Warehouses vary in size, location, climate, and purpose. While there are plenty of variables at play, they all have one thing in common: a strong warehouse requires effective management to remain safe, efficient, and profitable. As such, some common mistakes can be addressed and avoided in warehouses of any size.
Warehouse Management: Avoiding These 5 Common Pitfalls Will Save You Time
When a warehouse is up and running, it’s easy to get caught up in a routine and continue habits or procedures that are inefficient or downright incorrect. While things might run smoothly enough for a while, cracks in processes can begin to grow, and problems will inevitably worsen. Organizational mistakes can result in everything from lost productivity, missed profitability to even injury.
Whether you’re drowning in paperwork, avoiding warehouse rack inspections or suffering from a lack of employee training, numerous problems can be solved with keen warehouse management.
Keep reading to determine how you can avoid the most common mistakes and save time.
1. Layout and Infrastructure
There are numerous factors at play, but it’s safe to say that nearly all warehouses are not operating at their full potential. According to a survey conducted by Logistics Management in 2018, the average capacity utilization of warehouses was 68 percent.
It’s nearly impossible to completely reset your warehouse’s setup once it’s an established space. Still, it’s worth periodically inspecting and tweaking your setup to ensure you’re maximizing space to meet the demands of your operation. Even if you appraise the layout once a year, you’ll be able to make minor adjustments that encourage maximum efficiency with the use of the space.
Tweaks can be as simple as making the most of vertical space, reshuffling stock based on priority, walking through each worker’s picking path to assess obstacles and slow points, and considering if each department is where it should be. For example, having shipping and receiving located in the same area can often lead to inefficiencies and mistakes. If these can be separated, you will likely notice a decrease in errors.
Your business is constantly evolving, and your warehouse infrastructure should be too. The improvements will likely never end, but you can stay ahead of the curve by continually reassessing your layout.
2. Routine Pallet Rack Inspections
Whether you supervise a single warehouse or operate multiple distribution centers, you must manage and maintain one of your most critical assets: your racking systems. In North America, the law stipulates that company management is responsible for providing a safe workplace to their employees. Putting workers at risk of injury can expose employers to severe liability in case of an accident.
Because of pallet rack safety regulations in North America and the growing demand for warehouse safety, it is required to have and display the load capacity of your racks. Any adjustments made to the pallet rack configuration, such as a change in beam placement or height, must be reviewed by the original manufacturer or competent storage rack engineer before it is put back to use. Damotech offers load capacity calculation and certification services performed by qualified engineers with focused expertise in industrial pallet racking systems.
Racks must also be regularly inspected for damages and anomalies. Forklifts are the main culprit. To learn about the five most frequent ways forklifts can damage racks, read this blog. Ignoring racking issues can cause them to accumulate over time, increasing the potential for a collapse. To learn more about how you can protect and repair pallet racks, click here.
No matter your challenges or the industry you are in, most experts and governing bodies agree to recommend monthly assessments done by warehouse personnel and yearly independent inspections performed by third-party rack experts or engineers.
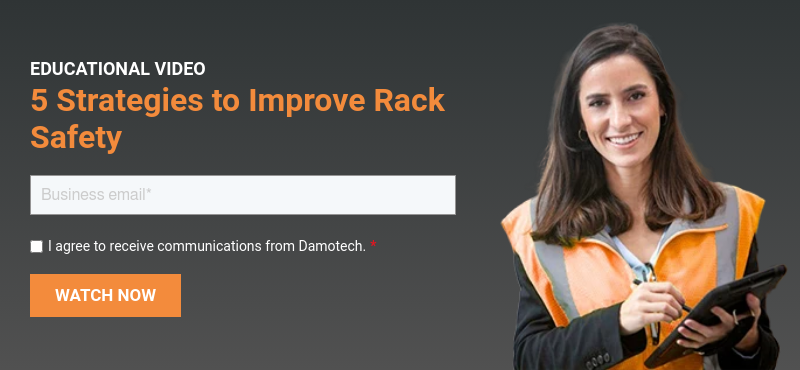
3. Inconsistent Inventory
There’s no denying that taking a physical inventory of your stock can be a costly and laborious pursuit, but cycle counts should not be skipped if you want to maintain a well-managed warehouse. Even if your inventory records are 99 percent accurate, it’s a good idea to keep cycle counts as a safeguard against future discrepancies. The better you know your inventory, the better you can manage your warehouse.
Similarly, it’s important to clean house on the excess stock. You may have items collecting dust as you wait for a rainy day to start moving units. That’s unlikely to happen, however, and the overstock is more likely to clutter your supply chain and slow down work. While there are different variables depending on your industry, it’s wise to avoid stockpiling extraneous items that take up space and impede your warehouse operations.
Ultimately, a well-managed warehouse will be lean and clean, with every stock item and warehouse supply existing in the space for a defined purpose.
4. Embrace Automation
Your inventory will also be easier to manage if you ditch the pen and paper and embrace modern warehouse management software. Physical paperwork will almost guarantee slower processes, missing documents, and, in turn, missing stock.
Fortunately, countless applications are available for all budgets and sizes, and they can help with all aspects of warehouse management. From bookkeeping to inventory management to barcode software for order pickers, there is no shortage of ways you can modernize and streamline your warehouse.
The Damotech Platform helps you keep your rack inspection data in one place. It is the only dedicated rack inspection and asset management software in the industry. Accessible via the cloud, you’ll be able to get a bird’s eye view of your warehouse layout and sort rack inspection data by priority, access photos taken during inspections, and review load capacities by individual pallet location.
In other words, modernizing your warehouse can mean gaining control over everything from inventory to the hands-on safety of your racking.
5. Training and Development
While your stock and infrastructure are integral elements of your warehouse, the most critical moving parts are the actual human beings. It’s easy to rush through training or skip educational sessions that are deemed unnecessary at the moment. Still, a well-trained workforce is imperative to maintaining a safe and prudent warehouse. More than that, your workers will do better work and have more fulfilling careers if they are motivated and given the right resources for success.
While costs and time are often used as excuses to skip out on training, it’s important to remember that it’s far more cost-efficient and easier to train and motivate the staff you currently have rather than hire new workers. Perfection may not be attainable for any leader, but warehouse managers should still strive to grow and evolve alongside their daily demands. In doing so, they can help ensure that their warehouse is both safe and efficient.
Managing a warehouse is a complex task that requires paying attention to many aspects of daily activities. Keeping an eye on layout and infrastructure, implementing routine pallet rack inspections, keeping inventory in check, embracing automation, and offering training and development opportunities to your employees will increase your chances of keeping an efficient warehouse and save time!
References:
5 common warehouse management mistakes (2017)
The Most Common Warehouse Mistakes and How to Avoid Them
Supply Chain Rocks, The Most Common Warehouse Mistakes (2015)
2018 Warehouse/Distribution Center Equipment Survey: Automation & Robotics Lead Robust Outlook
15 Ways to Improve Warehouse Space Utilization (2020)
8 Tragically Common Mistakes in Warehouse Setup
(2020) Retrieved from https://www.infopluscommerce.com/blog/8-tragically-common-mistakes-in-warehouse-setup