Being a warehouse manager is a balancing act, one that requires making the right business decisions while facing whatever the day may bring. You must maintain top warehouse efficiency, fulfill orders, respect deadlines and budgets, all the while ensuring worker safety. So how then, do you make informed decisions? This is where warehouse KPIs can be a valuable tool for managers and operators.
First, let's review what the terms Key Performance Indicator (KPI) and warehouse benchmark mean and how they can be useful to the warehouse environment. Simply put, they allow us to evaluate our progress or success at reaching specific targets, in this case for warehouse efficiency.
Key performance indicator definition
Key Performance Indicators are measurements of performance that help leaders and managers gauge the effectiveness of a team, project, or even a company. It’s a way to measure objectives as part of a greater strategy or as a method to align everyone to a goal, but it is not the goal. KPIs may focus on broader activities or be very targeted towards specific metrics or processes.
Warehouse benchmark definition
A warehouse benchmark is used to measure a company’s performance, and it works by comparing the metrics measured in the company with industry best practices or other companies. It’s a way for businesses to build their strategies, improve on existing methods, or plan for the future.
Warehouse KPIs |
To monitor progress or performance and understand where you are with set goals or targets. |
Warehouse benchmark |
To compare your performance with others – useful for setting goals or targets. |
In other words, warehouse KPIs can help managers measure performance, and warehouse benchmarks can help identify opportunities and drive improvements.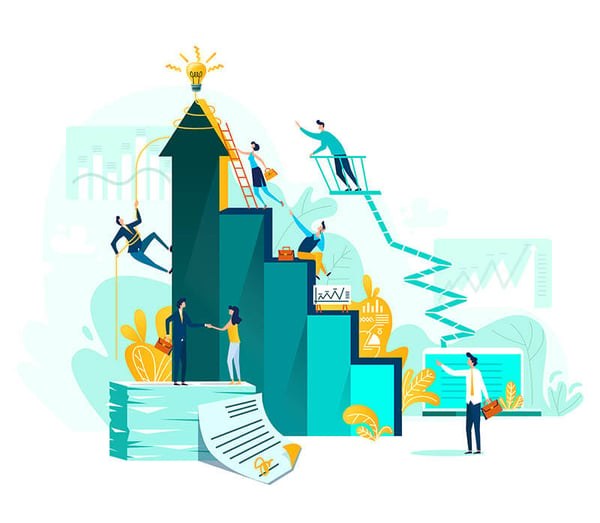
Where to find information on warehousing and industry KPIs?
WERC, the Warehousing Education and Research Council conducts an annual study to identify those key metrics that warehouse professionals can use to evaluate their performance on everything from order-picking to capacity utilization, among many other parameters. It’s based on a survey that is sent out to their members and information gathered from readers of DC velocity magazine, a publication that caters to logistics and supply chain executives.
To get started on warehouse benchmarks and to find data commonly measured in the industry, this paid resource is practical.
Top WERC performance metrics for warehouses
According to the WERC 2016 DC Measures Report the top 5 metrics that mattered most to respondents were:
- On-Time Shipments (Customers)
- Average Warehouse Capacity Used (Capacity)
- Order Picking Accuracy (Quality)
- Dock-To-Dock Cycle Time in Hours (Operations)
- Internal Order Cycle Time in Hours (Customer)
Three of the top 10 metrics in the WERC report1 were employee-related: contract employees to total workforce, overtime hours to total hours, and part-time workforce to total workforce.
Because every warehouse has its challenges, experts recommend building your own set of KPIs.
Your warehouse KPIs dashboard
You ought to look at warehouse benchmarks with the intent to improve your own, without necessarily matching them. Choose those that matter to you or your organization instead of using a list that works for someone else. For example, you can target a specific area of your facility or production and define your KPIs around them. When that area is improved, you can move on to another. When crafting your warehouse KPIs, in addition to choosing objectives relevant to your department, it’s wise to also align them with the KPIs of the organization.
