The Cost of Poor Warehouse Leadership: High Turnover, Low Safety, and Chaos
Warehouse leadership isn’t just about hitting productivity targets but protecting your people and infrastructure. Poor leadership doesn’t just cost you efficiency; it increases safety risks, damages your racking systems, and puts your operation at risk.
Imagine a facility where new hires are thrown into tasks with little guidance, experienced workers feel micromanaged, and safety violations pile up because no one knows what’s expected of them. Turnover skyrockets, productivity plummets, and accidents become routine.
The problem? A one-size-fits-all leadership approach that doesn’t adapt to the team’s needs.
✔ Not sure how your leadership style stacks up? Take our quick diagnostic.
Great warehouse managers lead differently. Here’s how to level up your leadership and protect your facility from the inside out.
Why Warehouse Leadership Matters More Than Ever
Leadership isn’t just about hitting KPIs in today’s fast-paced logistics and manufacturing environment. It’s about creating a culture that prioritizes safety, empowers staff, and preserves the physical infrastructure, including your pallet racking systems.
When warehouse leaders fail to adapt their management style:
- New hires are left untrained.
- Veteran employees feel micromanaged.
- Safety violations go unchecked.
- Damage to equipment and racks increases.
- Turnover and absenteeism spike.
The cost? Soaring operational risk, higher liability, and thousands in preventable repairs.
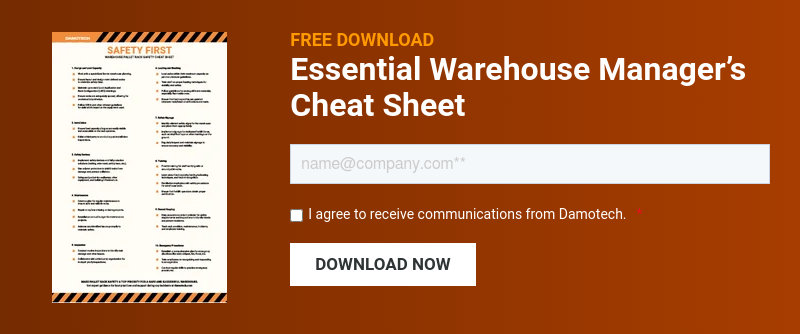
Adaptive Leadership: What It Is and Why It Works
Effective warehouse managers don’t treat every employee the same. They adapt.
The Hersey-Blanchard Situational Leadership Model offers a proven way to do this. This model helps managers tailor their leadership approach based on an employee’s experience, skill level, and confidence, and identifies four leadership styles (Blanchard, Zigarmi & Zigarmi, 1985):
Leadership Styles (S1–S4)
- S1: Directing – High directive, low support. Ideal for brand-new hires.
- S2: Coaching – High directive, high support. Best for employees lacking confidence.
- S3: Supporting – Low directive, high support. Empowers skilled but hesitant workers.
- S4: Delegating – Low directive, low support. Reserved for self-motivated pros.
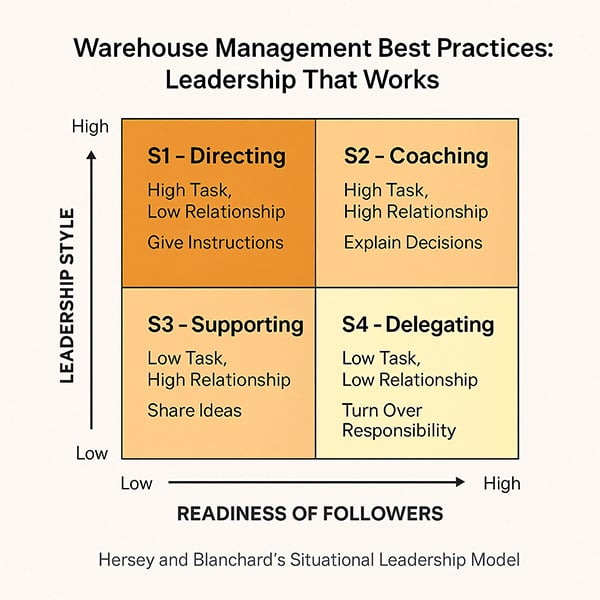
To apply this method, managers must first assess their employees’ development levels (Hersey, Blanchard & Johnson, 2007):
Development Levels (D1–D4)
- D1: Enthusiastic Beginner – High motivation, low competence.
- D2: Disillusioned Learner – Growing skills, waning confidence.
- D3: Capable but Cautious – Competent, needs encouragement.
- D4: Self-Reliant Achiever – Highly competent and motivated.
Goal: Match the leadership style to each team member’s development level.
