I. Why Modern Warehouses Must Transform
The Wake-Up Call: A Realistic Warehouse Tragedy
During peak holiday operations, four forklifts converged on Aisle 7, each operator focused on high-priority tasks. A warehouse manager, attempting to reroute one driver, entered the congested space on foot. Moments later, a forklift struck him. He fell, hitting his head on the concrete. Work stopped. An ambulance arrived.
This fictionalized scenario highlights a common reality: unsafe, inefficient warehouse environments often stem from disjointed logistics systems. The convergence of forklifts, each operating on separate urgent picks within a congested aisle, created the perilous conditions—not due to human error alone, but as a result of systemic logistics breakdown. These aren’t just isolated errors, but symptoms of broken workflows, inadequate visibility, and reactive management.
Addressing these systemic flaws through integrated logistics and intralogistics optimization can simultaneously elevate productivity and dramatically improve worker safety.
II. What Are Intralogistics and Integrated Logistics?
Definitions
- Intralogistics: The orchestration of materials, people, and information within the four walls of a warehouse.
- Integrated Logistics: The coordination of internal operations with external partners across the supply chain.
Why It Matters
Intralogistics is foundational. Integrated logistics expands that efficiency beyond the warehouse. Together, they:
- Reduce congestion
- Prevent operational errors
- Enable safer, faster decisions
Investing in sophisticated external connectivity without addressing internal inefficiencies and hazards is akin to constructing a high-performance engine but placing it in a vehicle with faulty brakes.
Table: Intralogistics vs. Integrated Logistics
Feature | Intralogistics | Integrated Logistics | Safety Synergy |
---|---|---|---|
Scope | Inside the warehouse | Entire supply chain | Less internal chaos from better external coordination |
Tech | WMS, AGVs, RFID | SCM, TMS, IoT | Internal tech feeds real-time safety data upstream |
Risk Reduction | Congestion, load errors | Supply delays, rushes | Stability improves decisions, reduces injury triggers |
III. Measurable Gains: Efficiency & Safety Wins
Case Studies
- Accel Logistics: +35% productivity with Blue Yonder WMS; reduced operating stress.
- Costa Logistics: 14% faster picking; 10% cost savings with Manhattan WMS.
- Quiksilver: $4M saved annually; doubled throughput with Korber WMS.
Root Benefits
- Optimized Movement: AGVs and routing algorithms prevent congestion.
- Faster Order Fulfillment: Lower cycle times, fewer manual tasks.
- Increased Accuracy: RFID/barcode precision prevents risky rework.
IV. Safety Gains with Smart Systems
Stats That Matter
- 4.7 injury cases per 100 FTEs in warehousing (NAICS 493)
- 1 in 6 workplace fatalities involve forklifts
- Forklifts responsible for ~90% of pallet rack damage
- 36% of forklift-related deaths are pedestrians
Risk Reduction via Technology
- Forklift Congestion: WMS route control & slow zones reduce collisions
- Blind Spots: RTLS + RFID give real-time proximity alerts
- Manual Handling: Automation reduces physical strain and fatigue errors
ROI-Driven Safety Tech
- Surveily AI: 62% fewer incidents, 1,498% increase in near-miss visibility
- RTLS: Real-time location tracking, heatmaps, dynamic geofencing
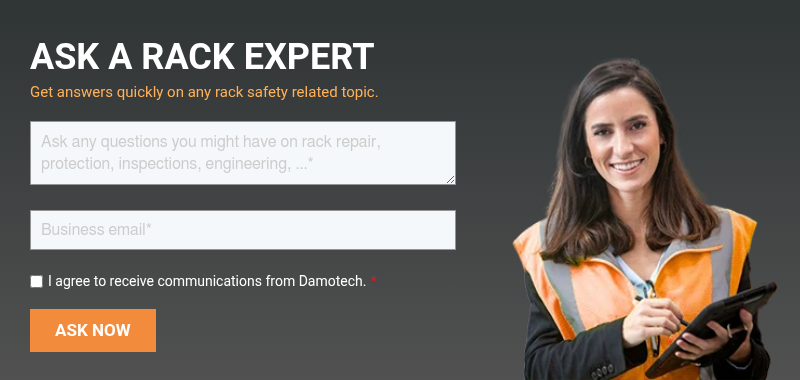
V. Tech Stack: The Safety Engine
The integration of AGVs and AMRs can alleviate congestion and minimize human error through automated routing.
