In warehouse management, rack safety often goes unnoticed in budget discussions. But what if we told you that overlooking this vital aspect could lead to significant problems?
Join us as we explore the 8 common reasons rack safety might not always receive the attention and funding it deserves and make a compelling case for why it deserves a top spot on your priority list.
Rack Safety: The Hidden Priority
We all know that the importance of rack safety cannot be overstated. However, when allocating funds, it’s not uncommon to overlook it for various reasons. But here’s the catch—neglecting it can lead to unforeseen risks and consequences.
Rack safety should never be treated as an optional extra. Prioritizing it goes beyond compliance; it represents an investment in the well-being of your employees, operational efficiency, financial savings, and the long-term success of your warehouse operations.
Let’s explore why rack safety may be omitted from budget considerations and our compelling responses.
REASON 1: The racking is still standing and appears intact.
“Why should we allocate resources to rack safety when our racking hasn’t failed us yet? It seems to be holding up just fine, and there haven’t been any accidents. Everything is running smoothly, and our funds could be better utilized elsewhere.”
The absence of accidents doesn’t mean your racking system is without risks. Often, problems in the racking may not be immediately visible or may develop gradually over time, making them difficult to detect until it’s too late.
By proactively investing in rack safety measures now, you can identify and address potential issues before they escalate into major problems, thus preventing accidents and their associated costs, disruptions, and liability.
Focusing solely on the fact that the racking is still standing overlooks the larger impact on your operations. A robust rack safety program not only mitigates risks but also enhances operational efficiency. By allocating funds to rack safety, you can reduce the likelihood of damage to both your products and the racking itself. This, in turn, minimizes downtime, decreases maintenance costs, and contributes to improved warehouse productivity.
Also, even though your racking has not experienced any catastrophic failures or accidents yet, you need to consider the broader perspective of rack safety. Investing in rack safety is not just about preventing accidents; it’s about safeguarding your employees, ensuring the long-term sustainability of your operations, and optimizing efficiency.
Allocating funds to this crucial aspect of warehouse management is an investment in your future success. This commitment fosters employee morale and loyalty, positively influencing their productivity and engagement, and demonstrates your commitment to safety and excellence.
REASON 2: Improvement of operations.
“I understand rack safety is essential, but other areas need attention to boost productivity and efficiency. Will allocating funds for rack safety significantly improve our overall warehouse operations?”
Rack safety isn’t just about your racking. While the concern about allocating funds for rack safety and its impact on overall warehouse operations is understandable, it’s essential to consider that rack safety improvements can have a more significant influence than might initially appear.
Risk mitigation: Investing in rack safety reduces the risk of accidents and damage to your inventory and equipment. This, in turn, minimizes potential downtime caused by accidents or equipment failures, directly contributing to improving operational efficiency.
Employee productivity: Employees who feel safe and valued are more likely to be engaged and efficient in their roles, positively impacting overall operations.
Operational streamlining: A well-maintained rack system can streamline your warehouse operations. It ensures efficient storage and retrieval, reducing the time and effort required for daily tasks. Over time, this efficiency can lead to increased productivity.
Compliance and reputation: Complying with safety standards and regulations, such as those defined by OSHA, ANSI, and RMI, not only helps you avoid fines but also enhances your reputation as a responsible and safety-conscious organization. This can be a competitive advantage in attracting customers and business partners.
REASON 3: Timing and budget constraints.
“Our budget is fixed and allocated for immediate concerns like forklift maintenance and dock doors, which directly impact daily operations. Now might not be the right time to invest in rack safety; we must prioritize within our financial limitations.”
While it’s essential to adhere to your budget constraints and to prioritize concerns that directly impact daily operations, it’s important to consider the long-term implications of not investing right away in rack safety.
- Unforeseen incidents, such as rack failures or accidents, can lead to costly equipment damage, inventory losses, and even potential injuries to your employees.
- Your warehouse assets, including the racks, represent a significant investment. Protecting and maintaining these assets through a comprehensive rack safety program contributes to their longevity and ensures that you maximize the returns on your initial investment.
- Rather than fearing disruption to your local budget, consider it an opportunity for transparent communication with headquarters. By clearly outlining the necessity for rack safety improvements and highlighting their long-term benefits, you can collaborate to find a solution that aligns with your budgetary constraints.
