In the bustling world of warehouses, forklifts are crucial in efficiently transporting heavy loads over short distances. However, their frequent use, coupled with the sometimes hasty operation, poses a significant threat to the integrity of rack systems.
Five Frequent Ways Forklifts Damage Pallet Racks
Collisions between forklifts and racks can have far-reaching consequences, making it imperative for warehouse operators to understand how these collisions occur and, more importantly, how to prevent them. In this article, we delve into the top five ways forklifts can damage racks, offering insights into the common scenarios and practical solutions to mitigate such risks.
1. Forklifts Backing Into Racks Across the Aisle
![]() |
![]() |
Figure 1. Removing a pallet from a rack slot. | Figure 2. Deformed rack column base. |
When retrieving a pallet, a forklift operator must simultaneously clear it from its slot and ensure it doesn't collide with anything across the aisle. Typically, a novice driver approaches this task with great caution, investing ample time. With growing experience and confidence, there might be an inclination to increase speed, and the forklift may impact the rack across the aisle, resulting in rack damage. The impact's energy transfer is directly proportional to the square of the lift's speed—underscoring the notion that speed threatens the integrity of racks.
Narrow or obstructed aisles heighten the risk of such collisions. Deploying the appropriate forklift type in alignment with aisle dimensions is imperative. Further insights on this connection can be found in our article discussing the correlation between forklift types and aisle widths.
To mitigate potential damages, it is advisable to incorporate sufficient column protection. Additional solutions encompass using impact and proximity sensors, regular and thorough driver training, specialized training initiatives for new drivers during peak seasons, and expanding narrow aisles. A comprehensive overhaul of the warehouse's safety culture might also be warranted.
Problem: Speed and misjudgment during pallet retrieval can lead to collisions with racks.
Solution: Adequate training, proper forklift selection for aisle dimensions, and protective measures like impact sensors and column guards.
2. Forklifts Rear-swinging Racks While Moving Forward (Entering or Exiting an Aisle)
![]() |
![]() |
Figure 3. Forklift turning corners. | Figure 4. Deformed end-of-aisle rack brace. |
On forklifts, the back wheels are the ones providing direction. Think of it as driving your car backward. Because they operate normally in rather tight aisles, the back wheels rotate for the lift to pivot around a surprisingly short radius. When driving forward without a pallet, if a turn is initiated a bit too early near the end of an aisle, the back end may swing drastically and come in contact with the pallet racks (Figure 3 and Figure 4). Again, speed accentuates this issue as the driver may not have enough time to react.
This impact can also happen because of encumbered aisles or misevaluation of the forklift dimensions and the turning radius that the rear end will follow during the turn.
As a precaution, using effective end-of-aisle protection is highly recommended, but like the previous point, training is essential. Some operators equip the lifts with side-mounted safety lights to help forklift drivers better evaluate required turning distances.
Problem: Back wheels providing direction can lead to the rear-end swinging into racks during turns.
Solution: Implementing end-of-aisle protection, thorough training, and the use of safety lights to maintain safe distances.
3. Forklifts' Lifting Masts, Front Forks, or Outriggers Impacting Racks
![]() |
![]() |
Figure 5. Deformed bottom-level rack beam. | Figure 6. Deformed and twisted column post. |
In warehouse operations, forklift components such as forks, lifting masts, and outriggers frequently contribute to rack damage. While loading or unloading pallets on racks, forklift operators inadvertently collide with crucial elements, including beams (see Figure 5), columns (see Figure 6), and anchors. The risk is exacerbated in upper-level racking components, where forklift operators, lacking three-dimensional perception, may encounter fork collisions when positioning pallets at higher elevations. Double-deep racks often witness substantial damage to the initial beam levels caused by the mast, as operators mistakenly use them as a depth gauge while positioning pallets with reach forks. Moreover, forklift outriggers may frequently contact column anchors (especially in seismic zones where larger footplates are required) or directly with the base of rack posts, as depicted in Figure 6.
To proactively address these challenges, deploying cameras at the fork level will prevent beam damage at elevated levels. Additionally, implementing robust column base and footplate guards and outrigger stoppers is a reliable safeguard against damage to anchors, columns, and lower beams, as illustrated in Figure 5.
Problem: Forklift components impact beams, columns, and anchors during loading and unloading.
Solution: Utilizing cameras at fork level, employing strong column base guards, and installing outrigger stoppers to prevent damage.
