Near Misses in Warehouses Are a Hidden Safety Risk
Most warehouses proudly display signs that read: “X Days Since the Last Accident.” While this may seem reassuring, it’s not the full story. Minor accidents and near misses happen daily, and if left unreported, they can lead to serious consequences.
“Zero accidents” doesn’t mean zero risk.
- A forklift nearly tips over but is caught just in time.
- A worker narrowly avoids a falling box.
- An overloaded rack bends but doesn’t collapse.
These near misses, or “lucky breaks,” are critical warning signs. The Heinrich Accident Triangle tells us that for every serious injury, there are 29 minor ones and 300 near misses (Heinrich, 1931). Tackling small incidents early can drastically reduce the chance of a major accident.
Why Near-Miss Reporting Is Critical for Warehouse Managers
While Damotech’s Rack Safety Flywheel provides a practical system for managing rack safety, the Heinrich Pyramid explains why near-miss reporting and culture change are foundational. This article complements the Flywheel model by spotlighting the human and behavioral side of safety.
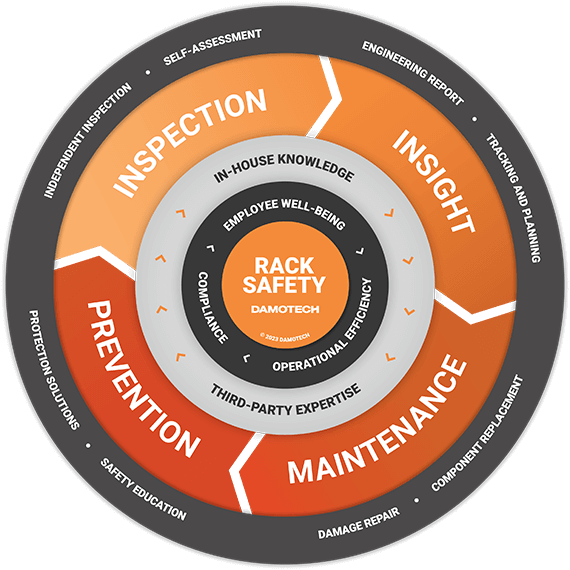
Warehouse Safety Leadership: The Key to Performance & Culture
At Damotech, we help warehouses operate at peak performance by focusing on what matters most: safety and efficiency. Our expertise lies in rack repair, protection, and engineering, but we also know that strong safety leadership drives long-term results.
This article is part of our management-focused series that delivers proven strategies for creating safer, more productive warehouse teams.
For a complete toolkit, explore Damotech’s Safety Resources.
What Is the Heinrich Accident Theory?
In the 1930s, safety pioneer Herbert William Heinrich reviewed 75,000 accident reports. He discovered a recurring pattern: serious accidents are often preceded by a chain of smaller, ignored incidents.
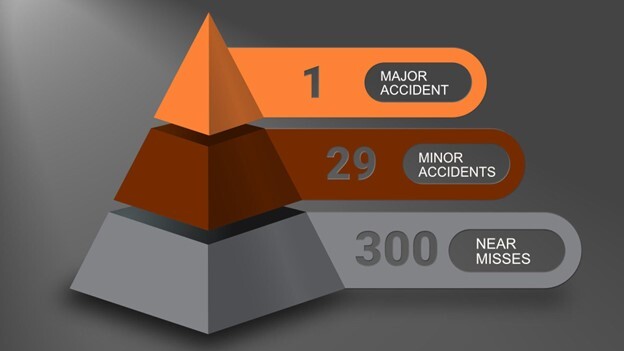
How does the Heinrich accident triangle work?
- 1 serious injury
- 29 minor injuries
- 300 near misses
The takeaway? Shrinking the base of the triangle (those near misses) reduces the odds of major incidents.
Supporting Research: Modern studies (e.g., NIOSH, 2018) support the idea that unchecked workplace hazards build up over time and can trigger serious consequences. While critics argue that not all minor incidents lead to major accidents, warehouses that track them tend to experience fewer serious injuries overall.
The Heinrich Pyramid, Updated: More Layers of Prevention
Heinrich’s triangle has evolved. Today, many versions include 4+ layers:
- Unsafe Acts or Conditions
- Near Misses
- Minor Injuries
- Serious Injuries
- Major Accidents
This reflects a broader understanding of how systems fail. OSHA, ANSI, and CSA standards all emphasize hazard identification and proactive correction before injuries happen.
Wondering where your warehouse stands in terms of rack safety? Take our short quiz to find out!
Benefits of a Safety Culture in Warehousing
How Warehouse Safety Improves Employee Retention
- Workers who feel safe and valued are more engaged and more likely to stay.
- Psychological safety improves communication and morale.
Warehouse Safety ROI: Operational & Cost Savings
- More uptime, fewer disruptions.
- Reduced medical expenses, insurance premiums, and litigation risks.
