The 4 different stages of rust on your warehouse pallet racks and how to prevent it
Steel is a largely used material in many different industries including tooling, building, automotive, and racking. We know steel can be very strong, but it has its weaknesses. One of them is known as corrosion or rust. Pallet racks typically rust when they are exposed to moisture in the air for an extended period. Chemicals can also be a cause of rust. For example, a leaking battery in a charging station for forklifts can accelerate the rusting of pallet racks as well as chemical fertilizers and salts.
The best way to deal with corrosion in your warehouse is being aware of the most efficient ways to prevent it from happening and understanding the 4 stages of rust. Keep reading to learn more!
Corrosion Prevention Methods
The most common methods to prevent steel from rusting include paint coatings, hot-dip galvanizing, and thermal spraying.
Paint coating of steel components is a sequential application that usually consists of applying a primer to the steel with intermediate coats, and a finish coating to finalize the process. Each coating layer has a specific function, and the method used to apply it has significant effects on the quality and durability of the coating. Standard methods of applying paint to steel include brush, roller, conventional air spray, and airless spray/electrostatic airless spray [1].
Hot-dip galvanization of steel is a process where the component is immersed in a bath of molten zinc at about 450°C. The steel is uniformly coated with zinc alloy and layers then form a metallurgical bond with the steel. The zinc coating is durable, tough, abrasion-resistant, and provides cathodic protection to small areas where the underlying steel is exposed to any factors that might cause corrosion [1].
For more information on corrosion, read our Metal of Honor blog post.
Thermally sprayed coatings of either zinc, aluminum, or zinc-aluminum alloys provide long-lasting protection against corrosion for steel components exposed to aggressive environments. The metal coating is initially in powder or wire form and is fed through a spray gun containing a heat source. The molten metal is blown onto the steel structure by a compressed air jet. After solidifying, the coating overlaps the steel and is porous. It is then sealed by applying a thin organic coating that penetrates the surface of the metal coat [1].
It is always best to prevent rust rather than having to address the issue, but sometimes even when prevented, corrosion of steel pallet racks can occur. When addressing the issue of corrosion, you might ask yourself:
How severely does the rust affect the load capacity of my racks, and should I replace the rusted component?
Being familiar with the 4 stages of rust will help you understand the situation and prioritize repair according to the severity of the situation.
The 4 Stages of Rust
The 2 most common methods of corrosion prevention in pallet racks are paint coatings and galvanization. In comparison, a galvanized coating of a steel component can survive 100 years if exposed to the right environment and designed in accordance, while a painted component exposed to the same conditions would need to have its coating renewed 3 times to last just as long [3]. Depending on whether your racks are galvanized or not, they will react differently during the rusting process. Therefore, we will be looking at the 4 stages of the rusting process for galvanized and painted racking components and assess their respective priority levels.
Stage 1: Small Patches of Rust (Low Priority)
When the rusting process has begun on a painted component, small patches of brown surface rust can be observed, as illustrated in the picture below. You might think this is problematic, but the reality is that surface rust is only an aesthetic issue and does not affect the strength of your rack [5].
While non-galvanized components will have a brown discoloration during the initial phase of rusting, galvanized components will have a white discoloration, as shown below. This is due to the added layer of zinc on the galvanized component. During this stage, the discoloration is usually small, light, and scattered on the racking component. Just like the painted components, this is only an aesthetic issue as the underlying steel material has not been compromised yet.
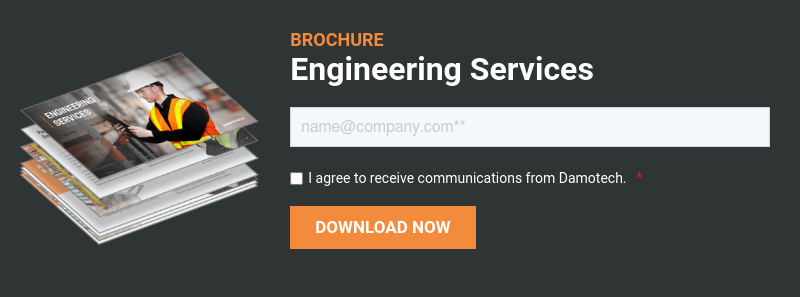
Stage 2: Medium Patches of Rust (Moderate Priority)
The second stage of the rusting process is when the steel starts losing some of its strength. For painted components, a brown discoloration can be observed just like in the initial stage but is also accompanied by etching or pitting of the surface metal [5]. If the steel has lost 10% or more of its original thickness, you should start thinking about replacing the component.
