Most warehouses use pallet racks to store their goods and optimize the stacking of materials for safe and easy access. Yet, not all warehouse owners take the proper precautions to ensure safety. Compared to stacking your pallets one on top of the other, pallet racking is a great approach to improve your warehouse's organization and storage capacity using vertical space.
However, to ensure the safety of your employees and merchandise, you need to keep your racks in good condition and do regular inspections. Without proper due diligence, you might make a costly mistake and compromise warehouse safety. This blog post covers the 10 common mistakes to avoid unwanted consequences.
1. DO NOT neglect regular rack inspections
Rack inspection is an important part of your warehouse maintenance. Safety standards suggest that rack inspections should be done at least monthly by knowledgeable warehouse workers and yearly by a third-party expert company. Professionals with specific knowledge and training in structural engineering concepts and rack inspection procedures must conduct this yearly inspection. Racks are exposed to many factors that may cause damage, such as weather, loading and unloading cycles, forklift activity, etc.
While some damages are easy to spot -like bent braces or a twisted column, other issues may need to be assessed by a racking specialist. Some issues may seem harmless, but over time, they could worsen and lead to undesirable outcomes. The consequences of rack failure can be significant, from damage to equipment and inventory to loss of human lives. An inspector watches for damages, clearances, and potential fire hazards and ensures the load capacity labels or plaques are correctly displayed on your racks. This last one makes it much clearer for the different operators in the warehouse to avoid overloading.
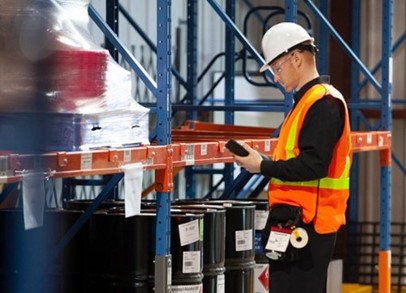
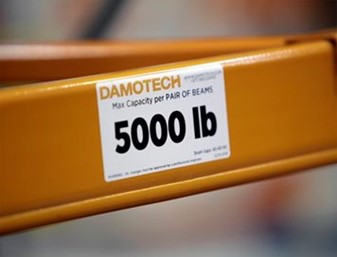
Having a professional racking inspector will help you spot rack-related issues in your warehouse.
2. DO NOT let rack damage accumulate
Repeated impacts can potentially result in catastrophic consequences to a racking system. Once a rack component has been damaged, it may no longer carry its previously rated load capacity. While there are many types of rack damage, the frame doesn't need to be severely impacted to become a safety risk. Damages should be repaired in a timely manner, according to their severity.
If an immediate repair is not an option and the damage represents a safety risk, the racking should be unloaded and marked with the appropriate signage to avoid further use until repairs are completed. A way to prevent these damages is to train employees properly and use protective devices in critical warehouse areas.
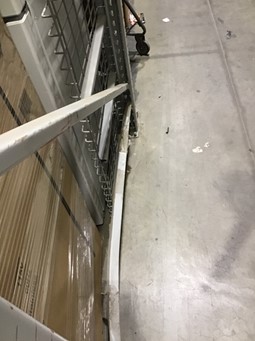
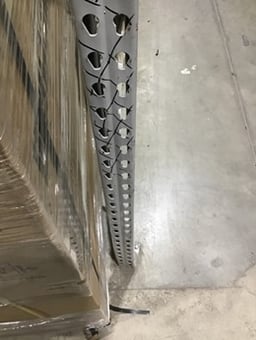
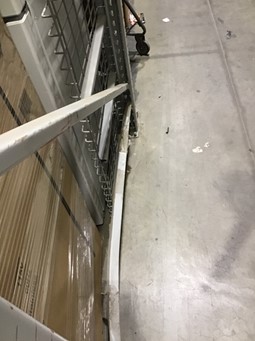
Multiple damages to upright
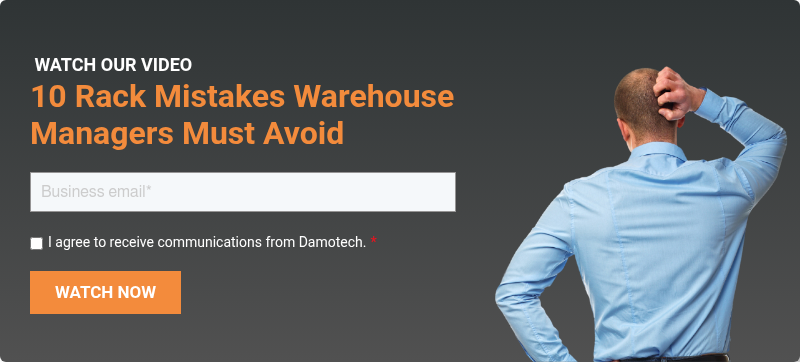
3. DO NOT use “home-made” rack repairs
“Home-made” repairs of racking systems are not recommended unless performed by a certified welder and supervised by an engineer approving the process. Many requirements and risk factors must be considered and respected when performing these repairs, which makes them very difficult to approve.
