Freezer warehouses are among the most demanding environments in the supply chain. These ultra-low-temperature facilities are essential for preserving frozen foods, pharmaceuticals, and other temperature-sensitive goods.
But maintaining safety in these sub-zero conditions requires more than cold air—it demands rugged freezer racks, specialized PPE, and strict engineering standards. This article explores how freezer warehousing works, what makes it uniquely risky, and how Damotech helps keep your racks and workers safe.
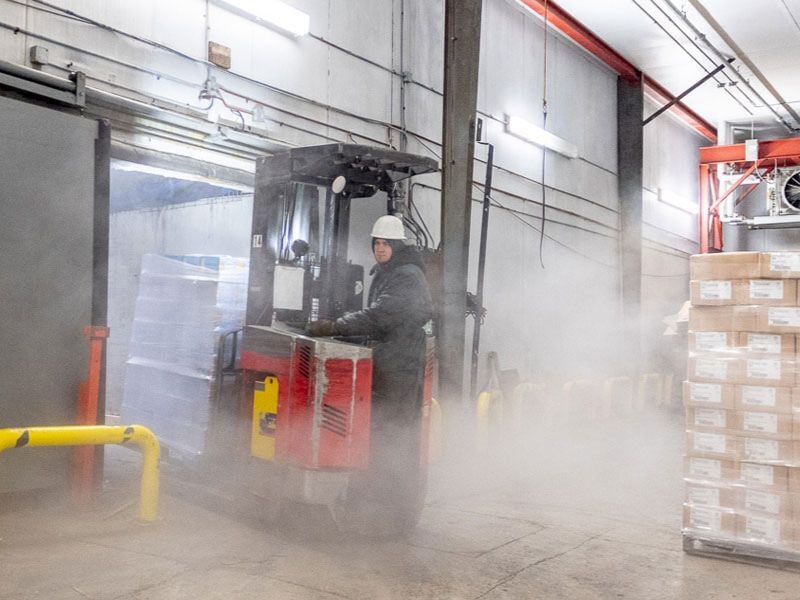
A forklift driver navigates a sub-zero loading zone in a freezer warehouse, where condensation and frost pose daily visibility and safety challenges. Photo Credit: Minnesota Freezer Warehouse Company
Jump to Section▼
- What Is a Freezer Warehouse?
- Cold Storage vs. Freezer Warehouses
- How Freezer Warehousing Works
- Freezer Safety Rules & PPE
- Freezer Warehouse: Material & Risks
- Freezer Rack Damage Risks
- Damotech’s Role in Protection
- Best Practices for Freezer Safety
- FAQ Section
What Is a Freezer Warehouse?
A freezer warehouse is a temperature-controlled facility typically kept between -10°F and -40°F to store perishable goods like frozen foods, pharmaceuticals, and biotech materials. These warehouses are a critical component of the cold chain, ensuring product safety and longevity.
Cold Storage vs. Freezer Warehouses: What’s the Difference?
Type of Facility | Temperature Range | Primary Use |
---|---|---|
Ambient Storage | 50°F to 70°F | Dry goods, packaging materials |
Refrigerated (Coolers) | 34°F to 50°F | Produce, dairy, some beverages |
Freezer Warehouses | 0°F to -13°F | Frozen meat, seafood, medicine |
Freezer warehouses operate under far more extreme conditions and require specialized infrastructure, safety measures, and equipment to ensure operational integrity.
How Freezer Warehousing Works
These warehouses use large-scale industrial refrigeration systems, combining evaporators, compressors, and condensers. The objective is to extract heat and maintain precise temperature control. Freezer zones also demand high insulation performance, airlocks, and moisture control systems to avoid frost heave and rack deterioration.
- Thermal cycling degrades floor slabs, causing frost heave.
- Moisture control becomes critical to avoid ice buildup on racks.
- Anchor points and expansion joints must accommodate contraction at sub-zero temperatures.
Working in Sub-Zero Temperatures: Freezer Safety Rules & PPE
Freezer environments create serious risks for warehouse personnel:
- Decreased dexterity and reaction time
- Slips and falls on icy surfaces
- Hypothermia and frostbite from prolonged exposure
What Are the Side Effects of Working in a Freezer Warehouse?
- Numbness or reduced grip
- Joint stiffness or pain from cold exposure
- Dehydration due to dry, cold air
- Long-term circulation problems if exposure is not managed properly
Employers must offer ergonomic assessments and regularly inspect warehouse environments for risks.
Recommended Freezer PPE
- Thermal insulated gloves (freezer-rated)
- Anti-slip insulated boots
- Moisture-wicking base layers
- Balaclavas and insulated hoods
- Fleece-lined or insulated jackets
- Layered clothing (breathable + thermal barrier)
- PPE-compatible radios for low-visibility zones
While there’s no dedicated OSHA standard specifically for freezer PPE, employers are still obligated under the General Duty Clause [Section 5(a)(1) of the OSH Act of 1970] to maintain a workplace free of known hazards. Since cold stress is a recognized occupational risk, it falls under this duty of care.
