During conformity inspections of pallet rack systems conducted by experienced professionals, the 9 issues addressed in this blog are typically the most frequently encountered.
These issues may not only impact the structural integrity of the rack systems but can also pose operational challenges for workers. Identifying and addressing these issues is critical to ensuring the structural reliability and operational efficiency of your pallet rack storage systems.
Deformed and detached braces
The importance of upright racking braces cannot be overstated. These sometimes overlooked components play a critical role in maintaining the stability of the uprights. Unfortunately, they are also commonly subject to deformation and damage, leading to potential safety hazards.
From accidental forklift collisions to overloading, these braces bear the brunt of warehouse wear and tear. It’s crucial to note that damages to braces on the lower levels may be more critical than higher-level braces, as the lower-level braces are typically subject to higher stresses due to the combined weight of the loads above.
Figure 1. Deformed horizontal brace
The “1-2-3 Rule” is an effective method the RMI recommends to determine if a deformed brace needs to be repaired or replaced. You can read about how to use this method in our Rack Damage Assessment Guide.
If you ever find a detached horizontal or diagonal brace on an upright, it is recommended to have that brace repaired or have the upright replaced as soon as possible.
Missing and loose anchors
Anchors are a critical component to the stability of the racking structure, securing it to the floor, resisting lateral forces, and twisting at the baseplates. Over time, anchors can become loose and dislodged due to various factors, including vibrations from heavy machinery, seismic activity, forklift collision, or even improper installation.
When anchors are missing or loose, the rack’s stability may be compromised, creating an accident waiting to happen. While conducting regular inspections, look at the bottom of the front and back columns to ensure anchors are installed and adequately tightened to the baseplates.
It should be noted that a minimum of one anchor should be installed appropriately at each baseplate for pallet racking over 96" in height. However, the rack manufacturer should specify the exact type and number needed (American National Standards Association [ANSI], 2021, section 1.4.7).
Figure 2. Baseplate missing anchoring
Deformed and detached beams
Another issue that plagues racking systems is deformed and/or detached beams. These components are essential for bearing the direct weight of the pallets and providing lateral stability to the upright columns. However, factors such as overloading, improper handling, or impacts from forklifts can lead to beams becoming deformed and even detached from the rack system.
A deformed beam will have a reduced load capacity and can also create an uneven surface, increasing the risk of goods falling. Detached beams pose a dangerous threat as they are no longer bracing the uprights and are much more likely to fail, causing products/materials to fall into the aisle below.
Figure 3. Severely damaged beam
During your inspections, ensure to check for beam deflection and damage. The maximum allowable vertical beam deflection is the span of the beam divided by 180 (ANSI, 2021, section 5.3).
Missing, loose & inadequate safety pins
Missing, loose, and/or inadequate safety pins are critical and highly common issues found while conducting rack inspections.
Safety pins are like the unsung heroes of pallet racking; they are a small device that secures beams to the upright columns, preventing accidental dislodging due to vibrations or impacts. Unfortunately, these small but crucial components often go unnoticed.
It is common to find safety pins hanging loosely off of the columns or even missing entirely. A missing, loose, or inadequate safety pin can have significant consequences, as the beams may become detached from their slots, potentially causing pallets to fall and endangering warehouse personnel and inventory.
At least one safety pin should be installed on each beam clip to adequately secure the beam to the column and prevent dislodging (ANSI, 2021, section 5.4.2). We recommend using a nut and bolt when possible as they are much more secure devices and less likely to become loose compared to a J-pin or stamped safety pin.
Figure 4. Safety pin preventing beam from fully dislodging
Deformed columns
Deformed and/or twisted columns are a persistent concern that can heavily affect the load capacity of a rack system. Upright columns bear the immense weight of the racking system and the goods stored upon them, transferring this load down to the floor.
Over time, it is common for the columns to get impacted by lift trucks in the facility, leading to column deformations and/or twisting. When a column becomes damaged, it jeopardizes the stability at that location. It can create a domino effect, potentially affecting adjacent uprights, which may have to take on additional weight.
When a deformed column is spotted, using the “1-2-3 Rule” is suggested to estimate how critical the column damage is. The rule is described in our Rack Damage Assessment Guide.
Figure 5. Severely deformed upright column
In-house repairs/welds
Another common issue on pallet racking systems is in-house repairs and welds that have not been designed by an engineer or performed/installed by a professional. To save costs or minimize downtime, some facility managers resort to makeshift fixes or welds performed by unqualified personnel.
