So you realize your warehouse needs more storage and you decide to buy a racking system. Great idea, but don’t go rushing into it. Many factors should be considered when planning a new rack installation. Asking yourself the right questions will save you time, money and optimize overall productivity! Here are the top 5 focus points that will lead to the best decisions when choosing your future installation.
1-Why Do You Need the Rack?
Before acquiring a pallet rack, ask yourself why you need a new rack. Depending on the reasons, many different solutions will be available to you. For example, if your goal is to maximize storage, you should choose racks offering a greater storage density. If you need better product accessibility, you might consider racks that allow access to all your pallets, and if your motive is to optimize the warehouse space, then fewer aisles and higher density racks should be the solution. Every warehouse is different, and every warehouse has its own needs, problems, and solutions. Therefore, identifying your objective first will help you choose the product that is right for you.
2-What Types of Products Does Your Warehouse Store?
This aspect can easily go under the radar, but significantly influences the selected type of racks. From the different stocked goods to the services your warehouse offers -even the types of pallets you are using-, it is essential to know what goes in and out of your pallet rack systems. Is your warehouse storing small, light products? Is it storing solid or liquid goods? Are they frozen and require refrigeration?
Table 1: Types of Products on the Shelves
Solid | Liquid |
Big | Small |
Light | Heavy |
Frozen | Perishables |
Table 2: Types of Pallets on the Shelves
Irregular | Uniform |
Single-Use | Reusable |
It is important to ask yourself these questions as the rack’s structure can vary based on the answers. Liquid goods are less stable and will react more if there is an impact on the rack, causing the liquid to be displaced. Also, certain racks like drive-ins or pallet flow require reusable pallets. So, if your entire warehouse runs with single-use pallets, make sure you are willing to make the switch. Almost every warehouse will be storing commodities, and some will be a lot more active on the distribution, which implies higher forklift circulation and increased chances of damaging the racks. Some will also include machinery for wrapping or special product treatments that can affect the warehouse’s environment (heating and chemicals). Identifying all these conditions will make your planning easier and ensure you install the ideal rack for you.
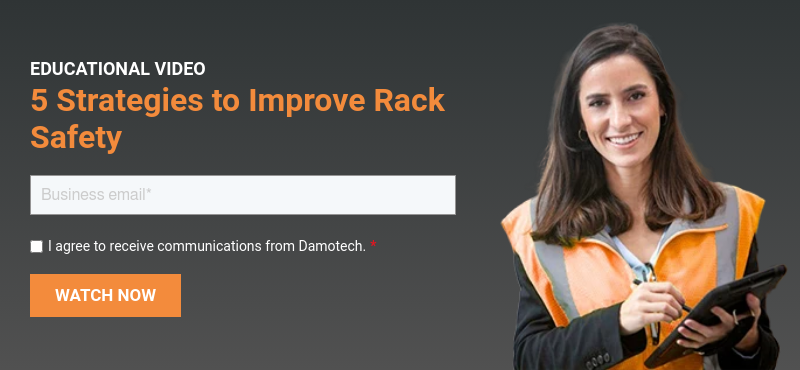
3-What Types of Rack Are Available?
There are seven main rack types to consider, and knowing which one is the most appropriate for your warehouse can be overwhelming. Ideally, your rack arrangement will support your warehouse productivity goals and will be adapted to your specific product types. Here is a list of all seven, with pros and cons that can help you better understand which should be part of your arsenal or not.
-
Selective Single-Deep Pallet Racks
Figure 1: Single-Deep SystemSelective Single-Deep is the iconic standard pallet rack. It is the best option for big warehouses where accessibility to the products and simple, low-cost solutions are focus points.
Pros:
- Good overall pallet accessibility
- Pallets can be accessed on both sides
- The less expensive rack in the business
- Easy installation
Cons:
- It takes up more space than other racking types
- While any pallet can be accessed, workers might have to travel long distances to get to the right product
-
Selective Double-Deep Pallet Racks
Figure 2: Double-Deep SystemThe Selective Double-Deep racks are very similar to the Single-Deep, but they’ll let you gain storage density by adding more depth to the system. However, when placed against a wall or back to back, you will lose pallet accessibility as the ones in the back row won’t be accessible anymore.
Pros:
- Good density, offering more storage space than Single-Deep racks
- Maximizes the number of pallets per aisle ratio
- Easy installation
- Low cost
Cons:
- If many rows are placed back to back, accessing the pallets becomes more challenging compared to Single-Deep racks, because the back row pallets will be hidden by the ones in the front
- Workers may have to travel long distances to get to the right product
- If the system is installed against a wall or back to back, it requires special forklift equipment with forward reachability to access the pallets at the back of the rack (Figure 3)
Figure 3: Special Forklift Requirements
-
Pushback Pallet Racks
Pushback racks are great for maximizing storage and space. They function by a Last In First Out (LIFO) procedure, which means the last pallet going in the bay will be the first one to come out. Therefore, it requires products that can be stored for long periods of time.
Figure 4: Pushback System
Pros:
- High inventory (2 to 6 pallets deep for the most common systems today, but could vary for custom projects)
- Dense and efficient storage
- Fast load/unload time
Cons:
- Cannot access every pallet
- More expensive than static racking
-
Drive-in Pallet Racks
Figure 5: Drive-in System
With Drive-In racks, what you gain in storage capacity, you lose in loading/unloading speed. They also function by a Last In First Out (LIFO) method, allowing products to be stored for long periods of time.