Budget constraints are real, but it’s essential to recognize the cost-effectiveness of preventive measures compared to the potential financial setbacks and operational disruptions incurred in the event of a safety incident. Perhaps you can explore phased investments or alternative funding solutions to ensure that you address this critical aspect of warehouse safety without compromising your financial stability.
REASON 4: Fear of uncovering problems.
“I’m concerned that if we invest in a comprehensive inspection for rack safety, we might discover more problems than we’re prepared for. It could lead to unexpected expenses we’re not ready to tackle.”
The concern about potentially discovering unexpected issues during a rack safety inspection is understandable. However, identifying potential issues through an inspection allows you to address them proactively. Doing so can prevent these problems from escalating into more significant, costlier issues in the future. Remember, rack issues are not a matter of “if” but a matter of “when.”
Prioritizing safety is also a moral obligation to your employees. Ensuring their well-being should always be a top priority.
A rack safety inspection can be the foundation for building a long-term improvement roadmap that effectively tackles immediate concerns, helping you manage them efficiently and reinforcing your commitment to a secure and productive workplace. With the help of rack safety experts, you can develop a clear plan and establish priorities for the most critical safety enhancements that align with your budgetary limitations.
REASON 5: Perception of no problem.
“We haven’t received any complaints or reports of incidents regarding rack safety. Since there has been no indication that our warehouse might be in poor condition, rack safety hasn’t been on our radar.”
It’s encouraging that you haven’t received any complaints or reports of incidents related to rack safety, but remember that a lack of documented issues doesn’t necessarily indicate an absence of problems. Rack safety concerns may not always be immediately apparent, and waiting for incidents to occur before acting could lead to more significant risks and potentially costly consequences (such as financial losses, legal liabilities, and reputational damage).
Consider that many rack-related accidents go unreported or unnoticed until they evolve into significant incidents. You should address rack safety to prevent potential hazards before they worsen.
Moreover, maintaining a high standard of rack safety can lead to numerous benefits beyond just avoiding accidents. It can contribute to cost savings by reducing damage to products and racks, minimizing downtime, and extending the lifespan of our warehouse infrastructure.
REASON 6: Low priority on safety agenda.
“While safety is crucial, we have other pressing corporate priorities. Rack safety might have to take a backseat to measures like personal protective equipment (PPE), ergonomics, and equipment operation safety.”
Although your current corporate priorities are important, here’s why rack safety should not take a lower priority compared to other safety measures:
Preventive approach: Rack safety isn’t just about reacting to immediate issues; it’s a proactive step to prevent potential incidents leading to costly damage, inventory loss, and operational disruptions that you could have avoided.
Long-term cost savings: Investing in rack safety can yield substantial cost savings over time. Preventing rack damage and addressing potential hazards can reduce maintenance costs.
Regulatory compliance: Ignoring rack safety can put you at odds with regulatory authorities, potentially leading to expensive fines or legal issues.
Safety culture: A comprehensive safety culture encompasses all facets of workplace safety, including rack safety. It sends a powerful message that you are devoted to safety at every level, benefiting your employees and the company.
Enhanced reputation: A commitment to safety, including rack safety, enhances your reputation within your organization and the industry. It can make you more appealing to partners, customers, and potential employees who value a safe and responsible work environment.
REASON 7: Unawareness of imminent risks.
“I don’t know where to start. It might be easier to postpone until I have a clear plan, direction, or support.”
Your concerns regarding the need for a clearly outlined plan are valid. Given the complexities of warehouse systems and the continuous evolution of local standards and guidelines, it’s understandable not to be fully aware of the immediate risks associated with industrial racks.
For instance, did you know that even one slight change in your existing pallet rack system can significantly alter its strength and structural integrity? This underscores the importance of consulting with a qualified racking expert beforehand.
Your company’s growth and success depend on long-term planning. It’s prudent to be prepared for potential risks and disruptions by ensuring the integrity of your warehouse infrastructure.
Prioritizing rack safety allows you to proactively identify and address potential hazards before they escalate into accidents, safeguarding your employees and your company’s reputation and finances.
Failing to meet safety standards, even if you’ve been fortunate so far, could put you at odds with regulatory authorities in the event of an incident. Investing in rack safety demonstrates your commitment to compliance and reduces these potential legal risks.
REASON 8: Temporary in-house solutions.
