As a warehouse manager, ensuring the safety and well-being of your employees, visitors, and equipment is paramount. Rack safety is a crucial aspect of warehouse safety that demands special attention.
Imagine your warehouse buzzing with activity—forklifts maneuvering swiftly, personnel bustling about, and racks storing various products. It’s a dynamic environment requiring constant vigilance. Maintaining a safe work environment, adhering to regulations, and following industry best practices are pivotal in safeguarding your workforce and optimizing warehouse operations.
To prioritize rack safety effectively, warehouse managers and workers should understand the health of their racking systems. This blog delves into the importance of implementing and maintaining a comprehensive rack safety program within your warehouse. With a strong emphasis on rack safety, we will uncover essential factors to consider and share valuable best practices, enabling you to enhance rack safety, minimize potential risks and downtime, and establish a secure and efficient warehouse environment.
The impact of rack damage on your people and bottom line
Before exploring the significance of implementing a rack safety program, it’s crucial to understand that overlooking rack safety can result in severe repercussions, such as injuries, property damage, and even loss of life. Rack damage can have far-reaching consequences, causing substantial financial and operational disruptions that impact inventory, finances, productivity, efficiency, and customer perception.
These consequences include:
- Inventory loss: Falling or damaged products result in replacement costs and potential revenue losses due to shortages or delays.
- Financial impact: Rack repairs or replacements incur costs, affecting the business’s bottom line. Employee injuries from collapses lead to medical expenses, lost wages, and potential legal fees, impacting finances further.
- Downtime and lost productivity: Temporary closures of sections or the entire warehouse cause downtime and delayed order fulfillment, affecting revenue and customer satisfaction.
- Decline in employee morale: When employees are often confronted with rack damage, it can result in safety concerns, decreased job satisfaction, heightened work stress, and workload, diminished productivity and efficiency, reduced engagement and motivation, and disrupted team collaboration and coordination.
- Operational inefficiencies: Material handling, order picking, and inventory management become less efficient, resulting in increased labor costs and reduced operating efficiency.
- Damage to reputation and customer relationships: Product damage and order delays negatively impact a company’s reputation and strain customer relationships, leading to lost business opportunities.
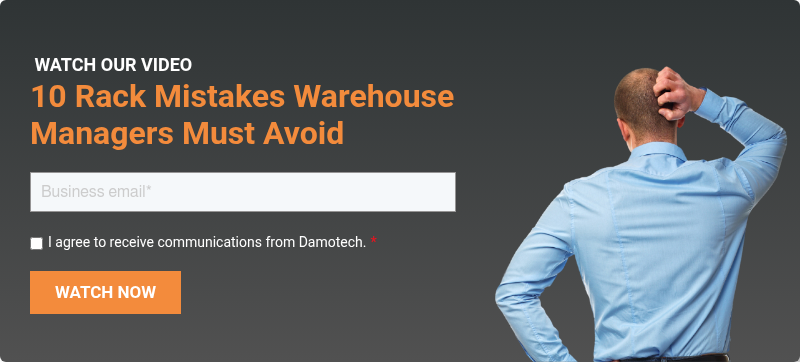
The benefits of implementing a rack safety program
In contrast, giving priority to rack safety can have a positive impact on your company’s bottom line. It helps:
- Prevent accidents.
- Minimize the risk of property damage or injuries.
- Reduce workers’ compensation claims, lawsuits, and costs associated with repairs or replacements.
By investing in rack safety, companies ensure their employees’ well-being and demonstrate their commitment to their safety, increasing employee satisfaction, productivity, and retention rates. And in turn, it also positively impacts the company’s overall health, safety, and environment (HSE) performance.
A well-designed and comprehensive safety program is essential for any successful warehouse operation. It provides genuine peace of mind and delivers substantial cost savings. Let’s explore the key advantages it brings:
Employee Well-being
A rack safety program places employee well-being at the forefront, ensuring the protection of personnel, the equipment they utilize, and the products they manage. It can achieve this through:
- Adoption of safe procedures.
- Proactive recognition and resolution of potential risks.