Pros:- Higher inventory than Pushback racks (2 to 10 pallets deep for the most common systems today, could vary for custom projects)
- Dense and efficient storage
- Makes static racking less expensive than it would be with Pushback racks
- Higher risks of rack damage due to forklifts having to drive inside the system
- Not every pallet can be accessed
- Slower load/unload process than Pushback racks
- Must follow the suitable loading/unloading sequence for safety
-
Pallet Flow Pallet Racks
Figure 6: Pallet Flow System
This type of rack is great for maximizing storage. It functions by First In First Out (FIFO) procedure, which means the first pallet going in the bay will be the first one to come out. Therefore, it can store both products that need to be sent quickly and products that last for a long period of time.
Pros:
- Highest inventory (2 to 20 pallets deep for the most common systems today, could vary for custom projects) more than Pushback and Drive-In
- Dense and efficient storage
- Faster load/unload than Drive-In racks
Cons:
- System is loaded and unloaded from different sides
- More forklift circulation, so higher risks of rack damage
- Can’t access every pallet
- More expensive than static racking
-
Carton Flow Pallet Racks
Figure 7: Carton Flow System
These racks are similar to Pallet Flow racks but are designed for small products. They function by First In First Out (FIFO) method, which means the first pallet going in the bay will be the first one to come out.
Pros:
- High inventory
- Dense and efficient storage
- Hand-operated rack, so lower risks of rack damage
Cons:
- Can only store small size loads
- Requires uniform merchandise in size and weight
- More expensive than static racking
-
ASRS (Automated Storage and Retrieval System)
Figure 8: ASRS System
This system is a high-tech solution, great for inventory with uniform size and weight and warehouses requiring special conditions that human workers cannot operate— dark rooms for film and photo storage, for example.
Pros:
- Automatic inventory control
- Reduced risk of rack damage due to the absence of human error
- Narrow aisles allow for more storage capacity
- High density
- Safer due to reduced forklift circulation
- Little to no labor is needed
Cons:
- The most expensive racking option, due to equipment and installation
- Long and complex installation time
- Specialized maintenance is required to prevent from failing
4-What are the Building’s Requirements?
Buildings have many different features that make a difference in a new rack installation. For example, the floor must be able to support all the loads imposed by the storage racks. Factors like slab thickness or heated flooring will make a difference in the total load the racking systems can support. If you do not have access to the data, an examination by a specialized engineering consultant may be required. Also, consider the floor area available before installing a rack. This will ensure :
- The respect of building clearances
- The planning of large enough aisles for forklift movement
- The safe loading of materials
Next, make sure that your racking configuration allows for the appropriate clearance from the ceiling to properly install the sprinkler systems. Finally, make sure the lifting equipment you are using is adapted to the dimensions of the new racks. High ceiling warehouses can accept taller pallet racks, but there is a chance your forklifts cannot reach the top level of these racks, especially if you have been running with shorter ones all along. In that case, new forklifts would need to be acquired, which can lead to unplanned expenses.
5-Where is My Warehouse Located?
The design of the pallet rack might be different if in a high seismic zone. Therefore, after you have selected your rack type, it is important to consider the geographic region in which the rack will be installed before setting them up.
![]() Figure 9: Seismic Zones in the US |
|
Above is a map of the seismic zones in the US. The pink regions like California and Hawaii are well known for their seismic activity, but keep in mind that the border between Tennessee, Arkansas, Kentucky, Missouri, and Illinois is also a high seismic zone. The same goes for South Carolina and Alaska. Therefore, pallet racks in these regions will be designed in such a way that they are able to sustain seismic activity.
Post-Installation
Once you have chosen and installed the best racking option to optimize operations safely in your warehouse, a few last factors will need to be addressed. When you acquire a new rack system, your rack manufacturer should provide the Load Application and Rack Configuration (LARC) drawings. Essentially, LARC drawings will tell you what the intended configuration of the rack is and the maximum load capacity given this configuration. So, once the storage shelving is installed and ready to go, it is the warehouse owner’s responsibility to ensure the employees, especially the forklift drivers, are aware of the maximum load the rack can support. The correct way to do so is to make the load capacity plaque visible and accessible by posting it on the rack system itself generally at the ends of the aisles. Second, make sure the rack configuration is the same as on the LARC drawings. This second part is important because it is common for warehouses to make some changes and managers will be tempted to modify certain rack configurations to better suit their needs over time. If this is the case and the rack configuration needs to be changed to a configuration that differs from the LARC drawings, make sure it is done with the approval of a certified rack engineer.
As you can see, there are many things to consider when planning a new rack installation. Luckily, Damotech’s certified rack engineers can guide you through the entire process. To talk to one of our rack safety experts, click here.
References:
Advantages And Disadvantages Of ASRS - news - News - Jracking (China) Storage System
Pushback Racking 101 | 3D Storage Systems Limited
Drive-In Pallet Racking - Toronto (flowrite.ca)
Seismic Design Considerations for Warehouse Pallet Racking Systems (apexwarehousesystems.com)
Videos - RMI Safety (rmiracksafety.org)
Inspection checklist V4 Damotech
industrialsteelstoragerack.pdf (safemanitoba.com)
Figures:
single deep racking - Bing images
double deep rack drawing - Bing images
pushback rack system drawing - Bing images
Drive in Rack Structure - Bing images
pallet flow Rack Structure drawing - Bing images