Compliance, Branding & Audits in Warehouse Safety
- Agencies (like OSHA, WorkSafeBC, etc.) consider near-miss tracking a best practice.
- A strong safety culture supports audits and builds employer brand equity.
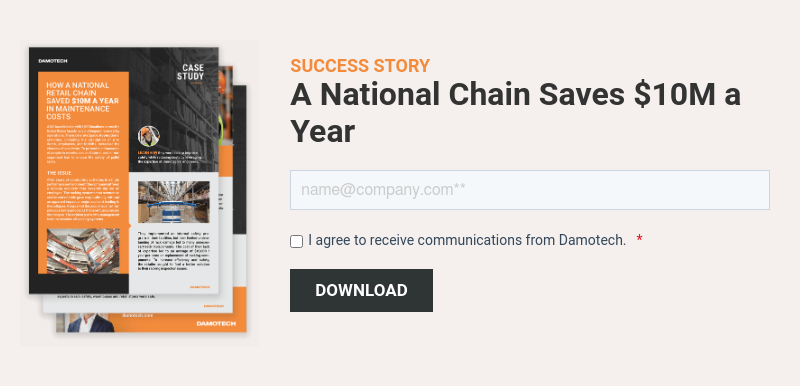
Real-World Applications of the Heinrich Triangle
Amazon: Implemented near-miss reporting across 1,100+ facilities and AI to detect high-risk areas.
Walmart: Uses wearable tech to monitor ergonomic safety.
UPS: Requires anonymous near-miss reporting.
How to Promote Near-Miss Reporting in Warehouses
Common Barriers to Reporting Near Misses in Warehouses
- Fear of blame
- Belief that “it wasn’t serious enough”
- Not wanting to waste management’s time
Warehouse Manager Tactics to Encourage Reporting
- Make it Easy: Use mobile apps, QR codes, and voice-activated systems. Allow anonymous reports.
- Reframe the Message: Treat reports as data, not failures.
- Reward Participation: Celebrate proactive reporting.
- Close the Loop: Show how reports led to action.
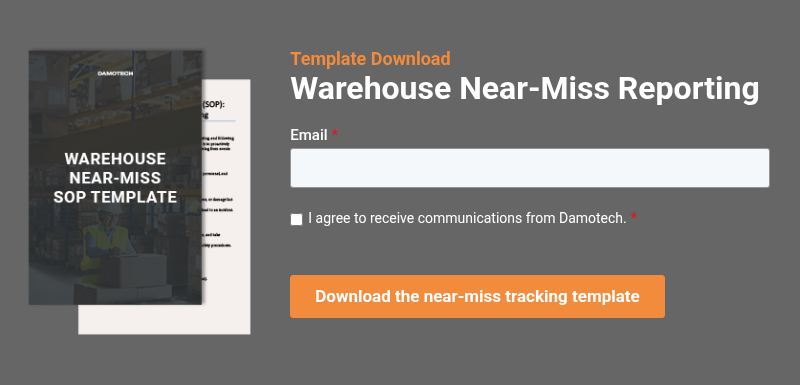
Overcoming Barriers to Building a Safety-First Warehouse
Changing Warehouse Culture Around Near Misses
Educate that “no injury” doesn’t mean "no risk.”
How to Justify and Fund Warehouse Safety Programs
- Reframe safety as a cost-reducer.
- Look for safety grants and incentives.
Conclusion: Building a Near-Miss Driven Warehouse Safety Program
A safe warehouse isn’t defined by how many days it’s been since the last injury—it’s defined by how actively it tracks and addresses the risks that haven’t become accidents yet.
Key Results from a Safety-First Culture:
- 60% more near-miss reports
- 45% fewer minor injuries
- Higher employee trust in safety systems
Safety isn’t a slogan. It’s a strategy.
Next step? Discover the Rack Safety Flywheel to start building a stronger culture today.
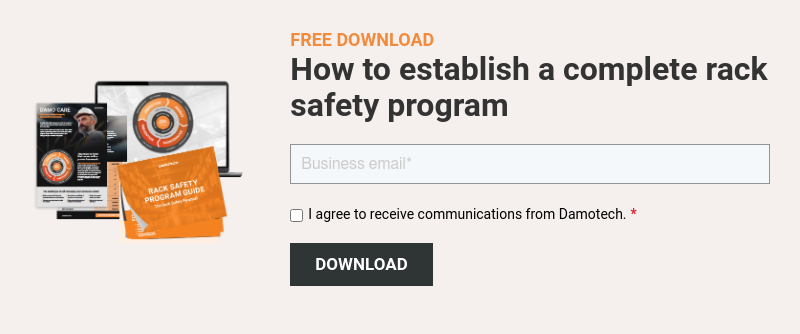
References
Heinrich, H.W. (1931). Industrial Accident Prevention: A Scientific Approach.
Accident triangle - Wikipedia
SafetyStratus: Beyond Heinrich’s Triangle