- Ensuring workers are well-informed about the appropriate actions to take when rack safety concerns arise.
Operational Efficiency
A well-executed program manages rack damage, thereby reducing maintenance costs, product loss, and costs associated with injuries while improving processing efficiency. It also helps eliminate or decrease downtime caused by damaged racks, ensuring their swift repair or replacement before they impact operations.
Regulatory Compliance
When you adhere to a rack safety program, you showcase your company’s compliance with regulations, such as OSHA, ANSI, and RMI standards, reducing the likelihood of fines. It highlights a commitment to putting worker safety first and ensuring the longevity of your warehouse infrastructure.
What is a rack safety program blueprint, and how can it help?
A rack safety program blueprint is a map you can follow to avoid the risks and unknowns of trying to go alone. An example of a complete and efficient safety program blueprint is the Rack Safety Flywheel.
The Safety Flywheel illustrates how companies can ensure safety in their operations. It breaks down the safety process into practical steps, represented by the four quadrants of the wheel.
Figure 1. Example of a rack safety flywheel model
As effort is invested into each section, the Flywheel gains momentum and enhances warehouse and rack safety in companies’ facilities, creating a safer environment for employees and assets. Implementing a flywheel model can help you achieve sustainable growth and success by focusing on key areas and generating momentum toward their objectives.
Sustaining the wheel’s motion is crucial because ensuring rack safety is an ongoing, continuous process that cannot be initiated or completed singularly, requiring continual effort and dedication.
EXPLORE THE WAYS IN WHICH OUR BLUEPRINT FOR A RACK SAFETY PROGRAM
CAN BENEFIT YOUR COMPANY.
Combining in-house and third-party rack safety knowledge for an effective program
While it’s possible to try tackling the project alone, doing so can be challenging, and success may be less likely. Managing everything alone is not easy, so getting help from a third party can make the process easier and faster while giving you access to expertise you may not have in-house. The best way to create an effective rack safety program is to combine your knowledge with third-party expertise.
Using in-house and third-party expertise, you can be confident that you’re setting up a safety program that follows industry-leading standards.
In-house Rack Safety Expertise
In-house expertise pertains to employees' knowledge and know-how contributing to warehouse safety.
Independent Rack Safety Knowledge
Third-party knowledge refers to the insights and expertise of professionals experienced in the field of rack safety. Seeking the know-how of independent experts, particularly that of a rack safety engineer, guarantees an objective and uniform evaluation of rack safety implementation across the entire company.
The four main sections of an optimal rack safety program
A comprehensive and efficient rack safety program should comprise four main areas. If you initiate and maintain the process, there is no initial or final step in ensuring rack safety, as it is ongoing.
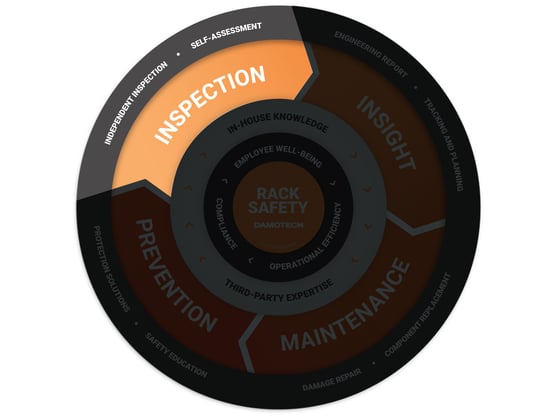
Pallet Rack Inspection
How often your racking should be inspected varies based on factors such as the speed of your operations, the size of your warehouse, and damage occurrence. As a general rule, warehouse staff or rack safety experts should conduct monthly routine inspections, and third-party rack experts should perform yearly compliance inspections.
Reasons to regularly perform inspections:
- Safeguarding employee safety.
- Ensuring regulatory compliance.
- Protecting inventory.
- Reducing costs.
- Enhancing operational efficiency.
Routine Inspection
Routine inspections are essential to warehouse rack safety. Warehouse personnel or third-party rack experts should regularly inspect pallet racks to identify anomalies in the racks and ensure they are safe to use. These routine rack inspections are not formal inspections but rather evaluations of the safety level of the racks.