Unlike the painted components where a brownish discoloration appears during all stages, the galvanized components only start showing signs of such discoloration at the second stage of the process. Although the brown discoloration is at its initial stage here, the white discoloration has spread to cover a larger area of the racking component while having a powder-like appearance. Just like the non-galvanized components, if the galvanized part has lost 10% of its thickness, it should usually be replaced.
Stage 3: Large Patches of Rust (High Priority)
For painted components, at the third stage, the brown discoloration has spread and covers most of the components with severe etching and pitting as shown in the image below. The rust has penetrated the steel of the component and has probably severely reduced its load capacity. If you see this stage on any of your racks, the issue should be addressed as soon as possible by replacing the component.
Just like the second stage of corrosion, the galvanized component will show signs of white discoloration but with a larger dark rusted area. As mentioned earlier for the non-galvanized parts, the rust has penetrated and started eating away at the base material. The area with the brown discoloration represents a weak point on the component and has probably lessened its load capacity. It should be replaced without delay.
Stage 4: Deterioration of the Steel (Unload Priority)
Whether your rack is galvanized or not, this is the stage that you never want to get to. At this stage, the corrosion has eaten away so much of the steel that holes have been created in the component. If the rusted component is a beam, the affected cell and potentially additional components should be unloaded at this point, and if it is an upright, the two adjacent bays should be unloaded. If any component reaches this stage of corrosion, it should be replaced immediately.
Special assessment
A large, penetrated area is a weak point on a component but what if the affected area is small, yet located in a key spot on the component? For example, at the column base or a welded joint. These key areas are often bearing most, if not all, of the load applied to the rack and/or component. Therefore, assessment of corroded racking components should be done on a case-by-case basis. For more insights on the priority levels, read our blog What to Know About Rack Damage Priority and Classification [4].
Takeaways
As we all know, rust does not happen instantaneously, it is an ongoing process that evolves over time. The general guideline is if the racking component has lost 10% of its original thickness, it should be repaired or replaced, but special care should be taken when assessing rust located on one of the component’s key areas. Nevertheless, the cause of the rust should be determined to prevent further corrosion of the existing component or the new replacement part. Routine inspections should be conducted so rusted components can be replaced before they begin to lose their structural capacity. If you have any doubts about the structural integrity of your racks, contact our rack experts.
References
[1] "Steel Contruction Info," [Online]. Available: https://www.steelconstruction.info/Corrosion_protection. [Accessed 04 11 2021].
[2] N. Wathier, "Metal of Honor - Preventing Rust And Corrosion To Your Pallet Racks," Damotech, 15 May 2019. [Online]. Available: https://www.damotech.com/blog/metal-of-honor-preventing-rust-and-corrosion-to-pallet-racks. [Accessed 6 October 2021].
[3] "Hot-Dip Galvanized vs Powder Coat or Paint," Piping Technology & Product, Inc., [Online]. [Accessed 04 11 2021]. Available: www.pipingtech.com
[4] Damotech, "What to Know About Rack Damage Priority and Classification," Damotech, 3 August 2020. [Online]. Available: https://www.damotech.com/blog/what-to-know-about-rack-damage-priority-and-classification. [Accessed 26 October 2021].
[5] A. Post, "Is used Pallet Racking Safe?," Arker Warehouse, 10 October 2018. [Online]. Available: https://arkerwarehouse.com/used-pallet-racking-safety/. [Accessed 8 October 2021].
[6] "Rust Bullet," [Online]. Available: https://www.rustbullet.com.au/technical/how-it-works/corrosion-stagesscale/. [Accessed 21 October 2021].
[7] Conger, 30 07 2021. [Online]. Available: https://www.conger.com/warehouse-racking-guide/. [Accessed 04 11 2021].
- Top 100 Warehouse Safety Quotes for Toolbox Talks, Posters & Meetings
- Top 12 Largest Warehouses in North America (Size, Tech & Safety)
- Costco’s Supply Chain Strategy: Decoding Its Warehousing Approach
- Minimum Distances Between Pallets, Rack Systems & Building Structures
- IKEA Warehouses: Efficient Warehousing and Distribution Strategies