemade Repairs
With homemade repairs, it is very difficult to test the result of the weld and guarantee a resistance that is at least equal to that offered by the original component. Because of this, there are strong recommendations against field welding in a warehouse on existing pallet racking. Instead of homemade or welded repairs, you should consider an engineered rack repair solution that is bolted on and does not require on-site welding.
Beams
While rack beams can support heavy loads, their capacity is not unlimited. Any loaded beam showing a visible deflection should be checked against the simple L/180 limit. The vertical deflection of the beam should not exceed the length of the beam (L) divided by 180. As shown in the image below, the deflection is measured as the largest distance from the deformed loaded beam to the initial unloaded beam position (horizontal). Look for damaged, deflected, unclipped, or overloaded beams, missing safety bars, and badly positioned or damaged pallets. Lastly, you should also check that the beam has an up-to-date load capacity label that has been certified by an engineer.
Beam Connectors
Beam connectors are what connects the beams to the uprights. They commonly have teeth that clip into the holes of the upright. Safety pins are devices that prevent the accidental dislodging of the beam connector during loading or unloading of pallets. There must be at least one safety pin in each beam connector. Some beam connectors are bolted onto the upright instead of clipped on. In this case, the bolts act as safety pins so no additional safety pin is required. Look for corrosion, deformations, cracks in the welds, broken connectors, or missing safety pins to see if your beam connectors need to be addressed.
Out of Plumb
Plumbness refers to the verticality of an upright. An out-of-plumb upright is straight but leaning in one direction or another, either down aisle or cross-aisle. ANSI/RMI specification states the maximum out-of-plumb ratio of an upright is ½ inch per 10 feet of height, or simply 1/240, for a loaded upright. Always look in the cross-aisle and down-aisle directions to verify if an upright is out-of-plumb.
Load Capacity
Knowing and displaying your pallet rack’s load capacity, as well as having Load Application and Rack Configuration (LARC) drawings on hand, are critical to the safe operation of your warehouse. The maximum load capacity should be visible either via labels in each bay or by placing plaques on racking systems with uniform configurations. If your racks are missing these labels or plaques, or if the load capacities are unknown, they would need to be calculated by an engineer, who would then provide load capacity labels or plaques for your racking systems.
Rack Safety via Regular Inspections & Employee Education
Regular inspections are a great first step to prevent further damage and reduce the risk of rack failure. All identified damage should be reported, and severely damaged uprights should be unloaded immediately. It is also recommended to contact a rack safety expert who has rack engineers or experts on staff that can visit your location for an on-site rack inspection. These professionals should also be able to share advice on the best solutions to improve the overall safety of your warehouse.
Finally, since racks are living entities, they require routine inspections as part of an established maintenance program. Part of this safety initiative is to share reoccurring safety and damage issues with warehouse employees so that they may also become reliable for identifying and communicating issues to higher management. And since people are visual creatures, we suggest ordering our free Rack Safety Assessment Poster to display in your warehouse, for all employees to see. Rack safety is truly a team effort and the benefits of creating a culture of warehouse safety cannot be understated.
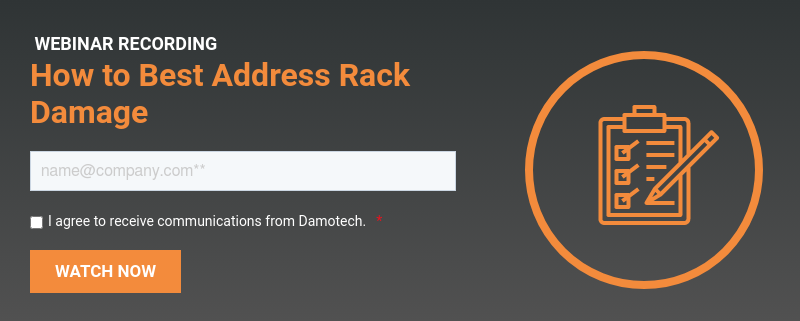