When opting for a third-party routine inspection, a rack expert possessing proper training, experience, and time can:
- Provide a more impartial evaluation and identify issues a busy employee might overlook.
- Assist in tracking key performance indicators (KPIs) and maintaining updated records of rack maintenance interventions.
- Provide expert advice and professional recommendations on the best solutions.
- Assist in developing a maintenance program.
- Assess the progress of safety initiatives.
- Identify trends or recurring issues.
- Provide valuable insights for continuous improvement.
Compliance Inspection
Professionals specializing in pallet racks should conduct compliance inspections of your racking systems. They comprehensively assess the rackings and can discover potential risks that may have gone unnoticed.
When should you seek the expertise of a third-party pallet racking specialist for a compliance inspection? CLICK HERE TO FIND OUT.
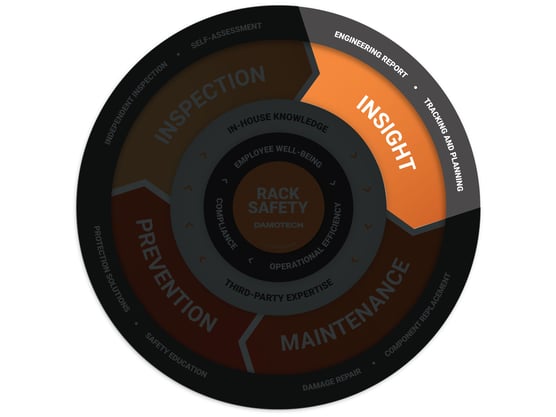
Insight After Rack Inspections
Access to insights is crucial as they enable you to make informed choices regarding the safety and integrity of your racks.
Engineering Report
Engineering reports play a significant role in providing technical data following rack inspections. They include information on the components most impacted, various recommendations for replacements or repairs, and the prioritization of remedial measures.
Tracking and Planning Maintenance Needs
Tools and software for tracking and planning translate data into actionable measures. Such tools help monitor progress and analyze essential performance metrics (KPIs).
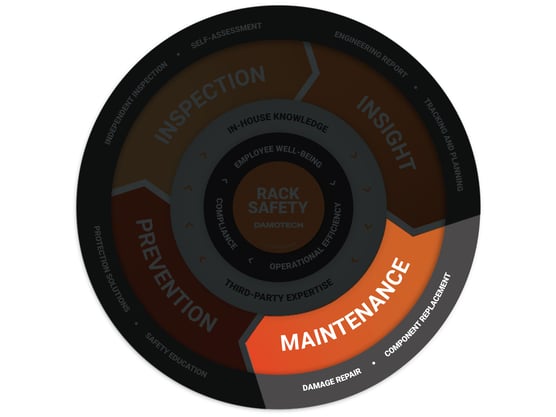
Pallet Rack Maintenance
Detecting anomalies through inspections is just the beginning. Having data will only enhance warehouse safety if a company proactively resolves the noted concerns. This is why rack maintenance is essential.
Replacing Rack Components
Warehouse operators are no strangers to encountering damaged rack components such as sheared upright legs, deflected beams, and dented braces. The causes of these damages can vary, ranging from a forklift colliding with a pallet rack to an absence of adequate training related to warehouse safety. In such cases, choosing to substitute the damaged component with a new part from the Original Equipment Manufacturer (OEM) can be a good tactic. This method proves advantageous when surplus resources are available, allowing for a prompt replacement.
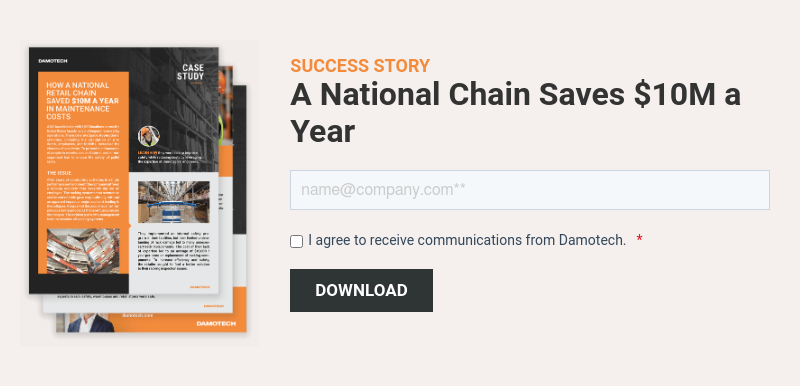
Repairing Rack Damage
Did you know you can often repair damaged upright columns and rack braces instead of replacing them? A rack repair kit effectively restores the columns to their original load capacity and stability.