Many requirements and risk factors must be considered and respected when performing these repairs that make them very difficult to approve. For example, field weld repairs must be in accordance with the applicable codes such as ANSI MH 16.1, CSA S16 and A344, AWS D1.1, or CWB. This includes:
- Validating adequate base metal thickness
- Considering the previous loading history of the racks
- Performing stress analysis on the structure
- Taking into account fire hazards in the welding process
- Respecting the welding procedures (done by a certified welder)
- Controlling the operating temperature during welding
- Having the repair overseen by a qualified professional engineer
- Inspecting the quality of the weld
- Inspecting the repairs after the procedure is done
Hence, without the appropriate certification, “home-made” repaired storage systems represent a safety concern. The safety of the racking can be adversely affected by the welding. The situation is even worse if there is surface contamination or if it was performed in an environment outside of the acceptable temperature range. For more information, read our blog post about field welding on racks and learn why homemade repairs may be risky and unsafe.
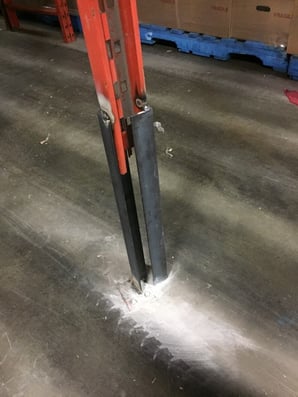
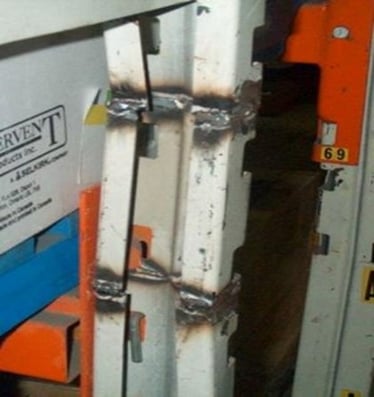
Illustrations of field weld inadequate home-made repairs
4. DO NOT use incompatible rack components
There are many different types of racking components made by different manufacturers. If a rack column or beam is damaged, we might mistakenly believe it can be replaced with any other upright or beam that appears similar in structure. Installing incompatible members to a rack component is not recommended since the members are not guaranteed to adequately replace the original ones.
For instance, a beam and upright column made by different manufacturers may not fit together properly. As a result, the beam may not perform adequately when subjected to all types of loads or easily get detached during forklift operation. Manufacturers use diverse materials and production techniques for columns, bracing, beams, and connectors in their products. It is important to confirm that racking components are compatible to ensure that the rack can be used in a way that does not compromise warehouse safety.
5. DO NOT leave racking systems unanchored to the floor
Anchors are essential for the stability of a rack structure. They provide resistance against uplift and horizontal displacements at the base of columns. Based on the ANSI/RMI MH16.1, every rack must be anchored with at least one anchor per column or more, depending on the manufacturer’s design. A forklift can inadvertently lift an unanchored pallet rack while handling merchandise or accidentally impact the system.
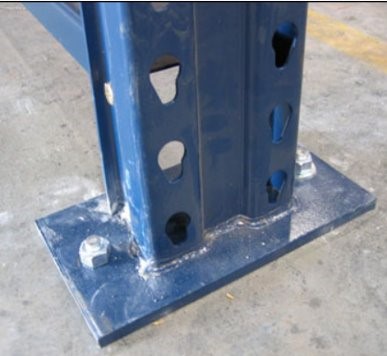
Every rack should have at least one anchor per column
6. DO NOT reconfigure racking without approval from an engineer
Changing the configuration of a racking system can change its load capacity. For example, the load capacities engineers provide are calculated only for the originally planned storage configurations, which are detailed in the Load Application and Rack Configuration Drawings (LARC). The ANSI MH16.1 1.4.2 specification states that the rack owner is also responsible for displaying the load capacity on the rack, as specified in the LARCs. If any modification to the rack configuration is done without an engineer’s approval, you might overload your racks without knowing it.