Table: Logistics Tech & Safety Value
Tech | Core Function | Efficiency Gain | Safety Boost |
---|---|---|---|
WMS | Task optimization | Less travel, more accuracy | Prevents overload, improves layout |
SCM | Supply coordination | Better forecasting | Smoother flows reduce rushes |
RTLS | Real-time asset tracking | Workflow visibility | Collision avoidance, slow zones |
RFID | Inventory tracking | Accurate counts | Reduces risky search maneuvers |
AI | Predictive insights | Route & labor optimization | Flags unsafe acts in real time |
VI. Pallet Rack Safety: Logistics Can’t Ignore It
Leading Threats
- Impacts: 90% of damage stems from forklift collision
- Overloading: Exceeding capacity without oversight
- Improper Modifications: Unauthorized reconfiguration = collapse risk
Logistics Systems = Rack Safety Tools
- WMS Putaway Logic: Prevents overloading
- RTLS Alerts: Create slow zones in aisles
- RFID Accuracy: Ensures correct placement, fewer manual interventions
Physical Protection Still Critical
- Damotech Repair Kits: Restore integrity post-damage
- Load Plaques: Clarify limits to operators
- Guarding Solutions: Absorb collision force
An intelligent system, however advanced, cannot fully compensate for a structurally compromised pallet racking system.
Damotech’s engineered repairs restore the rack’s original load capacity and, in many cases, enhance its resilience against future impacts.
VII. Roadmap to Safer, Smarter Warehousing
- Assessment: Map bottlenecks and risks
- Foundations: Deploy WMS/SCM
- Tech Rollout: Add scanning, RTLS, AI
- Flow Optimization: Data-driven layout redesign
- Safety Integration: Alerts, geofencing, inspections
Key Tip: Don’t forget the human factor. Train, involve, and empower staff.
VIII. Final Word: Tech + Safety = Competitive Edge
The future of logistics belongs to operations that are:
- Productive
- Predictable
- Proactively Safe
No logistics strategy is complete without safe, load-bearing infrastructure. Damotech helps you build that foundation, ensuring your racks are resilient and compliant before layering on smart systems. Contact a Damotech expert today and discover how structural safety solutions can unlock the full potential of your smart logistics strategy.
Frequently Asked Questions
How do intralogistics and integrated logistics improve warehouse safety?
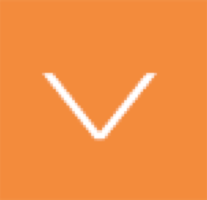
Intralogistics and integrated logistics enhance warehouse safety by streamlining workflows, reducing congestion, and improving visibility across operations. Intralogistics systems, like WMS and real-time tracking, optimize material flow and minimize manual handling risks. Integrated logistics extends this efficiency across the supply chain, helping prevent operational surges and last-minute chaos that often lead to accidents. Together, they create safer, more predictable environments for workers and equipment.
What is the difference between intralogistics and integrated logistics?
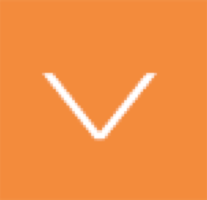
Intralogistics manages the flow of materials, information, and personnel within a warehouse, covering storage, picking, and internal transport. Integrated logistics connects these internal systems with external partners like suppliers, carriers, and customers. The former optimizes in-house efficiency and safety, while the latter ensures end-to-end coordination across the entire supply chain.
How does WMS improve forklift safety?
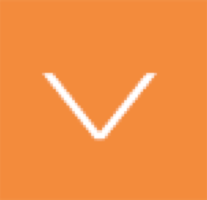
A Warehouse Management System (WMS) enhances forklift safety by directing travel paths, managing task assignments, and reducing unnecessary movement. It prevents aisle congestion, minimizes cross-traffic, and ensures accurate load placement, which reduces collision risks. Some systems even integrate with real-time location tracking to create dynamic slow zones or proximity alerts.
What are the common causes of pallet rack failure?
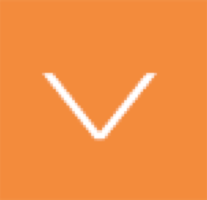
- Forklift impacts (up to 90% of incidents)
- Overloading or exceeding rated capacities
- Improper loading and uneven weight distribution
- Unauthorized modifications to racking structures
- Wear, corrosion, or neglected maintenance
Damotech’s engineered repair kits, inspections, and load capacity calculations are designed to address and prevent these risks proactively.