Situational Leadership in Action
Scenario | Development Level | Leadership Style | Why It Works |
---|---|---|---|
New hire assigned to the inventory | D1 | S1 (Directing) | Step-by-step clarity reduces mistakes. |
Forklift operator making errors | D2 | S2 (Coaching) | Builds skills while reinforcing safety. |
Experienced technician unsure about leading | D3 | S3 (Supporting) | Encouragement unlocks initiative. |
Veteran supervisor managing audit | D4 | S4 (Delegating) | Autonomy drives efficiency and trust. |
Safety Outcomes of Adaptive Leadership
Applying adaptive leadership isn’t just smart—it’s essential for safety. The Swiss Cheese Model shows that accidents happen when minor oversights align.
Adaptive leadership plugs those gaps:
- Boosted Productivity: Workers thrive when given the right balance of instruction and support (WERC, 2021).
- Lower Turnover: Employees stay when they feel seen and supported.
- Stronger Teams: Clarity in expectations builds cohesion and morale.
- Improved Safety: Tailored guidance reduces the risk of injuries (OSHA, 2022).
Real-World Case Studies
🌟 Success: Carlos and Mark
Carlos, a D1 new hire, struggled with inventory management. His manager, Mark, began with S1 Directing—daily check-ins, clear procedures, and hands-on support. Over six months, Carlos progressed to D4 and now trains others. This is adaptive leadership at its best.
❌ Failure: Tom’s One-Size-Fits-All
Tom treated all employees the same: “Sink or swim.” New hires were overwhelmed. Mid-level workers got no feedback, and senior staff were micromanaged. Turnover soared, and safety violations multiplied. A rigid leadership style cost the operation dearly.
Top Warehouse Management Tips for Stronger Leadership
- Assess each employee’s experience and confidence levels.
- Adapt your leadership style (S1–S4) to match their development level (D1–D4).
- Train and onboard thoroughly—don’t rush new hires onto the floor.
- Balance direction and support based on the task and the person.
- Delegate appropriately to experienced team members.
- Use software and inspections to back leadership with data.
- Model accountability, communication, and safety-first thinking.
Call to Action: Lead Safer, Smarter, and Stronger
Want to elevate your leadership while reducing safety risks? Damotech helps warehouse managers align their leadership style with operational safety.
From engineering assessments to rack safety software, we equip you with the tools to lead a safer, more productive warehouse.
Ready to improve leadership and rack safety? Talk to a Damotech Expert.
Quick Diagnostic: Are You Leading Adaptively?
Use these simple yes/no questions to assess if your leadership style supports both safety and performance in your warehouse.
If you answer “no” to two or more, it’s time to adapt your approach.
Self-Check Questions
- Do you adjust your leadership style based on an employee’s experience or confidence level?
- Do new hires in your facility receive structured onboarding and job-specific safety guidance?
- Do struggling employees receive coaching, not just correction?
- Do you regularly give positive feedback to your top performers, or just redirect when things go wrong?
- Do you know which of your team members are ready for more autonomy, and trust them to work independently?
How to Use This Self-Diagnostic
- 4–5 Yes Answers: You’re likely leading with adaptive awareness.
- 2–3 Yes Answers: Some blind spots to fix.
- 0–1 Yes Answers: Your leadership style may be putting safety and retention at risk.
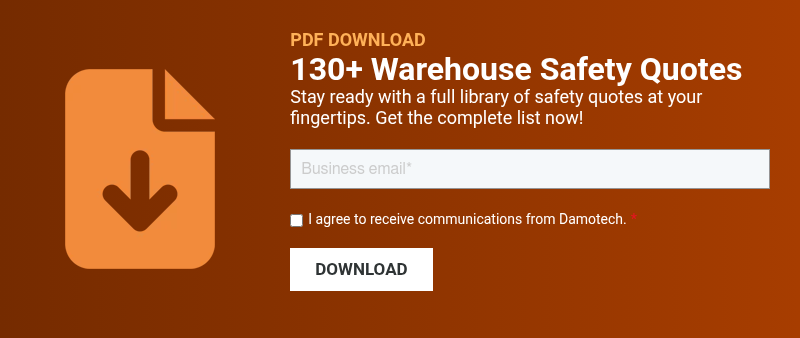
FAQ
What is the best leadership style for warehouse managers?
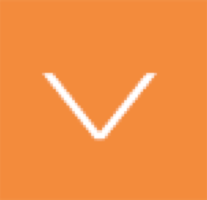
Adaptive leadership is best. It tailors supervision to each team member’s experience and confidence, boosting both safety and efficiency.
Why is adaptive leadership necessary in a warehouse?
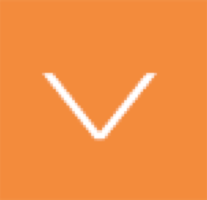
Because teams are diverse, matching leadership to development levels prevents safety risks, improves morale, and boosts retention.
How does leadership impact warehouse safety?
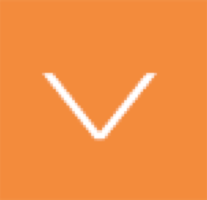
Strong leadership reduces the likelihood of oversight and encourages better adherence to safety protocols, inspections, and damage reporting.