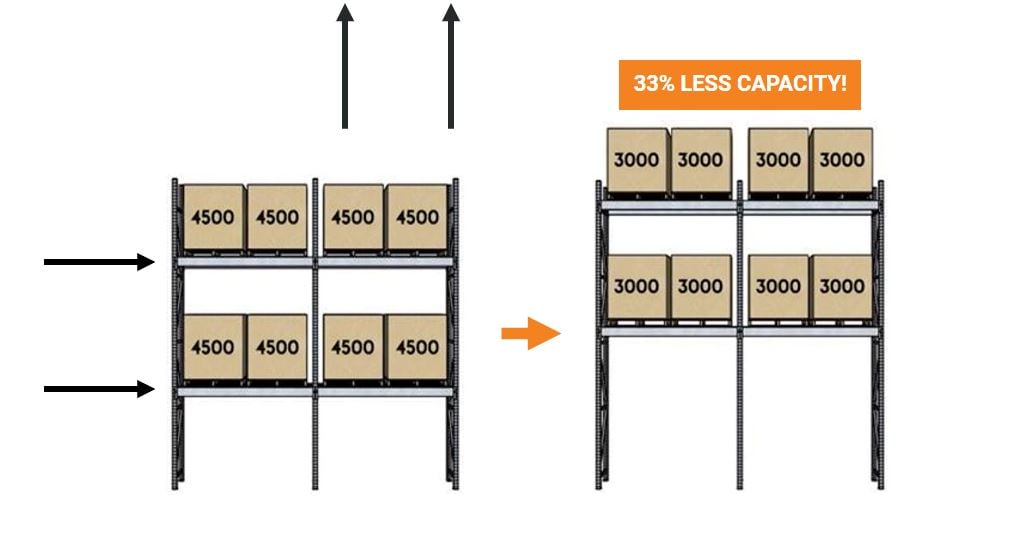
With similar parts, 2 rack configurations will have different load capacities
7. DO NOT operate with inadequate aisle widths
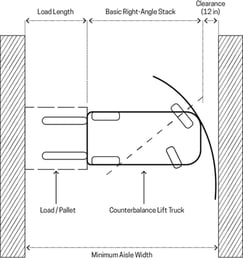
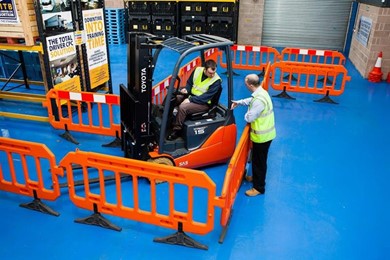
How to determine the minimum aisle width needed for a forklift and instructions to the operator
Before positioning the pallet racks in your warehouse, it is important to consider the compatibility of your forklift and the aisle dimensions. The aisle widths are typically determined based on the type of equipment used. When lift trucks have limited space to maneuver, there is a higher risk of impacting the racking systems and causing damage. OSHA states the recommended width of aisles to be at least 3 feet wider than the largest equipment or a minimum of 4 feet.
Too little clearance will damage both the loads and the storage racks. To minimize the damage, operators will slow down their movement, which could greatly add to the operating costs of the warehouse. Too much clearance will waste space and increase construction costs. In some cases, the cost of the rack system. Where mechanical handling equipment is used, sufficient clearances must be allowed for aisles, loading docks, through doorways, and turns and/or passages. Aisles and passageways must be clear, appropriately, and visibly marked and have signs to warn of clearance limits. Learn more about the five frequent ways forklifts can damage racks.