According to OSHA and NIOSH, cold stress is a leading cause of workplace injury in freezer warehouses, especially during seasonal peak periods.
Freezer Warehouse: Material & Risks
Cold temperatures amplify stress on racking components. Common vulnerabilities include:
- Material embrittlement – Low temperatures can make standard steel brittle.
- Condensation corrosion – Moisture freeze-thaw cycles degrade anchor points.
- Substandard components – Wood shims, uncoated bolts, and rust-prone anchors should be avoided.
Ideal Design Features
- Galvanized or powder-coated racking
- Closed tubular construction
- Load-bearing elements engineered for contraction tolerance
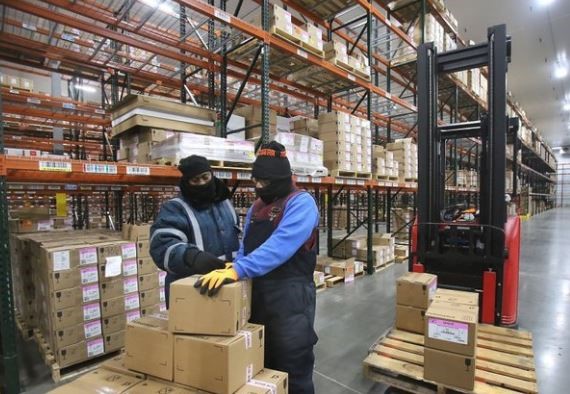
Warehouse employees in full cold-weather gear organize inventory in a freezer facility, where PPE and safe handling procedures are essential for worker protection and efficiency. Photo Credit: Abel Womack
Freezer Racks: Damage Risks in Frozen Facilities
Freezer warehouses increase rack damage frequency due to:
- Moisture freeze-thaw cycles
- Forklift collisions on icy surfaces
- Anchor loosening from slab contraction
Additionally, operating forklifts in tight, icy aisles increases impact risks. Common issues:
- Upright dents and deflection from glancing collisions
- Loose or sheared bracing due to vibration and freeze-thaw expansion
- Anchor pull-out caused by sub-slab frost heave
Damotech helps mitigate these risks by reinforcing freezer rack stability and providing engineering inspections.
Damotech’s Role in Freezer Rack Repair & Protection
We help freezer warehouse operators:
- Inspect all racks for compliance
- Reinforce weak points with DAMO PRO kits
- Install guarding (e.g., DAMO GUARD)
- Centralize inspection records via Damotech software
Best Practices for Freezer Warehousing Safety
- Conduct monthly inspections (weekly during peak seasons)
- Rotate staff shifts to reduce exposure
- Equip all workers with certified cold-rated PPE
- Use Damotech software to monitor rack conditions and load integrity
- Provide heated rest areas and anti-slip flooring
- Train employees on warehouse safety
- Flag any rack visibly compromised by frost or impact
- Get engineer approval before changing beam levels
Conclusion: Freezer Warehouse Safety Starts with Your Racks
Freezer warehouses are unforgiving environments. Safety begins at the structural level. Damotech helps warehouse operators reduce risk, cut costs, and ensure compliance through proven engineering, software, and rack protection products.
FAQ Section
What is a freezer warehouse?
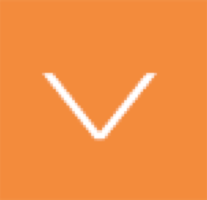
What are the biggest safety hazards in freezer warehouses?
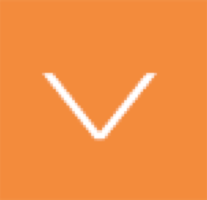
What kind of steel racking should be used in freezer warehouses?
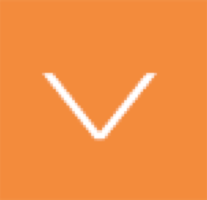
How often should freezer racks be inspected?
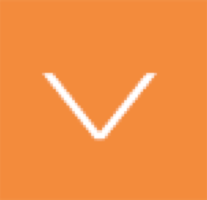
What is the best racking system for freezer warehouses?
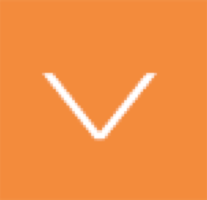
Why are freezer warehouse aisles wider than standard?
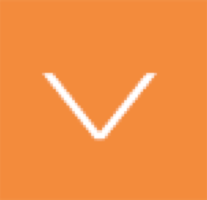
Operators need wider aisles (10–12 ft) to account for limited visibility caused by bulky cold-weather PPE.
How can you protect racking systems in freezer warehouses from impact damage?
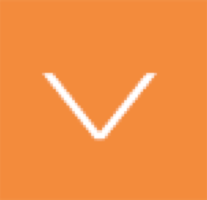