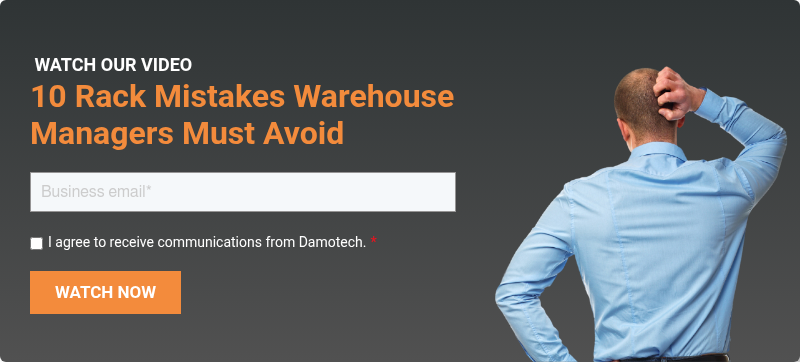
Top warehouse KPIs
To provide a starting point, here are some examples of KPIs you could add to your warehouse KPI dashboard:
1. Warehouse Safety KPIs
Measuring safety is not just about tallying accidents. Examples of safety KPIs include lost time on reported incidents, injury incidence rate, or equipment breakdown. It can also be about % completion of planned inspections, % of damaged components in racks, or employee training (% required vs. % completed). This is an area where the Damotech Platform and its inspection dashboard will come in handy.
2. Storage and inventory KPIs
Measure the turnover or cost of inventory. Slow-moving inventory takes up valuable storage space and decreases your warehouse's efficiency. For instance, you can measure storage productivity by tracking inventory volume per square foot of the warehouse.
3. Warehouse productivity KPIs
Picking and packing KPIs are significant for distribution centers since customer satisfaction may depend on this, and they require much labor. Examples may be cost of picking labor, picked orders hourly, cost per picked items, or measuring for accuracy and speed in shipping out the orders. You may also wish to track equipment effectiveness performance.
4. Warehouse Operation Efficiency KPIs
You can focus on your shipping or receiving area and the workers in that department, tracking the total number of items shipped versus your projected numbers, on-time deliveries, an order's cycle time or lead time, the accuracy of orders, perfect order rate, or rate of returns.
5. User Satisfaction KPIs
Measure the satisfaction of workers, partners, suppliers, or customers in your warehouse KPI dashboard.
6. Workforce KPIs
Measure employee well-being, rate, type of injuries, overtime hours worked, part-time to total workforce, annual turnover rate, or labor costs.
7. Cost-related KPIs
All sorts of KPIs here related to labor, cost of inventory, warehouse space, and assets like equipment, storage rack systems, lifting devices, and vehicles. You could also measure the usage of consumables, such as packing materials or energy use.
8. Time-related KPIs
Order cycle time, order fill rate, lead time, or identifying peak hours or seasonal demands.
The link between warehouse KPIs, sustainability, and social responsibility
Supply chains have evolved and are now moving towards a more sustainable approach to warehousing and distribution. However, uniform sustainability metrics are just starting to really be defined and even requested. Examples of indicators being measured are targets associated with the consumption of energy, water, or packaging. Also measured are waste reduction2, energy efficiency3, carbon footprint, or recycling.
To devise your own KPIs, start with these steps:
- Focus on a limited amount of warehouse KPIs
- Establish targets for each KPI
- Define "success" and how you will measure it
- Document them in Excel or other software
- Set a timeframe
- Decide on how you will track them
- Report and adjust
1- Focus on a limited amount of KPIs
The important thing is to choose those that matter to you or your organization instead of using a list that may work for someone else. For example, you can target a specific area of your warehouse or production and define your KPIs around it. Alternatively, track more high-level KPIs to help you discover some weaknesses or areas of your operations that could benefit from some improvement — focusing on a small, but vital set of KPIs will bring you more value and make it easier to take action to improve the warehouse efficiency.
2- Establish targets for each KPI and be clear about the desired outcome
Determine why you are measuring them, and what are your objectives? KPIs are strategic. Your focus should be on what is essential and measurable. For example, are you doing this exercise to save money, create a safer environment, or cut down on production lead time? Reaching out to employees or colleagues can help you in deciding what to tackle. Do you have concerns about something and need to check whether your instincts are on the ball? Or maybe you've purchased new equipment and wish to measure its ROI? Whatever the reason, make sure to track what is useful to you.
3- Define what "success" means
For each KPI, define success either by doing a warehouse benchmark against the industry's best practices or setting your own objectives. Next time you are mingling with peers or attending an industry event, why not ask what they measure in their warehouse. Be specific in defining your desired outcomes and know that a warehouse KPI is not a goal, but an indicator4.