8. DO NOT connect racks to the building structure (unless specified by an engineer)
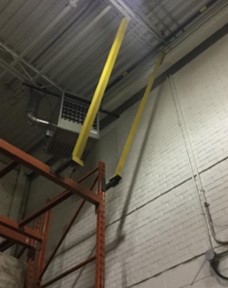
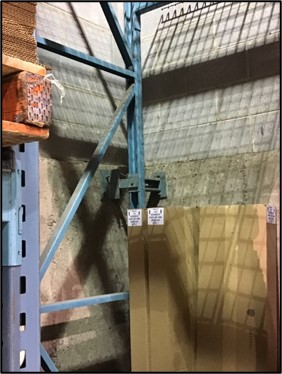
Example of a pallet rack connected to the building structure
Pallet racks are typically self-sufficient and freestanding structures. Building components (e.g., walls, columns, beams, etc.) are not typically designed to support additional loads from neighboring structures. Connecting pallet racks to building components allows forces to transfer between them, resulting in damages to the rack or the building's structure, which could have unintended consequences.
Connecting pallet racks to building components is not recommended unless a structural engineer certifies or specifically designs the structures to interact or sustain the forces from attaching pallet racks. Although pallet rack systems can be connected together with row spacers or cross-aisle ties, an engineer must design and approve such modifications. For more information, see the blog Recommended clearances between pallet racks and building structure.
9. DO NOT use racks in a way it was not designed for
While you might be tempted to use your rack systems to store all kinds of material, most racks are specifically designed to support pallet loads, evenly distributed across a pair of beams. For example, using upright braces to support the merchandise may damage them. It is also important to note that the rack's load capacity is calculated with a specific beam configuration. Attaching additional objects to your systems (e.g., tools, rack replacement parts, merchandise) will put an additional load that was not necessarily considered in the initial calculation, which can increase the risk of failure.

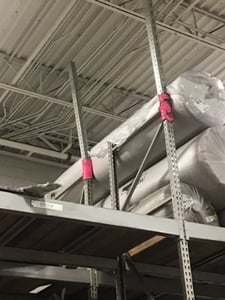
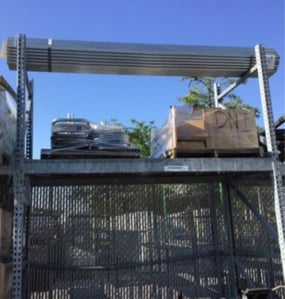
Inadequate usage of pallet racking systems
10. DO NOT operate your racks without proper protection
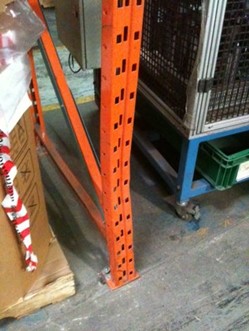
Unprotected upright
While racking systems are extremely efficient structures for supporting vertical loads, they are generally not designed to withstand strong forces caused by forklift impacts. Guarding accessories are elements added to uprights or columns, strategically installed in high-traffic locations, and offering rack protection by providing a barrier to partially absorb/deflect collisions, reducing the effects of their impact. Installing racking protection is one of the best ways to minimize forklift damage. Using inadequate racking protection devices such as wood poles will give you a false sense of security and compromise warehouse safety.
If it is not specifically designed for its use, it will be easy to dislodge upon impact, leaving your rack unprotected. Because it reduces recurring upright replacements and operation downtime, rack protection is a cost-effective solution that reduces maintenance costs. For more information, read about safety tactics to eliminate rack damage in your warehouse.