“Considering the poor condition of our racking, it’s likely that we’ll need to replace it eventually, necessitating operational shutdowns. In the meantime, as a temporary solution, we rely on a local welder to address our repair needs or our maintenance team to manage the situation.”
While welding on existing racks may initially appear as a quick and cost-effective means of repairing a damaged racking system, you must consider the associated risk factors before proceeding with this option.
Fire hazard: Even when diligently following recommended fire safety procedures, welding generates sparks that may land in unfortunate locations, including on products, flammable materials, or pallets, potentially posing a fire hazard.
Weld contamination: It occurs when the surfaces to be welded are not adequately prepared, leading to weakened welds or hydrogen embrittlement, which can ultimately fail.
Temperature control: Careful temperature control is crucial during the welding process to adhere to American Welding Society (AWS) standards. Welding in freezer environments is generally discouraged due to the challenges it presents.
Supervision and certification: An engineer must provide a qualified procedure for field welding, and the welder must hold accreditation from AWS. The welder must demonstrate proof of certification and possess the necessary skills to execute the repair precisely as the supervising engineer specifies.
Due to the difficulty of testing the welded result and guaranteeing a level of resistance equivalent to that of the original component, there are strong recommendations against field welding on existing pallet racking in warehouse settings. If it is necessary to use this method, consult with an engineer experienced in racking systems and ensure strict adherence to all relevant codes and regulations before proceeding with the welded repair.
To avoid field welding, certified bolt-on repair solutions are available that eliminate the need for welding or dismantling of the racking system.
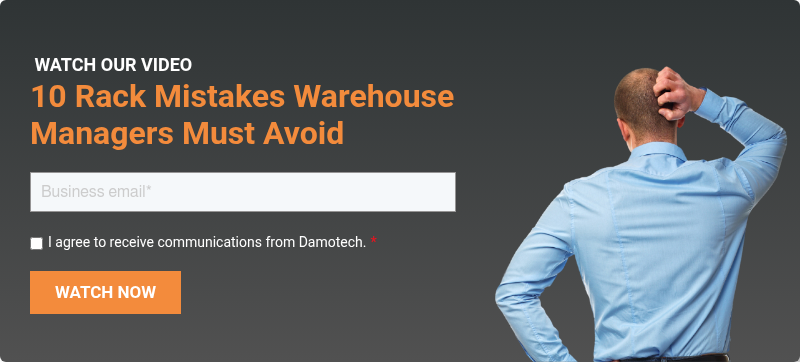
The Benefits of Choosing Rack Repair Over Replacement
A common reaction might be to reach out to the original equipment manufacturer and order a new upright. However, did you know that rack repair offers several advantages? Damotech’s engineered solutions are designed to replicate the original configuration of uprights, fully restoring the racking system’s original load-bearing capacity.
What’s more, opting to replace a damaged rack component with a new upright runs the risk of it being hit again, whether by forklift impact or moving pallets. A newly installed rack is just as vulnerable and unprotected as the previous one, requiring you to order additional protective units to prevent recurring damage in the exact location. But with DAMO PRO, your pallet rack uprights undergo permanent repairs and receive durable protection. It is so resilient that a lifetime warranty backs it against impact damage.
There are compelling reasons to consider investing in engineered rack repair solutions now rather than waiting to replace a rack, including:
Safety as a priority: Always prioritize the well-being of your employees. Address rack safety concerns promptly to reduce the risk of accidents and injuries, creating a safer working environment.
Uninterrupted operations: Waiting for a complete replacement could lead to unexpected rack failures that result in operational downtime.
Cost efficiency: Repairing or enhancing your existing racking may be more cost-effective than a complete replacement, especially when factoring in the potential costs associated with operational downtime and the purchase of entirely new racking systems.
Rack safety is critical to the overall success of your warehouse operations
In conclusion, the importance of rack safety cannot be underestimated. It’s a crucial aspect of warehouse management that should never be relegated to the sidelines during budget discussions. Prioritizing rack safety is not just about compliance; it’s an investment in the welfare of your employees, the efficiency of your operations, financial stability, and the long-term success of your warehouse. Feel free to incorporate any of the presented information into your budget planning presentations.
Consider working with a rack safety expert to address the hidden risks of overlooking rack safety. These specialists understand the nuances of rack systems, ensuring that your facility remains safe and optimized. By taking proactive steps and prioritizing rack safety, you can safeguard your employees and business, providing a secure and prosperous future for your warehouse operations.