4. Forklifts Repeatedly Brushing Pallets and Merchandise with Racks
![]() |
![]() |
Figure 7. Deformed diagonal brace. | Figure 8. Deformed back column. |
The frequent friction between pallets and horizontal or diagonal braces during the placement and retrieval of pallets in slots is a common cause of racking damage (Figure 7). This issue is closely tied to the angle of approach of the pallet, which, in turn, is influenced by aisle width and clearance required to make the turn before the pallet is positioned or after it is retrieved. Another contributing factor may be excessively deep or wide pallets for the designated slots. It's crucial to note that pallets should maintain a 3-inch clearance from rack uprights and a 6-inch clearance from other pallets.
Damage often occurs when the load is elevated for removal while the pallet is in slight contact with a brace, resulting in a distinctive bent lip on the rack brace. Another damage involves crushing the back column upon entering the slot, as illustrated in Figure 8.
Effective solutions to prevent such damages include ensuring that pallet dimensions and aisle width are appropriately matched. Additionally, deploying upright side protection barriers or side panels provides an added layer of protection against potential harm to the rack system.
Problem: Friction during pallet placement and retrieval damages braces and columns.
Solution: Ensuring proper pallet dimensions, aisle width, and protection barriers and side panels.
5. Forklifts Unclipping and Overloading Beams during Pallet Loading or Unloading
![]() |
![]() |
Figure 9. Deflected rack beam. | Figure 10. Partially detached beam connector. |
Even though beam connector safety pins are a mandatory requirement by code, inspections often reveal detached or partially detached beam connectors (Figure 10). According to rack design code standards, each safety pin should provide a minimal 1000 lb uplift resistance. Despite this, the formidable strength of certain forklifts makes it possible to break these safety devices when lifting a pallet loaded with rigid products.
The consequences of overloading beams can be severe, leading to permanent deformation that necessitates replacement. Forceful dropping of loads can induce local deformation on the top surface of the beam, potentially causing cracks in beam welds and damaging the connection holes in the column. These issues collectively impact the overall performance of the rack system and may even result in a catastrophic collapse.
Enhancing driver training programs and conducting regular inspections of the racks is imperative to address these concerns effectively. By prioritizing safety through comprehensive training and consistent assessments, warehouses can significantly reduce the risk of structural failures and ensure the longevity of their rack systems.
Problem: Beam connectors detach due to overloading, risking permanent deformation and collapse.
Solution: Thorough training, regular inspections, and adherence to safety guidelines for beam connectors and load capacities.
Forklift Damage Preventative Measures and Safety Tips
Racks are highly efficient structures that require components to be free from damage to fully bear the loads placed on them. They are typically not designed to resist impact. Although some damages could be minor, accumulated damages over time can result in catastrophic consequences such as the collapse of a racking system. Therefore, maintaining healthy racks is essential to their performance, and taking the following preventive actions is a great way to stop the endless cycle of replacing damaged parts:
- Train forklift operators thoroughly and regularly;
- Inspect racks regularly;
- Keep aisles clutter-free;
- Match pallet size, rack size, and aisle width;
- Protect braces at pallet level with upright side panels;
- Use base guards and/or column guards to protect column base and anchors;
- Use outrigger stoppers to protect bottom beams;
- Use fork-level cameras to protect top beams;
- Use end-of-aisle protection and side-mounted safety lights on the forklifts;
- Use rear-view-mirrors and proximity sensors to prevent backing incidents;
- Check how the warehouse culture affects rack damage.
By embracing these preventative measures and safety tips, warehouses can safeguard their rack systems, ensuring they remain robust, efficient, and free from potentially catastrophic damage over time.
Finding the Best Forklift Safety Solutions
Lastly, find a reliable and experienced rack safety partner who can guide you in finding the most suitable and efficient rack safety solutions to not only prevent or repair damage to your racking systems but also to help you improve the overall safety of your warehouse.
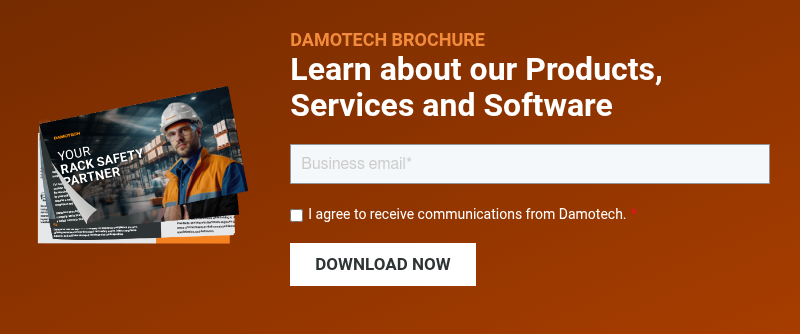