Figure 6. Inadequate welded repairs to braces
Unless they have been adequately designed by a professional, these repairs may lower the overall load capacity of the affected component. It’s essential to recognize that only qualified professionals should perform repairs and modifications to the racking systems. In-house welds will likely compromise the load capacity of the welded components as they can alter the properties of the steel if not performed correctly.
Any repairs to the racking should have proper documentation stating they have brought the damaged component back to its original load capacity or identify the new load capacity at the repaired location.
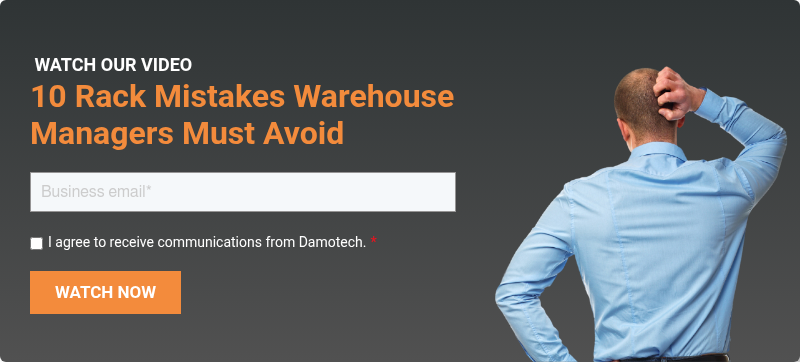
Out-of-plumb & out-of-straight uprights
Upright columns must be installed vertically and adequately aligned to maintain the stability of the rack system. When an upright is leaning in either the cross- or down-aisle direction, it is considered out-of-plumb.
The allowable tolerance for an out-of-plumb upright is half an inch for every 10 feet of height (ANSI, 2021, section 1.4.11.1); anything beyond this no longer conforms to standards. Factors such as uneven flooring, impacts, adjusting beam levels, or even seismic activity can cause uprights to deviate from a straight, vertical position.
When an upright becomes out-of-plumb or out-of-straight, it can lead to uneven weight distribution, making the racking system susceptible to failure. Using a laser level or torpedo level is recommended to check if uprights are out-of-plumb beyond the allowable tolerance. If so, they must be replumbed, typically by adding shims beneath the baseplates.
Figure 7. Using torpedo level to check verticality
Rust formation
Rust forming on the racking components is an issue that often goes unnoticed until it becomes a significant concern. Over time, environmental factors such as moisture, temperature fluctuations, and exposure to corrosive substances, including rain and snow, can lead to the formation of rust on the racks.
This issue can affect uprights, beams, and connectors, all of which play pivotal roles in maintaining the system’s structural integrity. Rust may weaken these components by reducing the steel thickness and, therefore, their load capacity.
If you notice a rusted component and you can scrape away at the rust easily and/or large flakes of rust come off, that component should be repaired or replaced as soon as possible. For more information on this topic, see our blog on rust-related issues.
Figure 8. Extreme rust corrosion to column
Inadequate building clearance
Improper clearance between racking systems and building components is a frequently encountered issue in warehouses and manufacturing facilities. Inadequate clearance can lead to a range of problems, including restricted access for forklifts/personnel as well as potential damage to the building structure and/or rack structure.
Figure 9. Upright inadequate clearance with building wall
Adequate clearance between racking and the building structure or other building components, such as piping, is critical to maintaining safety and operational efficiency within the warehouse.
Inadequate clearances may cause the racks to vibrate, impacting the building structure during loading/unloading or a seismic event. See ANSI MH16.1-21 section 2.6.6 for the allowable clearances between racks and the building structure.
Concluding Insights: Pallet Rack Inspections
As seen from the examples above, pallet racks are complex structures with many working components. This makes the inspection process very tedious as there are many different things to look out for when noting issues.
The 9 issues stated above are some of the most frequently discovered when inspecting racking. Each has its own various problems that are imposed on the rack systems and the facility’s operations.
Although these are the most common, various other issues can still be found on the rack systems. It is highly recommended that an in-house rack inspection be performed monthly by someone knowledgeable of rack damage assessment at your facility.
Additionally, it is recommended to have an annual inspection performed by a professional third-party company that can provide a detailed report on their findings and make recommendations on rectifying the issues. Get more information on the professional pallet rack inspection services Damotech offers.
Reference:
American National Standards Association. (2021). Specification for the Design, Testing and Utilization of Industrial Steel Storage Racks (ANSI MH16.1).