Furthermore, a brace repair kit can address issues with missing or bent horizontal or diagonal braces on warehouse racks. This way, you can replace damaged rack braces instead of replacing the entire upright. Discover the numerous advantages of using a column repair kit or brace repair product to fix a damaged rack.
Prevention to Maintain Warehouse Safety
Maintaining the safety and reliability of warehouse racks relies on proactive measures to prevent damage and ensure smooth operations. Instead of waiting for problems to occur, adopting a proactive approach to safeguarding products, equipment, and infrastructure and offering employees comprehensive training proves significantly more effective.
Solutions to Protect Racks
Including rack protection solutions in any rack safety program is vital. Efforts focused on prevention can effectively lower the risk of incidents, decrease maintenance expenses, and extend the overall lifespan of racks.
Protection solutions include upright guards, end-of-aisle protectors, and various protection products for walkways, infrastructure, equipment, and building columns.
It is advisable to consult a rack specialist to establish an optimal strategy for safeguarding vulnerable or high-risk areas. They possess the expertise and knowledge to recommend the most suitable protective solutions. Under their expert direction, a company can outfit its warehouse with optimal protection measures.
Rack Safety Training
Safety education is crucial for prioritizing the safety of workers and a warehouse environment. Even with employees’ knowledge, their effectiveness can be limited without proper training. It’s important to educate them about the appropriate safety guidelines and practices within the warehouse.
The training should focus on the core principles of pallet racking, adherence to guidelines, identifying hazards, and adopting suitable response strategies. Employees should be equipped with proper methods to assess pallet rack conditions, prioritize damage, and take necessary actions to resolve issues.
By prioritizing investment in rack safety training, your employees will gain the essential knowledge and skills needed to uphold a safe working environment and effectively mitigate potential hazards. Discover how our rack safety program blueprint can help you in creating an efficient safety program for your warehouse operations.
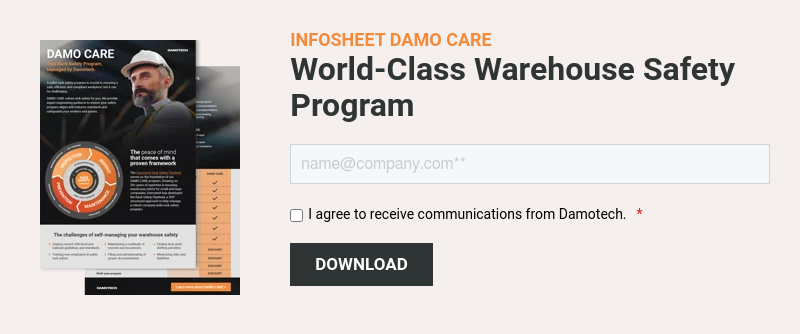
How can experts help you implement and maintain a successful rack safety program?
The process of implementing and upholding an efficient safety program for pallet racks can pose challenges for businesses.
The assistance of an experienced warehouse safety expert can prove invaluable in recognizing and overcoming the obstacles that may impede progress in your company’s rack safety initiatives. These challenges may include insufficient buy-in from management and a lack of awareness, training, resources, momentum, and communication. Also, difficulty measuring success and staying updated with regularly changing regulations can further complicate the process.
By leveraging the expertise and resources of rack safety experts, companies can establish a robust safety program that safeguards employees, protects assets, and ensures compliance with regulations.
DISCOVER HOW EXPERIENCED WAREHOUSE SAFETY EXPERTS CAN HELP YOU ENHANCE YOUR WAREHOUSE RACK SAFETY.