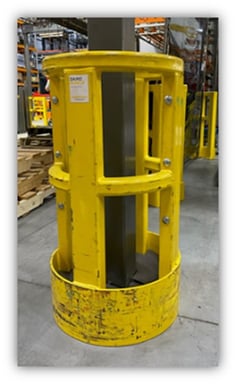
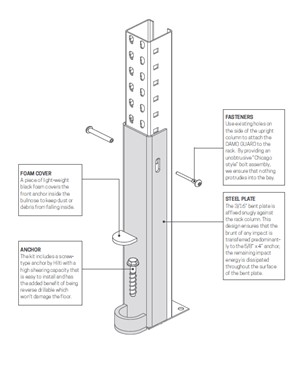
Adequate protection devices
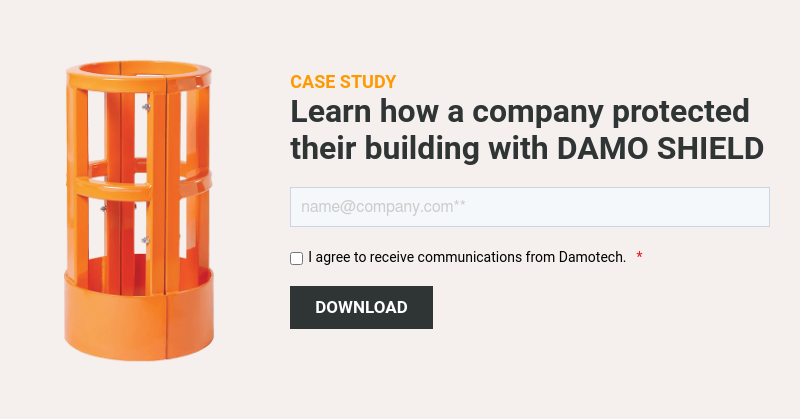
Honorable/Dishonorable Mentions
DO NOT ignore your pallet racks' current condition
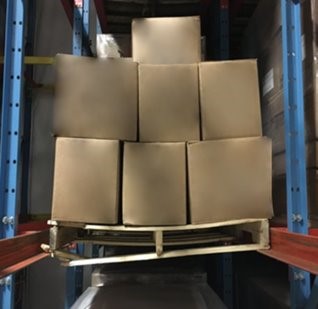
Damaged pallet
Pallets are critical for supporting and moving your products. They are an important part of the supply chain and can be found in different dimensions, types, and materials. Regularly checking to ensure that pallets are in good condition is essential. If a damaged pallet is found, it should not be used to store material in racks. Ignoring the condition of the pallet or not choosing the one that is compatible with the application can result in unwelcome consequences.
DO NOT take unnecessary safety risks
Even in the safest warehouse, some risks will always subsist. It is important to avoid putting yourself in situations that could harm you or damage your environment. For example, walking under a pallet rack that does not have the proper protection devices, such as wire mesh decking, is highly unsafe.
Racks are not designed to be used as ladders. Climbing on them can be extremely dangerous; not only can the person fall from a dangerous height, but there is also the risk of worsening existing damage to braces. Do not allow operators to climb onto a pallet rack or a live pushback lane to attempt to clear a stuck pallet, as the risk of serious injury is high.
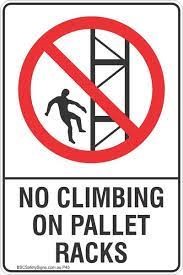
Example of a sign for not climbing on racks
DO NOT ignore rust on rack components
When exposed to the environment or chemical products, racks may develop rust, especially around parts where the metal is exposed to air and moisture. This is an important issue that needs to be addressed because rust can lead to a dangerous situation and costly problems, usually measured in weeks—not days or hours.
It starts with deposits on the surface of the metal with a red, black, or white coloration. It then leads to corrosion and decay that develops to a point where the base metal is completely penetrated and removed. The steel used to build those racking systems will slowly degrade over time. Covering rusted parts with paint will not stop the degradation process of your rack; it will only temporarily prevent more humidity from interacting with the steel.
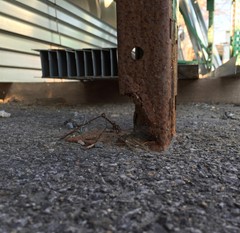
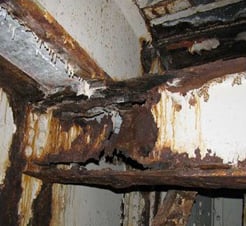
Excessive rust on rack components
DO NOT improperly shim your rack uprights
When your rack is out-of-plumb and needs to be put back in a vertical position, it is important to make sure that you use the adequate type of shims for your baseplates. Using shims not made of appropriate material, like wood, for example, can result in an unstable rack that can compromise its safety. Make sure to have a steel shim that covers the baseplate safely anchored to the ground.
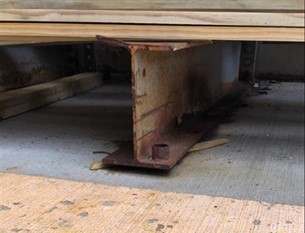
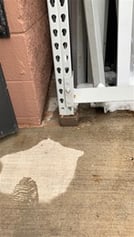
Inadequate shims
Pallet racks play a crucial role in the efficiency and safety of a warehouse. Maintaining their integrity and knowing how to use them most safely will ensure the safety of your employees, reduce downtime, prevent accidents, and optimize overall warehouse productivity!