4- Write them down and decide how you will measure
Prepare your warehouse KPI dashboard and determine how you will track the desired outcome. One brief sentence for each is enough. Extracting the data is where things may vary from one company to another because of the variety of tools being used, and what you have on hand will invariably influence how you measure. For instance, if you are using a warehouse management system (WMS), some data may already be available or integrated into your software. If you use a manual system, you will have greater control over the specific metrics you wish to track, but it will mean more work on the warehouse floor to input the data. Automated technology should make it easier to collect data and track your KPIs. For instance, if you automate inventory management, then you’ll maintain more accurate stock in place.
5- Set a time frame
Making sure your goals and warehouse KPIs are time-bound and have a set deadline will give you a clearer picture of your operation. However, equally important is tracking your progress along the way to assess how effective you were in developing the KPIs in the first place. Consistently monitor the information in your warehouse KPI dashboard against your objectives and adjust them if necessary.
6- Decide on how you will track your KPIs
You may have difficulty or need help obtaining information to generate your indicators. Data capture is essential for proper tracking in a warehouse operation. The implementation of technology in a warehouse will deliver the valuable info you need. When a warehouse management system (WMS) is used and combined with data capture and automation - barcodes and scanning, voice technology, mobile devices and computing, radio frequency identification (RFID) – it provides accurate info and offers boundless possibilities in reporting. As a central space for data, an ERP is also valued.
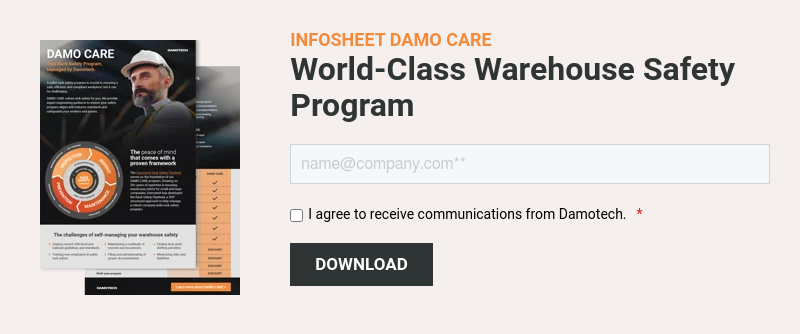
7- Report and adjust
Turn spreadsheets into great visuals. When you are done measuring, a visualization tool such as the one provided in this racking assets management software can provide insight and help communicate the data you've collected to your team or senior management. Data visualization can change not only how we look at the data but how fast and effectively we make informed decisions. Here are some free online tools you can use to convert your data into sharp graphics: Tableau Public, ChartBlocks, or RAW Graphs.
Warehouse KPIs & warehouse benchmarking key take away
Tracking data through a warehouse KPI dashboard can be valuable in decision-making, and a good driver for change in your organization. It can help you be more transparent with your employees, align your team to your objectives and serve to better communicate how well (or not) they are doing in their job.
Finally, best not to start with too many. Even small changes can generate big savings that will impact your bottom line and improve warehouse efficiency. Hopefully, the suggestions above can get you started on making more informed decisions based on measurable data. And, when you reach important goals, do communicate and celebrate them!
References & Footnotes
(1) Tillman, J., Manrodt, K., and Williams, D. (2018), WERC DC Measures: 2016 Trends and Challenges, Warehousing Education and Research Council, USA
(2) Bouchery, Y., Ghaffari, A., Jemai, Z. (2010) Key Performance Indicators for Sustainable Distribution Supply Chains: Set Building Methodology and Application, Laboratoire Génie Industriel, Ecole Centrale Paris.
(3) May G., Taisch M., Prabhu V.V., Barletta I. (2013) Energy Related Key Performance Indicators – State of the Art, Gaps and Industrial Needs. In: Prabhu V., Taisch M., Kiritsis D. (eds) Advances in Production Management Systems. Sustainable Production and Service Supply Chains. APMS 2013. IFIP Advances in Information and Communication Technology, vol 414. Springer, Berlin, Heidelberg
(4) Marr, Bernard. “What Is a KPI?”, 12 Aug. 2019, www.bernardmarr.com.